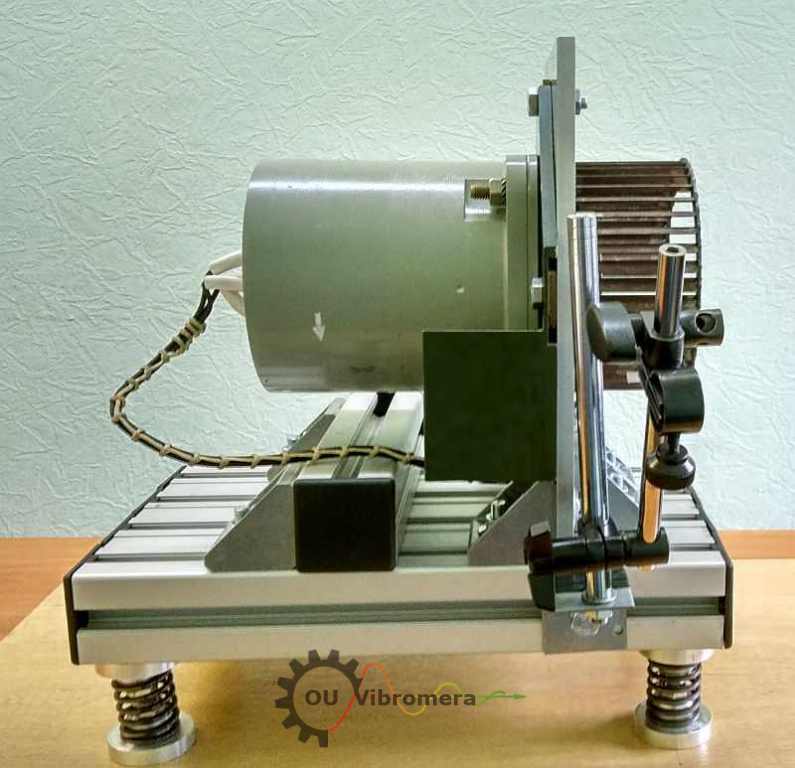
Fan balancing machine based on the Balanset-1A vibration analyzer.
Electric Motor Rotor Balancing: 5 Essential Steps for Perfect Results
Professional electric motor rotor balancing methodology for post-repair performance optimization
Table of Contents
- Why Electric Motor Rotor Balancing is Critical
- The Business Case for Electric Motor Rotor Balancing Equipment
- Electric Motor Rotor Balancing Setup with Spring Dampers
- 5-Step Electric Motor Rotor Balancing Methodology
- Electric Motor Rotor Balancing Results and Performance
- Electric Motor Rotor Balancing Best Practices
Why Electric Motor Rotor Balancing is Critical
Electric motor rotor balancing is fundamental to motor functionality and longevity. After repair interventions, electric motor rotors often exhibit imbalances that significantly reduce efficiency and operational lifespan. Motor repair enterprises consistently encounter this electric motor rotor balancing challenge across various industrial applications.
This comprehensive guide demonstrates proven electric motor rotor balancing methodology using specialized equipment and procedures. Proper electric motor rotor balancing ensures effective motor performance, reduces maintenance costs, and extends equipment life.
The Business Case for Electric Motor Rotor Balancing Equipment
Electric motor rotor balancing addresses multiple operational problems that impact performance and profitability. Unbalanced rotors create mechanical stress, energy waste, and premature component failure. Professional electric motor rotor balancing equipment provides cost-effective solutions for motor repair enterprises.
Key Problems Solved by Electric Motor Rotor Balancing:
Unbalanced rotors cause premature bearing failure, requiring frequent replacement and causing costly downtime.
Poor electric motor rotor balancing increases energy consumption by up to 15% compared to properly balanced motors.
Severe rotor imbalances lead to catastrophic motor failure, requiring emergency repairs and production shutdowns.
According to the Institute of Electrical and Electronics Engineers, proper electric motor rotor balancing can extend motor life by 200-300% compared to unbalanced motors. This makes electric motor rotor balancing essential for profitable motor repair operations.
Electric Motor Rotor Balancing Setup with Spring Dampers
Essential Electric Motor Rotor Balancing Setup Requirements
Effective electric motor rotor balancing requires a welded frame construction positioned on cylindrical spring dampers. This configuration isolates the balancing process from environmental vibrations that could compromise measurement accuracy. The spring damper system forms the foundation of professional electric motor rotor balancing operations.
