راهنمای کامل درک و کاهش ارتعاش در تجهیزات صنعتی
دانش بنیادی برای تضمین قابلیت اطمینان، کارایی و ایمنی عملیات صنعتی
۱.۱ مقدمه: چرا نمیتوان ارتعاش تجهیزات را نادیده گرفت
در دنیای تولید صنعتی، ارتعاش همراه اجتنابناپذیر تجهیزات در حال کار است. با این حال، مرز بحرانی بین ارتعاش عملیاتی عادی و ارتعاش مشکلساز وجود دارد که درک و کنترل آن مهم است. ارتعاش ماشینآلات و مکانیزمها یک پدیده فیزیکی پیچیده است که میتواند هم به عنوان شاخص عملکرد طبیعی و هم به عنوان نشانهای از مشکلات فنی جدی عمل کند.
اهمیت حیاتی پایش ارتعاش
دادههای آماری از شرکتهای صنعتی نشان میدهد که تا ۸۵۱TP3T از کل خرابیهای تجهیزات دوار، مدتها قبل از خرابی واقعی، با تغییراتی در ویژگیهای ارتعاش همراه هستند. این بدان معناست که نظارت صحیح بر ارتعاش میتواند از اکثریت قریب به اتفاق توقفهای برنامهریزی نشده تولید جلوگیری کند.
لرزش اغلب اولین نشانه شنیداری یا ملموس از وجود مشکل در تجهیزات است. گوش انسان قادر به تشخیص تغییرات در ویژگیهای صوتی ماشینهای در حال کار است، که از نظر تاریخی به عنوان روش تشخیصی اصلی برای مکانیکها و اپراتورهای باتجربه عمل میکرد. با این حال، الزامات مدرن برای دقت و قابلیت اطمینان تشخیصی بسیار فراتر از قابلیتهای حواس انسان است.
اگرچه سطح مشخصی از ارتعاش در ذات عملکرد بسیاری از دستگاهها وجود دارد و نتیجه طبیعی فرآیندهای دینامیکی در مکانیسمها است، اما ارتعاش بیش از حد نشانه بارز مشکلات اساسی است که میتواند منجر به عواقب جدی شود. درک این نکته مهم است که مرز بین ارتعاش طبیعی و مشکلساز یک مقدار مطلق نیست، بلکه به عوامل زیادی از جمله نوع تجهیزات، شرایط عملیاتی، سن دستگاه و الزامات دقت برای عملیات انجام شده بستگی دارد.
اصل تعادل پیشگیرانه
همانطور که به درستی در ادبیات فنی آمده است: «متعادلسازی، پیشگیری است.» این اصل بر حقیقت اساسی نگهداری صنعتی تأکید دارد: پیشگیری از مشکلات همیشه مؤثرتر و اقتصادیتر از حذف بعدی آنهاست.
اگر قطعهای به درستی بالانس نشده باشد، نیروهایی که باعث ارتعاش، سر و صدا و سایش تسریعشدهی قطعه میشوند، ناگزیر ایجاد میشوند. این فرآیند طبق قانون نمایی توسعه مییابد: یک عدم تعادل اولیهی کوچک با گذشت زمان منجر به افزایش لقی در یاتاقانها میشود که به نوبهی خود ارتعاش را تشدید کرده و سایش بیشتر را تسریع میکند. بنابراین، یک چرخهی معیوب از تخریب تجهیزات شکل میگیرد.
بنابراین، درک و مدیریت ارتعاش، پایه و اساس اساسی برای تضمین قابلیت اطمینان، کارایی و ایمنی عملیات صنعتی است. فرآیندهای تولید مدرن با درجه بالایی از اتوماسیون و ادغام مشخص میشوند، به این معنی که خرابی یک عنصر میتواند کل زنجیره فناوری را فلج کند. در چنین شرایطی، هزینه نادیده گرفتن مشکلات ارتعاش میتواند فاجعهبار باشد.
لازم است بین ارتعاش عملیاتی عادی و ارتعاشی که مشکلساز و علامتدار است، تمایز قائل شد. ارتعاش عادی با پارامترهای پایدار در طول زمان، ویژگیهای فرکانسی قابل پیشبینی مربوط به فرکانسهای عملیاتی تجهیزات و دامنههایی که از استانداردهای تعیینشده تجاوز نمیکنند، مشخص میشود. برعکس، ارتعاش مشکلساز از طریق ناپایداری پارامترها، ظهور مؤلفههای فرکانسی جدید، افزایش شدید دامنه یا تغییرات در روابط فازی بروز میکند.
