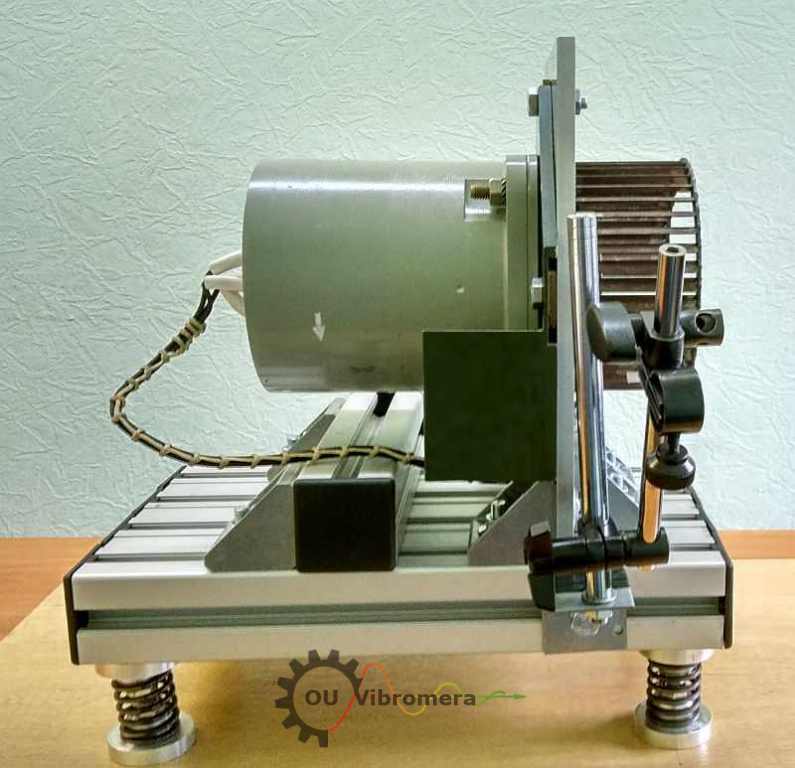
Fan balancing machine based on the Balanset-1A vibration analyzer.
इलेक्ट्रिक मोटर रोटर संतुलन: उत्तम परिणाम के लिए 5 आवश्यक चरण
मरम्मत के बाद प्रदर्शन अनुकूलन के लिए व्यावसायिक इलेक्ट्रिक मोटर रोटर संतुलन पद्धति
Table of Contents
इलेक्ट्रिक मोटर रोटर संतुलन क्यों महत्वपूर्ण है
इलेक्ट्रिक मोटर रोटर संतुलन मोटर की कार्यक्षमता और दीर्घायु के लिए मौलिक है। मरम्मत हस्तक्षेप के बाद, इलेक्ट्रिक मोटर रोटर अक्सर असंतुलन प्रदर्शित करते हैं जो दक्षता और परिचालन जीवनकाल को काफी कम कर देता है। मोटर मरम्मत उद्यम लगातार विभिन्न औद्योगिक अनुप्रयोगों में इस इलेक्ट्रिक मोटर रोटर संतुलन चुनौती का सामना करते हैं।
यह व्यापक गाइड विशेष उपकरणों और प्रक्रियाओं का उपयोग करके सिद्ध इलेक्ट्रिक मोटर रोटर संतुलन पद्धति को प्रदर्शित करता है। उचित इलेक्ट्रिक मोटर रोटर संतुलन प्रभावी मोटर प्रदर्शन सुनिश्चित करता है, रखरखाव लागत को कम करता है, और उपकरण जीवन को बढ़ाता है।
इलेक्ट्रिक मोटर रोटर संतुलन उपकरण के लिए व्यावसायिक मामला
इलेक्ट्रिक मोटर रोटर बैलेंसिंग कई परिचालन समस्याओं को संबोधित करता है जो प्रदर्शन और लाभप्रदता को प्रभावित करते हैं। असंतुलित रोटर यांत्रिक तनाव, ऊर्जा की बर्बादी और समय से पहले घटक विफलता पैदा करते हैं। पेशेवर इलेक्ट्रिक मोटर रोटर बैलेंसिंग उपकरण मोटर मरम्मत उद्यमों के लिए लागत प्रभावी समाधान प्रदान करता है।
इलेक्ट्रिक मोटर रोटर संतुलन द्वारा हल की जाने वाली प्रमुख समस्याएं:
असंतुलित रोटर के कारण समय से पहले बेयरिंग खराब हो जाती है, जिसके कारण बार-बार प्रतिस्थापन की आवश्यकता पड़ती है और महंगा डाउनटाइम होता है।
उचित रूप से संतुलित मोटरों की तुलना में खराब विद्युत मोटर रोटर संतुलन से ऊर्जा खपत 15% तक बढ़ जाती है।
गंभीर रोटर असंतुलन के कारण मोटर में भयंकर खराबी आ जाती है, जिसके कारण आपातकालीन मरम्मत और उत्पादन बंद करने की आवश्यकता पड़ती है।
इंस्टीट्यूट ऑफ इलेक्ट्रिकल एंड इलेक्ट्रॉनिक्स इंजीनियर्स के अनुसार, उचित इलेक्ट्रिक मोटर रोटर संतुलन असंतुलित मोटरों की तुलना में मोटर के जीवन को 200-300% तक बढ़ा सकता है। यह लाभदायक मोटर मरम्मत कार्यों के लिए इलेक्ट्रिक मोटर रोटर संतुलन को आवश्यक बनाता है।
स्प्रिंग डैम्पर्स के साथ इलेक्ट्रिक मोटर रोटर संतुलन सेटअप
आवश्यक इलेक्ट्रिक मोटर रोटर संतुलन सेटअप आवश्यकताएँ
प्रभावी इलेक्ट्रिक मोटर रोटर संतुलन के लिए बेलनाकार स्प्रिंग डैम्पर्स पर स्थित वेल्डेड फ्रेम निर्माण की आवश्यकता होती है। यह विन्यास संतुलन प्रक्रिया को पर्यावरणीय कंपन से अलग करता है जो माप सटीकता से समझौता कर सकता है। स्प्रिंग डैम्पर सिस्टम पेशेवर इलेक्ट्रिक मोटर रोटर संतुलन संचालन की नींव बनाता है।
