מדריך מלא להבנה והפחתת רעידות בציוד תעשייתי
ידע בסיסי להבטחת אמינות, יעילות ובטיחות של פעולות תעשייתיות
1.1 מבוא: מדוע לא ניתן להתעלם מרעידות ציוד
בעולם הייצור התעשייתי, רטט הוא בן לוויה בלתי נמנע של ציוד פעיל. עם זאת, קיים גבול קריטי בין רטט תפעולי רגיל לרטט בעייתי שחשוב להבין ולשלוט בו. רטט של מכונות ומנגנונים מייצג תופעה פיזיקלית מורכבת שיכולה לשמש הן כאינדיקטור לתפקוד תקין והן כמבשר לבעיות טכניות חמורות.
חשיבות קריטית של ניטור רעידות
נתונים סטטיסטיים ממפעלים תעשייתיים מראים כי עד 85% מכלל כשלי הציוד המסתובב מלווים בשינויים במאפייני הרטט זמן רב לפני התקלה בפועל. משמעות הדבר היא שניטור רטט נכון יכול למנוע את הרוב המכריע של השבתות ייצור לא מתוכננות.
רטט הוא לעתים קרובות הסימן הראשון, הנשמע או המוחשי, לכך שמשהו לא בסדר בציוד. האוזן האנושית מסוגלת להבחין בשינויים במאפיינים האקוסטיים של מכונות מפעילות, אשר שימשו באופן היסטורי כשיטת האבחון העיקרית עבור מכונאים ומפעילים מנוסים. עם זאת, הדרישות המודרניות לדיוק ואמינות אבחון עולות בהרבה על יכולותיהם של החושים האנושיים.
בעוד שרמה מסוימת של רעידות היא טבועה בפעולתם של מכשירים רבים והיא תוצאה טבעית של תהליכים דינמיים במנגנונים, רעידות מוגזמות הן סימפטום ברור לבעיות בסיסיות שעלולות להוביל לתוצאות חמורות. חשוב להבין שהגבול בין רעידות רגילות לרעידות בעייתיות אינו ערך מוחלט, אלא תלוי בגורמים רבים, כולל סוג הציוד, תנאי ההפעלה, גיל המכונה ודרישות הדיוק לפעולות המבוצעות.
עקרון האיזון המונע
כפי שנאמר בצדק בספרות הטכנית: "איזון הוא מניעה". עיקרון זה מדגיש את האמת הבסיסית של תחזוקה תעשייתית: מניעת בעיות תמיד יעילה וחסכונית יותר מאשר פתרון לאחר מכן.
אם חלק אינו מאוזן כראוי, ייווצרו בהכרח כוחות הגורמים לתנודות, רעש ובלאי מואץ של הרכיבים. תהליך זה מתפתח על פי חוק האקספוננציאל: חוסר איזון ראשוני קטן לאורך זמן מוביל למרווחים מוגברים במיסבים, מה שבתורו מחמיר את הרטט ומאיץ את הבלאי הנוסף. לפיכך, נוצר מעגל קסמים של התדרדרות הציוד.
לכן, הבנה וניהול של רעידות הן בסיס בסיסי להבטחת אמינות, יעילות ובטיחות של פעולות תעשייתיות. תהליכי ייצור מודרניים מאופיינים ברמה גבוהה של אוטומציה ואינטגרציה, מה שאומר שכשל של רכיב אחד יכול לשתק את כל השרשרת הטכנולוגית. בתנאים כאלה, העלות של התעלמות מבעיות רעידות יכולה להיות קטסטרופלית.
יש להבחין בין רעידות תפעוליות רגילות לבין רעידות בעייתיות וסימפטומטיות. רעידות רגילות מאופיינות בפרמטרים יציבים לאורך זמן, מאפייני תדר צפויים הקשורים לתדרי הפעולה של הציוד, ואמפליטודות שאינן חורגות מהסטנדרטים שנקבעו. רעידות בעייתיות, לעומת זאת, מתבטאות בחוסר יציבות של פרמטרים, הופעת רכיבי תדר חדשים, עלייה חדה באמפליטודה או שינויים ביחסי הפאזה.
קישור רעידות בעייתיות לתוצאות שליליות כגון בלאי, כשלים ועלויות יוצר תחושה של דחיפות ורלוונטיות עבור אנשי צוות טכני. סטטיסטיקות מראות כי השבתות ייצור לא מתוכננות עולות בממוצע פי 50-100 יותר מתחזוקה מתוכננת. יתר על כן, ניתן למנוע את רוב ההשבתות הללו באמצעות אבחון רעידות בזמן.
טכנולוגיות מודרניות מאפשרות לא רק לזהות בעיות בשלב מוקדם, אלא גם לחזות התפתחות פגמים, לתכנן זמן התערבות אופטימלי ולמזער את ההשפעה על תהליך הייצור. זה חשוב במיוחד בתנאי תחרות עזה, שבהם כל שעה של השבתה יכולה להוביל לאובדן מעמד בשוק.
הצדקה כלכלית לניטור רעידות
מחקרים מראים שכל דולר שמושקע במערכת ניטור רעידות מביא לחיסכון של 5 עד 20 דולר באמצעות מניעת מצבי חירום, אופטימיזציה של תכנון תיקונים והגדלת מרווחי התחזוקה.
חשוב גם לקחת בחשבון את הגורם האנושי בענייני בטיחות. רעידות מוגזמות עלולות ליצור אי נוחות למפעילים, להפחית את הפרודוקטיביות והריכוז שלהם, מה שמגביר את הסיכון לתאונות. בנוסף, חשיפה ממושכת לרעידות עלולה להוביל למחלות תעסוקתיות, וליצור סיכונים משפטיים וכלכליים נוספים עבור הארגון.
בהקשר של דרישות מודרניות לאחריות סביבתית של ארגונים, בקרת רעידות ממלאת גם תפקיד חשוב בהפחתת ההשפעה הסביבתית. הפעלה אופטימלית של ציוד צורכת פחות אנרגיה, מייצרת פחות רעש ופליטות, דבר התואם את עקרונות הפיתוח בר-קיימא ויכול להיות גורם חשוב בעת קבלת אישורים והיתרים סביבתיים.
1.2 מדע הרטט המכני: מושגים מרכזיים
ויברציה מכנית מייצגת תופעה פיזיקלית מורכבת שניתן להגדירה כתנודה של גוף או מערכת מכניים סביב מיקום שיווי משקל. הגדרה זו, למרות שהיא נראית פשוטה, מסתירה ניואנסים ומורכבויות רבות, שהבנתן חשובה ביותר לאבחון יעיל וניהול ויברציות בציוד תעשייתי.
כאשר: x(t) - תזוזה בזמן, A - משרעת, ω - תדירות זוויתית, φ - פאזה
מספר פרמטרים בסיסיים משמשים לתיאור והערכה כמותית של רעידות, שכל אחד מהם נושא מידע אבחוני חשוב. הבנת פרמטרים אלה והקשרים ההדדיים ביניהם היא הבסיס לניתוח יעיל של מצב הציוד.
משרעת רטט: אינדיקטור לחומרת הבעיה
משרעת מציינת את גודל הרטט, כלומר, כמה רכיב נע יחסית למצב שיווי המשקל שלו. ניתן למדוד פרמטר זה ביחידות שונות, שכל אחת מהן מתאימה לסוגים מסוימים של ניתוח ואבחון.
תזוזה (בדרך כלל נמדדת במילימטרים או מיקרומטרים) מציגה את הסטייה המקסימלית ממצב שיווי המשקל. פרמטר זה חשוב במיוחד עבור תנודות בתדר נמוך ובניתוח תנודות יסוד. ערכי תזוזה גדולים עשויים להצביע על בעיות בקשיחות המערכת או תופעות תהודה.