3 Critical Electric Motor Rotor Balancing Configuration Advantages
1. External Vibration Isolation
Spring dampers isolate electric motor rotor balancing from external vibrations and disturbances. This isolation ensures measurement accuracy during the electric motor rotor balancing procedure.
2. Resonance Control
Proper damping eliminates resonant conditions that compromise electric motor rotor balancing accuracy, ensuring stable measurement conditions throughout the procedure.
3. Critical Frequency Tuning
The natural frequency of frame oscillations must be 2-3 times lower than rotor rotational frequency for optimal electric motor rotor balancing results.
5-Step Electric Motor Rotor Balancing Methodology
Detailed Electric Motor Rotor Balancing Procedure
- Setup Phase: Mount the electric motor on the spring damper stand with proper frame support for stable electric motor rotor balancing conditions.
- Frequency Verification: Confirm the natural frequency meets the 2-3x lower requirement for accurate electric motor rotor balancing measurements.
- Initial Measurement: Record baseline vibration levels before beginning the electric motor rotor balancing procedure.
- Balancing Application: Apply calculated correction weights based on vibration analysis for optimal electric motor rotor balancing.
- Final Verification: Confirm electric motor rotor balancing achieved target vibration levels of 0.3-0.7 mm/s.
Electric Motor Rotor Balancing Results and Performance
Professional Electric Motor Rotor Balancing Results
Consistent residual vibration levels achieved through proper electric motor rotor balancing
Professional electric motor rotor balancing consistently delivers positive results when proper conditions are maintained. Post-balancing residual vibration levels measured with specialized equipment fall within the 0.3-0.7 mm/s range, indicating successful electric motor rotor balancing completion.
These electric motor rotor balancing results represent high-quality balance levels in motor applications. Properly balanced motors function efficiently with reduced susceptibility to premature wear or failures. For industry standards on motor performance, consult the International Electrotechnical Commission guidelines.
3 Major Electric Motor Rotor Balancing Performance Benefits
Enhanced Motor Performance
Electric motor rotor balancing ensures efficient operation with optimal power output and reduced energy consumption across all operating conditions.
Extended Motor Lifespan
Proper electric motor rotor balancing minimizes wear on bearings, windings, and mechanical components, extending operational life significantly.
Economic Benefits
Electric motor rotor balancing reduces maintenance costs, decreases downtime, and provides long-term cost savings for repair enterprises.
Electric Motor Rotor Balancing Technical Requirements
Electric Motor Rotor Balancing Parameter | Requirement | Unit |
---|---|---|
Residual Vibration Level | 0.3 - 0.7 | mm/s |
Natural Frequency Ratio | 2-3 times lower | than rotor RPM |
Stand Construction | Welded frame | - |
Damper Type | Cylindrical spring | - |
Advanced Electric Motor Rotor Balancing Considerations
Successful electric motor rotor balancing requires understanding the relationship between rotor mass distribution, rotational speed, and vibration characteristics. Motor repair facilities implementing electric motor rotor balancing must consider environmental factors, equipment calibration, and operator training for consistent results.
Quality electric motor rotor balancing also depends on proper measurement techniques and data interpretation. Modern balancing equipment provides precise calculations for correction weight placement, ensuring optimal electric motor rotor balancing outcomes. Regular calibration of balancing equipment maintains accuracy and reliability in electric motor rotor balancing operations.
Electric Motor Rotor Balancing Best Practices
Electric motor rotor balancing after repair interventions ensures efficient and prolonged motor operation. This methodology using specialized balancing equipment and spring damper stands provides consistent, reliable electric motor rotor balancing results across various motor types and applications.
Adherence to frequency tuning requirements remains paramount for achieving desired electric motor rotor balancing outcomes. The consistent achievement of 0.3-0.7 mm/s residual vibration levels demonstrates the effectiveness of professional electric motor rotor balancing procedures when properly implemented.
Motor repair enterprises implementing this electric motor rotor balancing methodology achieve enhanced motor performance and realize significant long-term economic benefits through reduced wear, increased motor lifespan, and improved operational efficiency. Proper electric motor rotor balancing represents a critical investment in motor reliability and performance.