3 महत्वपूर्ण इलेक्ट्रिक मोटर रोटर संतुलन विन्यास लाभ
1. बाहरी कंपन अलगाव
स्प्रिंग डैम्पर्स इलेक्ट्रिक मोटर रोटर बैलेंसिंग को बाहरी कंपन और गड़बड़ी से अलग करते हैं। यह अलगाव इलेक्ट्रिक मोटर रोटर बैलेंसिंग प्रक्रिया के दौरान माप सटीकता सुनिश्चित करता है।
2. अनुनाद नियंत्रण
उचित अवमंदन अनुनादी स्थितियों को समाप्त करता है जो विद्युत मोटर रोटर संतुलन सटीकता से समझौता करते हैं, तथा पूरी प्रक्रिया के दौरान स्थिर माप स्थितियों को सुनिश्चित करता है।
3. क्रिटिकल फ़्रीक्वेंसी ट्यूनिंग
इष्टतम विद्युत मोटर रोटर संतुलन परिणामों के लिए फ्रेम दोलनों की प्राकृतिक आवृत्ति रोटर घूर्णन आवृत्ति से 2-3 गुना कम होनी चाहिए।
5-चरणीय इलेक्ट्रिक मोटर रोटर संतुलन पद्धति
विस्तृत इलेक्ट्रिक मोटर रोटर संतुलन प्रक्रिया
- सेटअप चरण: स्थिर विद्युत मोटर रोटर संतुलन स्थितियों के लिए उचित फ्रेम समर्थन के साथ इलेक्ट्रिक मोटर को स्प्रिंग डैम्पर स्टैंड पर माउंट करें।
- आवृत्ति सत्यापन: पुष्टि करें कि प्राकृतिक आवृत्ति सटीक विद्युत मोटर रोटर संतुलन माप के लिए 2-3x कम आवश्यकता को पूरा करती है।
- प्रारंभिक माप: विद्युत मोटर रोटर संतुलन प्रक्रिया शुरू करने से पहले आधारभूत कंपन स्तर रिकॉर्ड करें।
- संतुलन अनुप्रयोग: इष्टतम विद्युत मोटर रोटर संतुलन के लिए कंपन विश्लेषण के आधार पर गणना किए गए सुधार भार को लागू करें।
- अंतिम सत्यापन: पुष्टि करें कि विद्युत मोटर रोटर संतुलन ने 0.3-0.7 मिमी/सेकेंड के लक्ष्य कंपन स्तर को प्राप्त कर लिया है।
इलेक्ट्रिक मोटर रोटर संतुलन परिणाम और प्रदर्शन
व्यावसायिक इलेक्ट्रिक मोटर रोटर संतुलन परिणाम
उचित विद्युत मोटर रोटर संतुलन के माध्यम से लगातार अवशिष्ट कंपन स्तर प्राप्त किया जाता है
जब उचित परिस्थितियाँ बनाए रखी जाती हैं, तो व्यावसायिक इलेक्ट्रिक मोटर रोटर संतुलन लगातार सकारात्मक परिणाम देता है। विशेष उपकरणों के साथ मापा गया संतुलन के बाद अवशिष्ट कंपन स्तर 0.3-0.7 मिमी/सेकंड की सीमा के भीतर आता है, जो सफल इलेक्ट्रिक मोटर रोटर संतुलन पूरा होने का संकेत देता है।
ये इलेक्ट्रिक मोटर रोटर संतुलन परिणाम मोटर अनुप्रयोगों में उच्च गुणवत्ता वाले संतुलन स्तरों का प्रतिनिधित्व करते हैं। उचित रूप से संतुलित मोटर समय से पहले खराब होने या विफलताओं की कम संवेदनशीलता के साथ कुशलतापूर्वक कार्य करते हैं। मोटर प्रदर्शन पर उद्योग मानकों के लिए, अंतर्राष्ट्रीय इलेक्ट्रोटेक्निकल कमीशन के दिशा-निर्देशों से परामर्श करें।
3 प्रमुख इलेक्ट्रिक मोटर रोटर संतुलन प्रदर्शन लाभ
उन्नत मोटर प्रदर्शन
विद्युत मोटर रोटर संतुलन सभी परिचालन स्थितियों में इष्टतम विद्युत उत्पादन और कम ऊर्जा खपत के साथ कुशल संचालन सुनिश्चित करता है।