מהירות הרטט (נמדדת במ"מ/שנייה או אינץ'/שנייה) היא הפרמטר האוניברסלי ביותר לאבחון רוב הבעיות המכניות בטווח התדרים שבין 10 הרץ ל-1000 הרץ. תקנים בינלאומיים כמו ISO 20816 מבוססים בדיוק על מדידות מהירות רטט. פרמטר זה מתואם היטב עם אנרגיית הרטט, וכתוצאה מכך, עם נזק פוטנציאלי לציוד.
פָּרָמֶטֶר | יחידות | בַּקָשָׁה | טווח תדרים |
---|---|---|---|
תְזוּזָה | מ"מ, מיקרומטר | תנודות בתדר נמוך, חוסר איזון | 2-200 הרץ |
מְהִירוּת | מ"מ/שנייה | אבחון כללי, תקני ISO | 10-1000 הרץ |
תְאוּצָה | מטר/שנייה², גרם | פגמים בתדירות גבוהה, מיסבים | 1000-20000+ הרץ |
תאוצת הרטט (נמדדת ב-m/s² או ביחידות g, כאשר g = 9.81 m/s²) היא הרגישה ביותר לרכיבי רטט בתדר גבוה ומשמשת לאבחון פגמים במיסבים, תיבות הילוכים ומקורות רטט אחרים בתדר גבוה. התאוצה פרופורציונלית לכוח הפועל על המבנה, מה שהופך אותה לחשובה להערכת עומסים מבניים.
אמפליטודה גדולה בדרך כלל מצביעה על בעיה חמורה יותר, אולם חשוב להבין שערכי אמפליטודה מוחלטים חייבים להתפרש בהקשר של סוג הציוד, תנאי ההפעלה ומאפייני מערכת המדידה. לדוגמה, אמפליטודה של רעידות של 5 מ"מ/שנייה עשויה להיות נורמלית עבור מנוע גדול במהירות נמוכה, אך קריטית עבור ציר של מכונת CNC במהירות גבוהה.
תדר רטט: המפתח לזיהוי מקור
תדירות מתייחסת לקצב התרחשות הרעידות ובדרך כלל מתבטאת בהרץ (Hz), התואם למספר המחזורים לשנייה, או במחזורים לדקה (CPM), וזה נוח במיוחד בעת ניתוח ציוד מסתובב מכיוון שהוא קשור ישירות לסיבובים לדקה (RPM).
10 הרץ - 10 קילוהרץ
ניתוח תדרים הוא אחד מכלי האבחון החזקים ביותר מכיוון שסוגים שונים של פגמים מתבטאים בתדרים אופייניים. לדוגמה, חוסר איזון ברוטור מתבטא בתדר סיבוב (1X סל"ד), חוסר יישור של הציר יוצר רטט בתדר סיבוב כפול (2X סל"ד), ופגמים במסבים יוצרים רטט בתדרים ספציפיים בהתאם לגיאומטריית המיסב ולמהירות הסיבוב.
הקשר המתמטי בין סיבובים לדקה לתדירות בהרץ מתבטא בנוסחה פשוטה: f(Hz) = סל"ד/60. קשר זה מאפשר המרה קלה של מהירות סיבוב לתדירות הרמונית בסיסית וניתוח של תדרים מרובים (הרמוניות), אשר לעתים קרובות מכילים מידע אבחוני חשוב.
ניתוח הרמוני באבחון
הופעת הרמוניות משמעותיות (2X, 3X, 4X של תדר סיבוב) מעידה לעתים קרובות על תהליכים לא ליניאריים בציוד, כגון שינוי תנועה, פגיעות או פעימות אווירודינמיות. ניתוח הרכב ההרמוניות מאפשר לאבחן בעיות שאולי אינן ברורות מאליהן בעת ניתוח התדר הבסיסי בלבד.
שלב הרטט: מידע מרחבי על תנועה
פאזה מתארת תנועה ויברציונית של חלק אחד של מכונה יחסית לאחר או לנקודת ייחוס קבועה. פרמטר זה חשוב במיוחד בעת אבחון סוגים מסוימים של חוסר איזון, חוסר יישור ופגמים אחרים המתבטאים ביחסי פאזה אופייניים בין נקודות מדידה שונות.
ניתוח פאזה דורש מדידת רעידות בו זמנית במספר נקודות באמצעות אות ייחוס, בדרך כלל מטכומטר או מהבהב. הפרש פאזה בין נקודות מדידה שונות יכול להצביע על סוג ומיקום הבעיה. לדוגמה, חוסר איזון מאופיין בדרך כלל בתנועה בפאזה של תומכי מיסב, בעוד שחוסר יישור מתבטא בתנועה לא בפאזה.
תנועה בשלב
מאפיין של חוסר איזון מסה, כאשר כל הנקודות נעות באותו כיוון בו זמנית
תנועה מחוץ לפאזה
אופייני לחוסר יישור פיר, כאשר נקודות נעות בכיוונים מנוגדים
תנועה ריבועית
עשוי להצביע על תנועת רוטור אליפטי או שילוב של פגמים
חשיבות מאפייני התדר באבחון
חשוב לציין שבעיות מכניות שונות נוטות להתבטא במאפייני ויברציה ייחודיים, במיוחד בתדרים מסוימים. דפוס זה הוא הבסיס לפיתוח מערכות אבחון מומחיות ואלגוריתמים אוטומטיים לזיהוי פגמים.
תת-הרמוניות (תדרים מתחת לתדר הסיבוב הבסיסי, כגון 0.5X, 0.33X) עשויות להצביע על חוסר יציבות בסיבוב, בעיות במיסבי גלגול או בעיות טריז שמן במיסבי הזזה. הופעת תת-הרמוניות היא לעתים קרובות סימן להתפתחות בעיות חמורות.
הבנת מושגים בסיסיים אלה הכרחית, במיוחד עבור קוראים שאינם מומחים ברעידות אך חייבים להבין את אופי הבעיה כדי לקבל החלטות מושכלות לגבי תחזוקה ותיקון. ידע זה מניח את היסודות לדיונים עתידיים בשיטות ניתוח מורכבות יותר כגון ניתוח ספקטרלי, ניתוח מעטפת וניתוח צפסטרלי.
שלב 1: מדידת פרמטרים בסיסיים
קביעת אמפליטודה, תדירות ופאזה של רטט בנקודות מפתח בציוד
שלב 2: ניתוח ספקטרלי
פירוק אות מורכב לרכיבי תדר כדי לחשוף חתימות פגמים אופייניות
שלב 3: ניתוח מגמות
מעקב אחר שינויים בפרמטרים לאורך זמן כדי לחזות התפתחות פגמים
שלב 4: אבחון משולב
ניתוח מקיף של כל הנתונים הזמינים לקביעה מדויקת של סוג הבעיה וחומרתה
מערכות ניתוח רעידות מודרניות מסוגלות לעבד כמויות עצומות של נתונים בזמן אמת, ולזהות אפילו סימנים חלשים של פגמים מתפתחים. למידת מכונה ובינה מלאכותית משמשות יותר ויותר לזיהוי תבניות אוטומטי באותות רעידות, מה שמשפר משמעותית את דיוק האבחון והמהירות.
1.3 גורמים נפוצים: זיהוי גורמים בסיסיים לרעידות מוגזמות
רעידות מוגזמות בציוד תעשייתי הן לעיתים רחוקות בעיה מבודדת. ככלל, זהו סימפטום של מצב פגום אחד או יותר שיכולים להתפתח באופן עצמאי או באינטראקציה זה עם זה. הבנת גורמים אלו חשובה ביותר לאבחון יעיל ומניעה של כשלים חמורים בציוד.
חוסר איזון: הסיבה הנפוצה ביותר לרעידות
חוסר איזון נוצר עקב פיזור מסה לא אחיד ברכיבים מסתובבים, ויוצר "נקודה כבדה" הגורמת לכוחות צנטריפוגליים וכתוצאה מכך, לרעידות. זוהי אחת הסיבות הנפוצות ביותר לרעידות במנועים, רוטורים, מאווררים, משאבות וציוד מסתובב אחר.