विस्तारित मोटर जीवनकाल
उचित विद्युत मोटर रोटर संतुलन से बियरिंग, वाइंडिंग और यांत्रिक घटकों पर घिसाव कम हो जाता है, जिससे परिचालन जीवन में काफी वृद्धि होती है।
आर्थिक लाभ
इलेक्ट्रिक मोटर रोटर संतुलन रखरखाव लागत को कम करता है, डाउनटाइम को कम करता है, और मरम्मत उद्यमों के लिए दीर्घकालिक लागत बचत प्रदान करता है।
इलेक्ट्रिक मोटर रोटर संतुलन तकनीकी आवश्यकताएँ
इलेक्ट्रिक मोटर रोटर संतुलन पैरामीटर | मांग | इकाई |
---|---|---|
अवशिष्ट कंपन स्तर | 0.3 - 0.7 | मिमी/सेकेंड |
प्राकृतिक आवृत्ति अनुपात | 2-3 गुना कम | रोटर RPM से अधिक |
स्टैंड निर्माण | वेल्डेड फ्रेम | - |
डैम्पर प्रकार | बेलनाकार स्प्रिंग | - |
उन्नत इलेक्ट्रिक मोटर रोटर संतुलन संबंधी विचार
सफल इलेक्ट्रिक मोटर रोटर संतुलन के लिए रोटर द्रव्यमान वितरण, घूर्णन गति और कंपन विशेषताओं के बीच संबंध को समझना आवश्यक है। इलेक्ट्रिक मोटर रोटर संतुलन को लागू करने वाली मोटर मरम्मत सुविधाओं को सुसंगत परिणामों के लिए पर्यावरणीय कारकों, उपकरण अंशांकन और ऑपरेटर प्रशिक्षण पर विचार करना चाहिए।
गुणवत्तापूर्ण इलेक्ट्रिक मोटर रोटर बैलेंसिंग भी उचित माप तकनीकों और डेटा व्याख्या पर निर्भर करता है। आधुनिक संतुलन उपकरण सुधार वजन प्लेसमेंट के लिए सटीक गणना प्रदान करता है, जिससे इष्टतम इलेक्ट्रिक मोटर रोटर बैलेंसिंग परिणाम सुनिश्चित होते हैं। संतुलन उपकरण का नियमित अंशांकन इलेक्ट्रिक मोटर रोटर बैलेंसिंग संचालन में सटीकता और विश्वसनीयता बनाए रखता है।
इलेक्ट्रिक मोटर रोटर संतुलन सर्वोत्तम अभ्यास
मरम्मत हस्तक्षेप के बाद इलेक्ट्रिक मोटर रोटर संतुलन कुशल और लंबे समय तक मोटर संचालन सुनिश्चित करता है। विशेष संतुलन उपकरण और स्प्रिंग डैम्पर स्टैंड का उपयोग करने वाली यह पद्धति विभिन्न मोटर प्रकारों और अनुप्रयोगों में सुसंगत, विश्वसनीय इलेक्ट्रिक मोटर रोटर संतुलन परिणाम प्रदान करती है।
वांछित इलेक्ट्रिक मोटर रोटर संतुलन परिणाम प्राप्त करने के लिए आवृत्ति ट्यूनिंग आवश्यकताओं का पालन सर्वोपरि रहता है। 0.3-0.7 मिमी/सेकंड अवशिष्ट कंपन स्तरों की लगातार उपलब्धि उचित रूप से कार्यान्वित किए जाने पर पेशेवर इलेक्ट्रिक मोटर रोटर संतुलन प्रक्रियाओं की प्रभावशीलता को प्रदर्शित करती है।
इस इलेक्ट्रिक मोटर रोटर संतुलन पद्धति को लागू करने वाले मोटर मरम्मत उद्यम बेहतर मोटर प्रदर्शन प्राप्त करते हैं और कम घिसाव, बढ़ी हुई मोटर जीवन अवधि और बेहतर परिचालन दक्षता के माध्यम से महत्वपूर्ण दीर्घकालिक आर्थिक लाभ प्राप्त करते हैं। उचित इलेक्ट्रिक मोटर रोटर संतुलन मोटर विश्वसनीयता और प्रदर्शन में एक महत्वपूर्ण निवेश का प्रतिनिधित्व करता है।