חוסר איזון סטטי
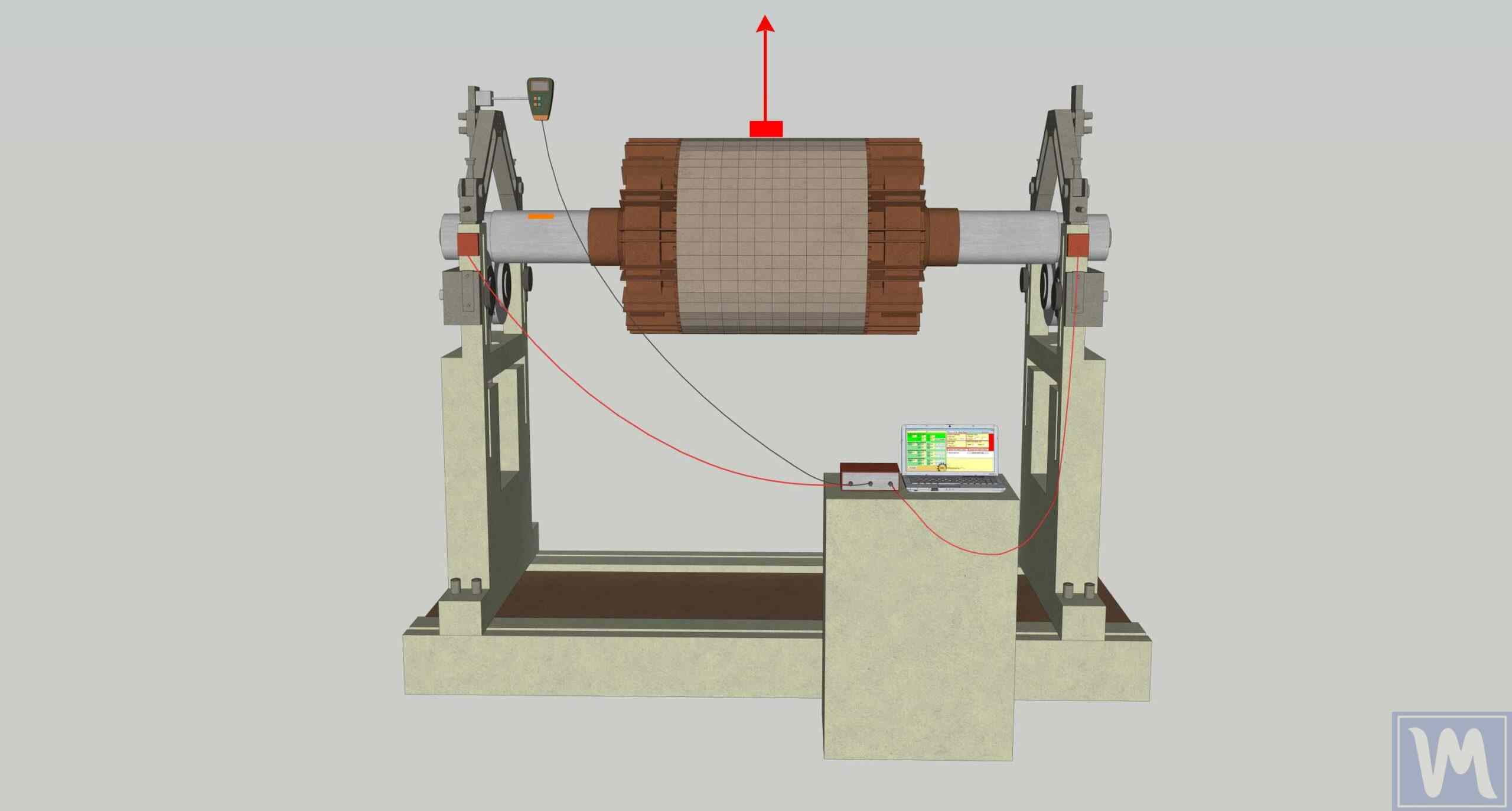
מרכז הכובד אינו חופף לציר הסיבוב. מתבטא במישור אחד וגורם לתנודה רדיאלית בתדירות הסיבוב.
חוסר איזון דינמי
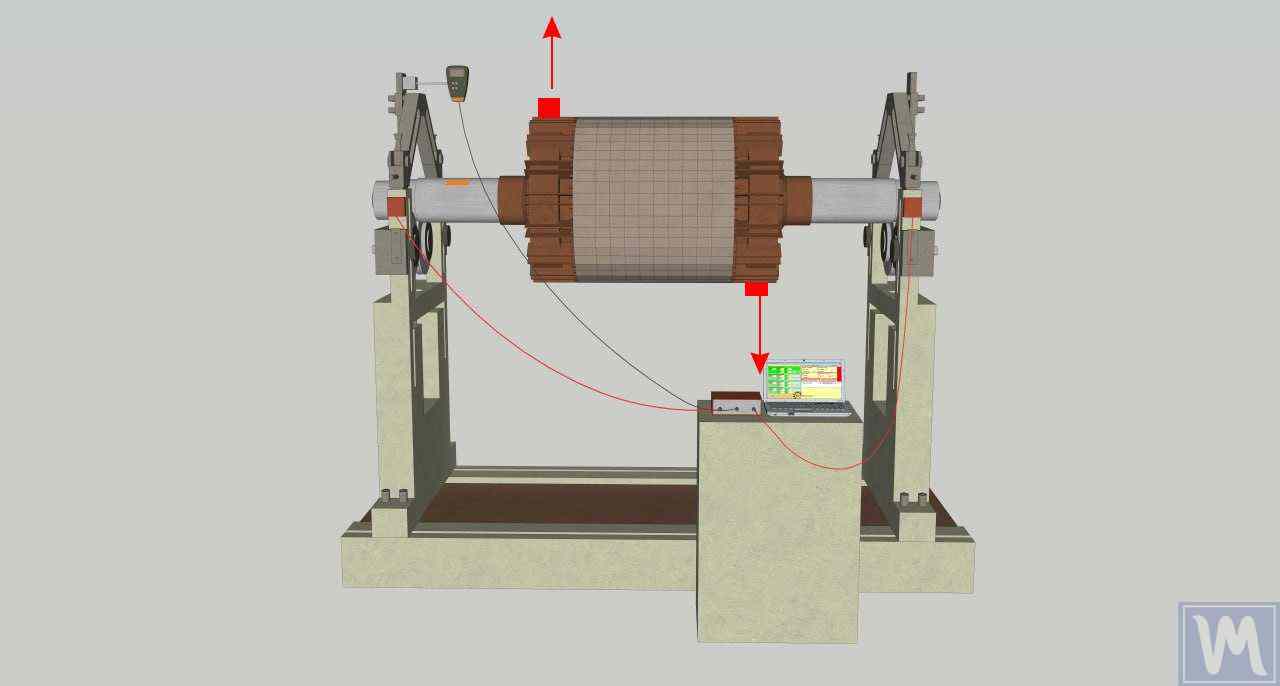
ציר האינרציה אינו חופף לציר הסיבוב. דורש תיקון בשני מישורים ויוצר מומנטים הגורמים לנדנד של הרוטור.
מבחינה מתמטית, כוח צנטריפוגלי הנובע מחוסר איזון מתבטא בנוסחה:
כאשר: m - מסה לא מאוזנת, r - רדיוס חוסר האיזון, ω - מהירות זוויתית
מנוסחה זו, עולה בבירור כי כוח חוסר האיזון הוא פרופורציונלי לריבוע מהירות הסיבוב, מה שמסביר מדוע בעיות חוסר איזון הופכות לחמורות במיוחד במהירויות גבוהות. הכפלת מהירות הסיבוב מובילה לעלייה פי ארבעה בכוח חוסר האיזון.
הגורמים לחוסר איזון מגוונים וכוללים שגיאות ייצור, בלאי לא אחיד, הצטברות זיהום, אובדן משקולות איזון, עיוותים כתוצאה מהשפעות טמפרטורה וקורוזיה. במהלך הפעולה, חוסר האיזון יכול לגדול בהדרגה, מה שמצריך איזון מחדש תקופתי של הציוד.
אופיו המתקדם של חוסר האיזון
חוסר איזון נוטה להיות מחזק את עצמו: חוסר איזון ראשוני גורם לעומסים מוגברים על המיסבים, מה שמוביל לבלאי מואץ שלהם ולמרווחים מוגברים, אשר בתורם מחמירים את חוסר האיזון ויוצרים מעגל קסמים של הידרדרות.
חוסר יישור: איום נסתר על אמינות
חוסר יישור מתרחש כאשר צירים של מכונות מחוברות (למשל, מנוע ומשאבה) מיושרים בצורה שגויה. ישנם שני סוגים עיקריים של חוסר יישור: מקבילי (הסטת ציר) וזוויתי (הצטלבות צירים בזווית). בפועל, חוסר יישור משולב הוא הנפוץ ביותר, כולל שני הסוגים.
חוסר יישור יוצר עומסים מחזוריים על מצמדים, מיסבים וגירים, המתבטאים ברעידות, בעיקר בתדר סיבוב כפול (2X סל"ד). עם זאת, הרמוניות אחרות עשויות להימצא גם כן, בהתאם לסוג ומידת חוסר היישור, כמו גם למאפייני הצימוד.
סוג חוסר יישור | תדרים עיקריים | כיוון הרטט | סימנים אופייניים |
---|---|---|---|
מַקְבִּיל | 2X סל"ד | רַדִיאָלִי | רעידות גבוהות בכיוון רדיאלי |
אנגולר | פי 1, פי 2 סל"ד | צִירִי | רעידות ציריות משמעותיות |
מְשׁוּלָב | פי 1, פי 2, פי 3 סל"ד | רדיאלי + צירי | ספקטרום מורכב עם הרמוניות מרובות |
מגבלות חוסר יישור מקובלות תלויות במהירות הסיבוב ובסוג הציוד. עבור ציוד מדויק במהירות גבוהה, סטיות מקובלות עשויות להיות רק כמה מאיות המילימטר, בעוד שעבור מכונות במהירות נמוכה הסבילות עשויות להיות נדיבות יותר. עם זאת, בכל מקרה, יישור מדויק הוא קריטי לפעולה אמינה וחיי שירות ארוכים של הציוד.
רפיון מכני: מקור לחוסר יציבות
רפיון מכני מרמז על מרווח מוגזם בין רכיבים ויכול להתבטא בצורות שונות: בסיס רופף או ברגי הרכבה, מיסבים שחוקים עם מרווח פנימי גדול מדי, התאמה לקויה של חלקים על הציר, שחיקה של חיבורי מפתח, עיוות של חלקי המארז.
רפיון יכול להגביר מקורות רטט אחרים, ולפעול כמגבר לכוחות חוסר איזון או חוסר יישור. בנוסף, רפיון יכול ליצור השפעות לא ליניאריות כגון פגיעות ודפיקות, אשר יוצרות רטט רחב פס ורכיבים בתדר גבוה.
סימנים אבחנתיים של רפיון
רפיון מתבטא לעיתים קרובות בחוסר יציבות של קריאות הרטט, הופעת תת-הרמוניות וספקטרום מורכב עם שיאים מרובים. סימן אופייני הוא גם תלות של רמת הרטט בעומס הציוד.
פגמי מיסב: אינדיקטורים לבעיות בתדירות גבוהה
בלאי, שקעים או נזק למסבים או לאלמנטים מתגלגלים של מיסבים הם גורם עיקרי לתנודות בתדירות גבוהה. מיסבים מייצרים תדרים אופייניים הקשורים לגיאומטריה ולקינמטיקה שלהם:
BPFI = (n/2) × (1 + d/D × cos α) × RPM/60
BSF = (D/2d) × (1 - (d/D × cos α)²) × RPM/60
FTF = (1/2) × (1 - d/D × cos α) × RPM/60
כאשר: n - מספר אלמנטים מתגלגלים, d - קוטר אלמנט מתגלגל, D - קוטר גובה, α - זווית מגע
נוסחאות אלו מאפשרות חישוב של תדירות פגמים אופיינית במיסבים: BPFO (Ball Pass Frequency Outer Race), BPFI (Ball Pass Frequency Inner Race), BSF (Ball Spin Frequency) ו-FTF (Fundamental Train Frequency).
תהודה: מגבר של כל הבעיות
תהודה מתרחשת כאשר תדר העירור (למשל, מהירות סיבוב או כפולותיה) עולה בקנה אחד עם התדר הטבעי של המכונה או המבנה שלה. זה מוביל להגברת רעידות חדה, אשר יכולה להיות הרסנית בתוצאותיה.
תופעת התהודה
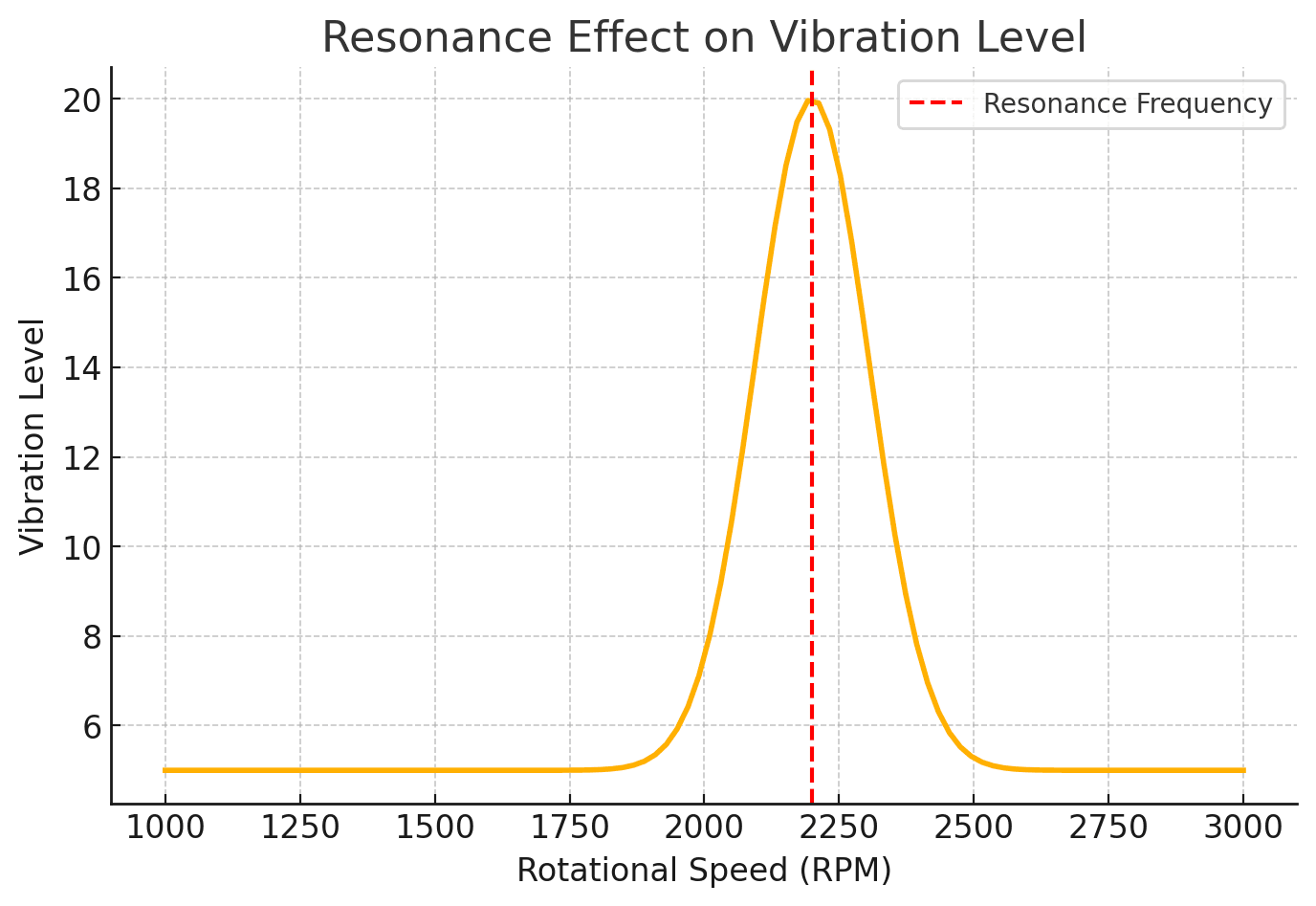
תהודה מגבירה את הרטט כאשר תדר העירור תואם את התדר הטבעי
תופעות תהודה מסוכנות במיוחד במהלך הפעלת וכיבוי הציוד כאשר תדר הסיבוב עובר דרך ערכים קריטיים. מערכות בקרה מודרניות כוללות לעתים קרובות אלגוריתמים למעבר מהיר דרך אזורי תהודה כדי למזער את זמן החשיפה לרעידות מוגברות.
סיבות נוספות לרעידות
מלבד הגורמים העיקריים, ישנם גורמים רבים נוספים שיכולים לגרום לרעידות מוגזמות:
פירים כפופים יוצרים ויברציות בתדר הסיבוב וההרמוניות שלו, כאשר אופי הוויברציה תלוי במידת ובסוג הכיפוף. כיפופים תרמיים יכולים להתרחש עקב חימום או קירור לא אחידים של פירים.
בעיות בתיבת הילוכים כוללים בלאי שיניים, שיניים שבורות או סדוקות, אי דיוקים בייצור, מרווחים שגויים. תיבות הילוכים מייצרות רעידות בתדר רשת (מספר שיניים × סל"ד) ובהרמוניות שלה.
בעיות חשמליות במנועים עשויים לכלול פערי אוויר לא אחידים, מוטות רוטור שבורים, בעיות קומוטציה במנועי DC, חוסר איזון פאזה במנועים תלת פאזיים. בעיות אלו מתבטאות לעיתים קרובות בתדרים הקשורים לתדר רשת החשמל.
גישה מקיפה לאבחון
חשוב להבין שבתנאי הפעלה אמיתיים, קיימים לעיתים קרובות מספר מקורות רטט בו זמנית. אבחון יעיל דורש ניתוח מקיף של כל הגורמים האפשריים והאינטראקציה ביניהן.
מערכות אבחון מודרניות משתמשות בבסיסי נתונים של חתימות פגמים ובמערכות מומחים לזיהוי אוטומטי של צירופי בעיות שונים. זה מאפשר לא רק לזהות את נוכחות הפגם אלא גם להעריך את חומרתו, מהירות ההתפתחות שלו ועדיפות הסילוק שלו.
1.4 אפקט הדומינו: השלכות של רעידות בלתי מבוקרות על יעילות, אורך חיים ובטיחות
התעלמות מרעידות מוגזמות גורמת לתהליך פירוק מדורג שניתן להשוות אותו לאפקט דומינו - אריח נופל אחד מוביל בהכרח לנפילת כל האחרים. בהקשר של ציוד תעשייתי, משמעות הדבר היא שבעיה ראשונית קטנה, שלא מטופלת, עלולה להוביל לתוצאות קטסטרופליות על מערכת הייצור כולה.
בלאי מואץ של רכיבים: החוליה הראשונה בשרשרת ההרס
בלאי מואץ של רכיבים הוא אחת התוצאות הישירות והברורות ביותר של רעידות מוגזמות. תהליך זה משפיע כמעט על כל רכיבי המכונה, אך הפגיעים ביותר הם מיסבים, אטמים, צירים, מצמדים ואפילו יסודות המכונה.
מיסבים רגישים במיוחד לרעידות משום שהן יוצרות עומסים דינמיים נוספים המאיצים את כשל העייפות של המתכת. מחקרים מראים כי הגדלת רמת הרעידות ב-20% בלבד יכולה להפחית את חיי השירות של המיסב ב-40-50%. זה קורה מכיוון שעמידות העייפות של המיסבים היא ביחס הפוך לקובייה של העומס המופעל, לפי משוואת לונדברג-פלמגרן.
אטמים סובלים גם מרעידות משום שהן משבשות את יציבות המגע בין משטחי האיטום. זה מוביל לדליפת חומר סיכה, חדירת זיהום והידרדרות נוספת של תנאי הפעולה של המיסב. סטטיסטיקות מראות כי חיי השירות של האטמים יכולים להתקצר פי 3-5 בנוכחות רעידות משמעותיות.
צירים נתונים למאמצים מחזוריים כתוצאה מרעידות, אשר עלולים להוביל לסדקים עייפים, במיוחד באזורי ריכוז מאמצים כמו אזורי מושב מיסב, חריצי מפתח או מעברים בקוטר. התפתחות סדקי עייפות בצירים מסוכנת במיוחד משום שהיא עלולה להוביל לכשל פתאומי וקטסטרופלי.
אופי הבלאי המתקדם
בלאי רכיבים כתוצאה מרעידות הוא בעל אופי הדרגתי: ככל שמרווחי התנועה במיסבים גדלים, משרעת הרעידות עולה, מה שמאיץ עוד יותר את הבלאי. תהליך זה יכול להתפתח באופן אקספוננציאלי, במיוחד לאחר חריגה מרמת סף מסוימת.
אובדן יעילות תפעולית: הפסדי אנרגיה נסתרים
רעידות מובילות באופן בלתי נמנע לאובדן יעילות תפעולית מכיוון שאנרגיה מתפזרת כתנודות מכניות במקום לבצע עבודה מועילה. זה מוביל לצריכת אנרגיה מוגברת, שיכולה לנוע בין 5% ל-25% בהתאם לחומרת הבעיה וסוג הציוד.
צריכת אנרגיה נוספת נובעת מכמה מקורות:
- הפסדי חיכוך: רעידות מוגברות מגבירות את החיכוך במיסבים ובמשטחי מגע אחרים
- הפסדים אווירודינמיים: תנודות להבי המאוורר והרוטור מפחיתות את יעילותן
- הפסדי כונן: חוסר יישור ופגמים אחרים מגבירים את ההפסדים במצמדים ובתיבות הילוכים
- הפסדי דפורמציה: אנרגיה מבוזבזת על דפורמציות אלסטיות של מבנים
בתהליכי ייצור הדורשים דיוק גבוה, רעידות עלולות לסכן את איכות המוצר הסופי. זה קריטי במיוחד בתעשיות כמו ייצור מוליכים למחצה, עיבוד שבבי מדויק ותעשיית התרופות, שבהן אפילו רעידות מינימליות עלולות להוביל לפגמים במוצר.
השלכות כלכליות: עלויות נסתרות וברורות
עלויות התחזוקה עולות עקב תיקונים תכופים יותר, ובעיקר עקב השבתות לא מתוכננות. נתונים סטטיסטיים ממפעלים תעשייתיים מראים את מבנה העלויות הבא הקשור לבעיות רעידות:
סוג עלות | חלק מההפסדים הכוללים | עלות ממוצעת | אפשרות מניעה |
---|---|---|---|
זמן השבתה לא מתוכנן | 60-70% | $ 50,000-500,000/שעה | 90-95% |
תיקון חירום | 15-20% | פי 3-5 מהעלות המתוכננת | 80-90% |
אובדן איכות המוצר | 10-15% | תלוי בתעשייה | 95-99% |
צריכת אנרגיה מוגברת | 5-10% | 5-25% של תקציב אנרגיה | 85-95% |
כואבים במיוחד הם זמני השבתה לא מתוכננים, שעלותם יכולה להגיע למאות אלפי דולרים לשעה עבור קווי ייצור גדולים. לדוגמה, בתעשייה הפטרוכימית, עצירת יחידת פיצוח יכולה לעלות בין 1 ל-500,000 ל-1,000,000 דולר ליום, לא כולל הפסדים כתוצאה מהפרת התחייבויות חוזיות.
סיכוני בטיחות: איום על כוח אדם וסביבה
ישנם סיכוני בטיחות תעסוקתית חמורים משום שרטט בלתי מבוקר עלול להוביל לכשלים מבניים או קטסטרופליים בציוד עם פוטנציאל לפגיעה בכוח אדם. ההיסטוריה התעשייתית מכירה מקרים רבים בהם התעלמות מבעיות רטט הובילה לתוצאות טרגיות.
דוגמאות לכשלונות קטסטרופליים
כשל הטורבוגנרטור במפעל הכוח של סאיאנו-שושנסקאיה בשנת 2009 היה קשור בחלקו לבעיות רטט. התאונה גרמה למותם של 75 אנשים ולנזקים בשווי מיליארדי רובלים. מקרים כאלה מדגישים את החשיבות הקריטית של ניטור רטט לבטיחות.
סיכוני בטיחות עיקריים כוללים:
- פגיעות מכניות: מחלקים מעופפים של ציוד שנהרס
- שריפות ופיצוצים: מדליפות של נוזלים או גזים דליקים עקב כשל באיטום
- הרעלה כימית: כאשר מורידים לחץ במערכות עם חומרים רעילים
- קריסות מבניות: כאשר יסודות או מבנים תומכים כושלים
רעש מוגזם הנוצר כתוצאה מרעידות גורם גם הוא לדאגות חמורות. הוא משפיע על נוחות המפעיל, מפחית את הריכוז ויכול להוביל למחלות שמיעה תעסוקתיות. חשיפה ממושכת לרעש מעל 85 דציבלים עלולה לגרום לאובדן שמיעה בלתי הפיך, וליצור סיכונים משפטיים למעסיקים.
השלכות סביבתיות: השפעה נסתרת על הסביבה
חוסר יעילות אנרגטית הנגרם כתוצאה מרעידות תורם להשפעה סביבתית שלילית באמצעות פליטות מוגברות של CO₂ וגזי חממה אחרים. עם צריכת אנרגיה שנתית של מפעלים תעשייתיים גדולים של מאות ג'יגה-וואט-שעה, אפילו חוסר יעילות של 5% יכול להוביל לאלפי טונות נוספות של פליטות CO₂.
בנוסף, בעיות רטט עלולות להוביל ל:
- דליפות של נוזלי תהליך לסביבה
- ייצור פסולת מוגבר כתוצאה מבלאי מואץ
- זיהום רעש של השטח שמסביב
- שיבוש יציבות תהליכים טכנולוגיים עם השלכות סביבתיות
מחיר חוסר המעש
ניתוח של מקרים אמיתיים מראה כי עלות ההתעלמות מבעיות רטט יכולה לעלות על עלות ביטולם פי 10-100. יתר על כן, ניתן למנוע את רוב הבעיות באמצעות ניטור קבוע והתערבות בזמן.
השפעה מקיפה על תהליכים עסקיים
תיאור מפורט של כל ההשלכות השליליות הללו מחזק את הצורך בניהול רעידות פרואקטיבי ויוצר הבנה ברורה של ה"צורך" שפתרונות אבחון מודרניים נועדו לספק. חשוב להבין שההשלכות של בעיות רעידות חורגות הרבה מעבר להיבטים טכניים ומשפיעות על כל רמות העסק:
- רמה תפעולית: פרודוקטיביות מופחתת, עלויות תחזוקה מוגברות
- רמה טקטית: שיבוש תוכניות ייצור, בעיות אספקה
- רמה אסטרטגית: אובדן יתרונות תחרותיים, פגיעה במוניטין
מציאות כלכלית מודרנית דורשת מארגונים להשיג יעילות מרבית ולמזער סיכונים. בהקשר זה, ניהול רעידות פרואקטיבי הופך לא רק לצורך טכני אלא ליתרון אסטרטגי שיכול לקבוע הצלחה או כישלון במאבק תחרותי.
1.5 מסלולי אבחון: סקירה כללית של כלים ושיטות לניתוח רעידות
תהליך אבחון הרטט מייצג מתודולוגיה מקיפה המשלבת טכנולוגיות מדידה מתקדמות, אלגוריתמי ניתוח מורכבים וידע מומחה כדי להפוך נתוני רטט "גולמיים" למידע אבחוני בעל ערך. תהליך זה כולל בדרך כלל שלושה שלבים עיקריים: מדידה, ניתוח ופירוש, שכל אחד מהם חשוב ביותר להשגת תוצאות מדויקות ושימושיות.
מְדִידָה
אָנָלִיזָה
פֵּשֶׁר
שלב המדידה: חיישנים כחלון לעולם הרטט
חיישנים הם חוליה ראשונה וחשובה ביותר בשרשרת אבחון הרטט. בעיקר משתמשים במדי תאוצה - התקנים המותקנים על ציוד כדי ללכוד רעידות מכניות ולהמיר אותן לאותות חשמליים. האיכות והמאפיינים של החיישנים משפיעים ישירות על הדיוק והאמינות של תהליך האבחון כולו.
מדי תאוצה מודרניים מחולקים למספר סוגים עיקריים:
פיזואלקטריים
הסוג הנפוץ ביותר. בעל טווח תדרים רחב (עד 50 קילוהרץ), רגישות ויציבות גבוהות. אידיאלי עבור רוב היישומים התעשייתיים.
IEPE (ICP)
חיישנים פיזואלקטריים עם אלקטרוניקה מובנית. מספקים רמת רעש נמוכה וחיבור פשוט. דורשים חשמל ממכשיר מדידה.
MEMS
חיישנים מיקרו-אלקטרומכניים. קומפקטיים, זולים, עמידים בפני זעזועים. מתאימים לניטור רציף ומערכות אלחוטיות.
מאפייני חיישן חשובים ביותר הם:
- רְגִישׁוּת: נמדד בדרך כלל ב-mV/g או pC/g. רגישות גבוהה מאפשרת גילוי אותות חלשים אך עלולה להוביל לעומס יתר עם רטט חזק.
- טווח תדרים: קובע את ספקטרום התדרים שהחיישן יכול למדוד במדויק. לצורך אבחון מיסבים, ייתכן שיידרש טווח של עד 20-50 קילוהרץ.
- טווח דינמי: יחס בין רמת מדידה מקסימלית למינימלית. טווח דינמי רחב מאפשר מדידה של תנודות חלשות וחזקות כאחד.
- יציבות טמפרטורה: חשוב ליישומים תעשייתיים עם טווחי טמפרטורות פעולה רחבים.
מיקום חיישנים: אמנות ומדע
מיקום נכון של החיישנים הוא קריטי לקבלת נתונים מייצגים. יש להתקין חיישנים קרוב ככל האפשר למסבים, בכיוונים של קשיחות מבנית מרבית, ועם חיבור מכני אמין כדי להבטיח העברת רעידות מדויקת.
ויברמטרים: הערכה מהירה של המצב הכללי
מדי ויברציה הם מכשירים ניידים המספקים מדידה כללית של רמת רעידות ושימושיים לבדיקות מהירות של מצב הציוד או למעקב אחר מגמות ארוכות טווח של מצב המכונה הכללי. מכשירים אלה מציגים בדרך כלל פרמטר רעידות אחד או יותר, כגון מהירות RMS או תאוצת שיא.
ויברמטרים מודרניים כוללים לעתים קרובות פונקציות:
- מדידה במספר תחומי תדרים לאיתור גס של הבעיה
- אחסון נתונים לניתוח מגמות
- השוואה עם תקנים קבועים מראש (ISO 20816, ISO 10816)
- ויזואליזציה ספקטרלית פשוטה
- העברת נתונים אלחוטית
פָּרָמֶטֶר | בַּקָשָׁה | ערכי אזעקה אופייניים | פס תדרים |
---|---|---|---|
מהירות RMS | הערכת מצב כללית | 2.8-11.2 מ"מ/שנייה | 10-1000 הרץ |
שיא התאוצה | פגמי פגיעה | 25-100 גרם | 1000-15000 הרץ |
שיא תזוזה | בעיות בתדר נמוך | 25-100 מיקרומטר | 2-200 הרץ |
מנתחי רעידות: אבחון מעמיק
לצורך אבחון מעמיק יותר וזיהוי גורם שורש לרעידות, נעשה שימוש במנתחי רעידות או מנתחי תדרים. מכשירים מורכבים אלה הם מחשבים ייעודיים המותאמים לעיבוד אותות רעידות בזמן אמת.
הבסיס לפעולת האנליזה המודרנית הוא התמרת פורייה מהירה (FFT), אלגוריתם מתמטי המפרק אות זמן מורכב לרכיבי התדר האינדיבידואליים שלו. תהליך זה יוצר ספקטרום רטט - גרף המציג את משרעת הרטט כפונקציה של התדר.
טרנספורמציית פורייה ממירה את אות הזמן x(t) לספקטרום תדרים X(f)
מנתחי רטט מודרניים מציעים פונקציות מתקדמות רבות:
- ניתוח רב-ערוצי: מדידת רעידות בו זמנית במספר נקודות לניתוח פאזות
- FFT ברזולוציה גבוהה: עד 25,600 קווים לניתוח ספקטרלי מפורט
- ניתוח זמן: לכידה וניתוח של תהליכים חולפים
- ניתוח מעטפת: הפקת אותות מווסתים לאבחון מיסבים
- ניתוח צפסטרלי: גילוי מבנים מחזוריים בספקטרום
- ניתוח מסלולי: ויזואליזציה של תנועת פיר במרחב
קריטריונים לבחירת מנתח
בבחירת מנתח רעידות, חשוב לקחת בחשבון לא רק מאפיינים טכניים אלא גם קלות שימוש, איכות תוכנה, יכולות פירוש אוטומטי של תוצאות ושילוב עם מערכות ניהול ארגוניות.
ניתוח צורת גל בזמן: חיפוש אחר תהליכים חולפים
ניתוח צורת גל בזמן הוא שיטה חשובה נוספת, שימושית במיוחד לגילוי פגיעות, תנודות ותופעות לא סטציונריות שאולי אינן נראות בספקטרום התדרים. שיטה זו מאפשרת צפייה באות הרטט בצורתו ה"טבעית" - כפונקציה של זמן.
פרמטרים מרכזיים לניתוח זמן כוללים:
- גורם קרסט: יחס בין ערך השיא לערך ה-RMS. ערכים גבוהים מצביעים על נוכחות פגיעות.
- קורטוזיס: מדד סטטיסטי של "חדות" התפלגות. קורטוזיס מוגברת היא לעתים קרובות סימן מוקדם להתפתחות פגמי מיסב.
- הטיה: מדד של אסימטריה של התפלגות אמפליטודה.
שילוב של שיטות ניתוח שונות
האבחון היעיל ביותר מושג על ידי שילוב של שיטות ניתוח שונות. ניתוח זמן יכול לחשוף את נוכחות הבעיה, ניתוח ספקטרלי יכול לזהות את סוגה, וניתוח פאזה יכול לאתר במדויק את המקור.
מגמות מודרניות בציוד אבחון
פיתוח טכנולוגי מוביל ליכולות חדשות באבחון רעידות:
- מערכות ניטור אלחוטיות: רשתות חיישנים עם העברת חשמל אוטונומית והעברת נתונים אלחוטית
- בינה מלאכותית: זיהוי אוטומטי של דפוסי פגמים וחיזוי כשל
- פלטפורמות ענן: עיבוד נתונים מרכזי מאובייקטים מרובים באמצעות משאבי חישוב גדולים
- אפליקציות מובייל: הפיכת סמארטפונים למנתחי רטט ניידים
- אינטגרציה של IIoT: כולל ניטור רעידות במערכות אינטרנט של הדברים התעשייתיות
יישום כלים ושיטות אלה, ובמיוחד ניתוח FFT, מכין את הקרקע לדיון ביתרונות של יכולות אנליטיות מתוחכמות, באופן אידיאלי ניידות, לאבחון יעיל באתר. אנליזטורים ניידים מודרניים משלבים את כוחן של מערכות נייחות עם נוחות השימוש בשטח, ומאפשרים אבחון מקיף ישירות בציוד.
מדידה בסיסית
שימוש בוויברמטרים פשוטים להערכת רמת הרטט הכללית ולקביעת הצורך בניתוח נוסף
ניתוח ספקטרלי
שימוש בנתחי FFT לזיהוי רכיבי תדר וקביעת סוג הפגם
אבחון מעמיק
שימוש בשיטות ייעודיות (ניתוח מעטפת, צפסטרום, ארובות) לאבחון מדויק של פגמים מורכבים
ניטור משולב
ניטור רציף עם אבחון אוטומטי וחיזוי מבוסס בינה מלאכותית
עתיד אבחון הרטט טמון ביצירת מערכות חכמות המסוגלות לא רק לזהות ולסווג פגמים, אלא גם לחזות את התפתחותם, לייעל את תכנון התחזוקה ולשלב אותן עם מערכות ניהול ארגוניות כלליות כדי למקסם את היעילות התפעולית.
1.6 כוחו של ניהול רעידות פרואקטיבי: יתרונות הגילוי והתיקון המוקדמים
אימוץ גישה פרואקטיבית לניהול רעידות במקום הגישה המסורתית הריאקטיבית של "תיקון לאחר תקלה" מייצג שינוי מהותי בפילוסופיית התחזוקה. גישה זו לא רק מונעת כשלים קטסטרופליים, אלא גם מייעלת את כל מחזור חיי הציוד, והופכת את התחזוקה ממרכז עלות למקור של יתרונות תחרותיים.
חיי שירות מוגברים של ציוד: מתמטיקה של עמידות
ניהול רעידות פרואקטיבי מציע יתרונות משמעותיים רבים, ביניהם בולט חיי שירות ארוכים יותר של רכיבי ציוד. מחקרים מראים שניהול רעידות נכון יכול להאריך את חיי השירות של המסבים ב-200-300%, את האטמים ב-150-200% ואת חיי השירות הכוללים של המכונה ב-50-100%.
שיפורים אלה מבוססים על עקרונות יסוד של כשל עייפות חומרים. על פי משוואת וולר, עמידות העייפות היא ביחס הפוך למשרעת המאמץ, בהספק שעבור רוב המתכות נע בין 3 ל-10. משמעות הדבר היא שאפילו הפחתה קטנה ברמת הרטט יכולה להוביל לעלייה משמעותית בחיי השירות.
כאשר: N - מספר המחזורים עד לכשל, Δσ - משרעת המאמץ, A ו-m - קבועי החומר
שיפור יעילות הציוד הכוללת (OEE)
יעילות הציוד הכוללת (OEE) היא מדד יעילות ייצור מרכזי אשר לוקח בחשבון זמינות, ביצועים ואיכות. ניהול רעידות פרואקטיבי משפיע באופן חיובי על שלושת רכיבי ה-OEE:
- זְמִינוּת: צמצום זמן השבתה לא מתוכנן באמצעות מניעת תקלות חירום
- ביצועים: שמירה על פרמטרי הפעלה ומהירויות אופטימליים
- אֵיכוּת: צמצום פגמים באמצעות יציבות של תהליכים טכנולוגיים
סטטיסטיקות מראות כי ארגונים המיישמים תוכניות מקיפות לניהול רעידות משיגים שיפורים ב-OEE של 5-15%, מה שיכול להביא לרווח נוסף של מיליוני דולרים בשנה עבור מפעל ייצור גדול.
חישוב השפעה כלכלית משיפור OEE
עבור קו ייצור בשווי $10 מיליון עם תפוקה שנתית של $50 מיליון, שיפור OEE של % נותן רווח נוסף של $5 מיליון לשנה, אשר מחזיר את ההשקעות במערכת ניטור רעידות תוך מספר חודשים.
מניעת כשלים חמורים ויקרים
אחד היתרונות המשמעותיים ביותר של גישה פרואקטיבית הוא מניעת כשלים חמורים ויקרים. כשלים מדורגים, כאשר התמוטטות של רכיב אחד מובילה לנזק לחלקי מערכת אחרים, יכולים להיות הרסניים במיוחד הן מבחינה כלכלית והן מבחינה תפעולית.
דוגמה קלאסית היא כשל מיסבים במכונות טורבו במהירות גבוהה: הרס מיסבים יכול להוביל למגע בין הרוטור לסטטור, ולגרום נזק ללהבים, למארז ולצירים, ואף עלול להשפיע על היסודות. עלות כשל מפל כזה יכולה להיות פי 50-100 מעלות החלפת מיסבים בזמן.
סוג ההתערבות | עֲלוּת | זמן השבתה | הסתברות הצלחה |
---|---|---|---|
תחזוקה מונעת | $1,000 | 2-4 שעות | 95-98% |
תיקון מתוכנן | $5,000 | 8-16 שעות | 90-95% |
תיקון חירום | $25,000 | 24-72 שעות | 70-85% |
כשל מפל | $100,000+ | 1-4 שבועות | 50-70% |
הפחתת רעש ורעידות תפעוליות
הפחתה ניכרת ברעש התפעולי היא יתרון נוסף של ניהול יעיל של רעידות. רעש בסביבה תעשייתית לא רק יוצר אי נוחות לעובדים, אלא יכול גם להצביע על בעיות טכניות, להשפיע על דיוק עבודת המפעיל וליצור סיכונים משפטיים הקשורים לדרישות בטיחות תעסוקתית.
הפחתה של 10 דציבלים ברמת הרעש נתפסת על ידי האוזן האנושית כהפחתה כפולה בעוצמה. עבור מתקני ייצור שבהם רמת הרעש יכולה לעלות על 90 דציבלים, אפילו הפחתה קטנה יכולה להיות בעלת השפעה משמעותית על נוחות העבודה ועל תפוקת העובדים.
ניתוח רעידות כבסיס לתחזוקה חזויה
ניתוח רעידות הוא אבן הפינה של תחזוקה חזויה (PdM) - אסטרטגיה שמטרתה לצפות תקלות באמצעות ניטור מצב ציוד רציף או תקופתי. PdM מייצג התפתחות מתחזוקה תגובתית ומונעת לגישה חכמה מבוססת נתונים.
עקרונות מרכזיים של תחזוקה חזויה כוללים:
- ניטור מצב: מדידה רציפה או קבועה של פרמטרים מרכזיים
- ניתוח מגמות: מעקב אחר שינויים לאורך זמן כדי לזהות בעיות מתפתחות
- תחזית: שימוש במודלים סטטיסטיים ולמידת מכונה לחיזוי כשלים
- אופטימיזציה: תכנון התערבויות בזמן אופטימלי בהתחשב בדרישות התפעוליות
מודל כלכלי של תחזוקה חזויה
מחקרים מראים שתחזוקה חזויה יכולה להפחית את עלויות התחזוקה ב-25-30%, להגדיל את זמן הפעולה ב-70-75% ולהאריך את חיי השירות של הציוד ב-20-40%.
גילוי מוקדם ותכנון התערבות
יישום תוכנית ניתוח רעידות מאפשר זיהוי בעיות בשלבים הראשוניים שלהן, כאשר הן עדיין אינן משפיעות על הביצועים אך כבר ניתן לזהות אותן באמצעות שיטות אבחון רגישות. זה מפחית את הסיכון לכיבוי בלתי צפוי ומייעל את תכנון התחזוקה.
עקומת PF (כשל פוטנציאלי-תפקודי) ממחישה את התפתחות הפגם לאורך זמן:
נקודה P - כשל פוטנציאלי
הפגם הופך לניתן לגילוי באמצעות שיטות אבחון אך עדיין אינו משפיע על התפקוד
התפתחות פגמים
הידרדרות הדרגתית במצב עם אפשרות להתערבות תכנונית
סף פונקציונלי
הפגם מתחיל להשפיע על ביצועי הציוד
נקודה ו' - כשל תפקודי
הציוד אינו יכול לבצע את תפקידיו, נדרש תיקון חירום
מרווח הזמן בין שלב הפעולה (PF) לסוגי פגמים שונים יכול לנוע בין מספר ימים למספר חודשים, מה שמספק מספיק זמן לתכנון התערבות אופטימלית.
יתרונות כלכליים ישירים
זה מוביל ישירות להפחתת זמן השבתה וחיסכון משמעותי בעלויות. ניתוח התועלת הכלכלית מראה שכל דולר המושקע במערכת ניטור רעידות מביא לחיסכון של 3 עד 15 דולר, בהתאם לסוג הייצור ולרמת הקריטיות של הציוד.
דרישות טכנולוגיות ליישום מוצלח
כדי לנצל באופן מלא את היתרונות הללו, חשוב ביותר לבצע אבחונים בזמן, מדויקים ולעתים קרובות באתר. היכולת לבצע בדיקות אלו באופן קבוע ויעיל היא המפתח להצלחת כל אסטרטגיית תחזוקה פרואקטיבית.
הדרישות המודרניות לציוד אבחון כוללות:
- הִטַלטְלוּת: יכולת ביצוע מדידות ישירות על הציוד
- דיוק: יכולת לזהות אפילו סימנים חלשים של פגמים מתפתחים
- מהירות ניתוח: עיבוד נתונים מהיר לקבלת החלטות מיידית
- קלות שימוש: ממשק אינטואיטיבי לעובדים בעלי כישורים שונים
- הִשׁתַלְבוּת: תאימות עם מערכות ניהול קיימות
גורמי הצלחה קריטיים
הצלחת תוכנית לניהול רעידות פרואקטיבי תלויה לא רק באיכות הציוד אלא גם בגורמים ארגוניים: הכשרת כוח אדם, יצירת נהלים מתאימים, שילוב עם תכנון הייצור ותמיכה ניהולית.
כלים ניידים מתקדמים מאפשרים קבלת מידע שימושי במהירות, הקלה על קבלת החלטות מושכלות והתערבות מוקדמת. כלים אלה משלבים יכולות אנליטיות מתוחכמות עם פרקטיות של שימוש בשטח, מה שהופך אבחון מתקדם לנגיש למגוון רחב של מומחים טכניים.
עתיד ניהול הרעידות הפרואקטיבי טמון ביצירת מערכות חכמות בעלות למידה עצמית, אשר לא רק מנטרות את מצב הציוד הנוכחי אלא גם מייעלות את פעולתו בזמן אמת, תוך התאמה לתנאי הפעלה משתנים ולדרישות ייצור. זה פותח את הדרך למערכות ייצור אוטונומיות באמת המסוגלות לשמור באופן עצמאי על ביצועיהן האופטימליים.
סיכום: דרך לייצור אמין ויעיל
הבנה וניהול של רעידות בציוד תעשייתי מייצגים לא רק הכרח טכני אלא בסיס אסטרטגי להשגת מצוינות תפעולית בעולם התחרותי של ימינו. אבחון רעידות נכון משפיע לא רק על האמינות הטכנית של הציוד אלא גם על היעילות הכלכלית, בטיחות העובדים והאחריות הסביבתית של הארגון.
השקעות במערכות ניטור וניתוח רעידות מודרניות משתלמות פי כמה באמצעות מניעת תאונות יקרות, אופטימיזציה של תכנון תחזוקה ושיפור יעילות הציוד הכוללת. עתיד הייצור התעשייתי שייך לארגונים שיכולים להפוך נתונים על מצב הציוד שלהם ליתרונות תחרותיים.
0 הערות