ارتباط دادن ارتعاشات مشکلساز با نتایج منفی مانند سایش، خرابیها و هزینهها، حس فوریت و اهمیت را برای پرسنل فنی ایجاد میکند. آمار نشان میدهد که توقفهای برنامهریزی نشده تولید به طور متوسط ۵۰ تا ۱۰۰ برابر بیشتر از تعمیر و نگهداری برنامهریزی شده هزینه دارند. علاوه بر این، از طریق تشخیص به موقع ارتعاشات میتوان از بیشتر این توقفها جلوگیری کرد.
فناوریهای مدرن نه تنها امکان تشخیص مشکلات در مراحل اولیه را فراهم میکنند، بلکه امکان پیشبینی توسعه نقص، برنامهریزی زمان مداخله بهینه و به حداقل رساندن تأثیر بر فرآیند تولید را نیز فراهم میکنند. این امر به ویژه در شرایط رقابت شدید، جایی که هر ساعت توقف میتواند به معنای از دست دادن موقعیت بازار باشد، اهمیت دارد.
توجیه اقتصادی برای پایش ارتعاش
تحقیقات نشان میدهد که هر دلاری که در سیستم پایش ارتعاش سرمایهگذاری میشود، از طریق پیشگیری از موقعیتهای اضطراری، بهینهسازی برنامهریزی تعمیرات و افزایش فواصل تعمیر و نگهداری، 5 تا 20 دلار صرفهجویی به همراه دارد.
همچنین در نظر گرفتن عامل انسانی در مسائل ایمنی بسیار مهم است. ارتعاش بیش از حد میتواند باعث ناراحتی اپراتورها شود، بهرهوری و توجه آنها را کاهش دهد، که به نوبه خود خطر تصادفات را افزایش میدهد. علاوه بر این، قرار گرفتن طولانی مدت انسان در معرض ارتعاش میتواند منجر به بیماریهای شغلی شود و خطرات قانونی و مالی بیشتری را برای شرکت ایجاد کند.
در چارچوب الزامات مدرن برای مسئولیتپذیری زیستمحیطی شرکتها، کنترل ارتعاش نیز نقش مهمی در کاهش اثرات زیستمحیطی ایفا میکند. تجهیزات با عملکرد بهینه، انرژی کمتری مصرف میکنند، سر و صدا و انتشار گازهای گلخانهای کمتری تولید میکنند که با اصول توسعه پایدار مطابقت دارد و میتواند عامل مهمی در اخذ گواهینامهها و مجوزهای زیستمحیطی باشد.
۱.۲ علم ارتعاشات مکانیکی: مفاهیم کلیدی
ارتعاش مکانیکی یک پدیده فیزیکی پیچیده است که میتوان آن را به عنوان نوسان یک جسم یا سیستم مکانیکی حول یک موقعیت تعادل تعریف کرد. این تعریف، اگرچه ساده به نظر میرسد، اما بسیاری از ظرافتها و پیچیدگیها را پنهان میکند که درک آن برای تشخیص مؤثر و مدیریت ارتعاش در تجهیزات صنعتی بسیار مهم است.
که در آن: x(t) - جابجایی بر حسب زمان، A - دامنه، ω - فرکانس زاویهای، φ - فاز
چندین پارامتر اساسی برای توصیف و ارزیابی کمی ارتعاش استفاده میشوند که هر کدام اطلاعات تشخیصی مهمی را در خود جای دادهاند. درک این پارامترها و روابط متقابل آنها، اساس تجزیه و تحلیل صحیح وضعیت تجهیزات است.
دامنه ارتعاش: شاخص شدت مشکل
دامنه، بزرگی ارتعاش را نشان میدهد، یعنی اینکه یک قطعه چقدر نسبت به موقعیت تعادل خود حرکت میکند. این پارامتر را میتوان با واحدهای مختلفی اندازهگیری کرد که هر کدام برای انواع خاصی از تحلیل و تشخیص مناسب هستند.
جابجایی (که معمولاً بر حسب میلیمتر یا میکرومتر اندازهگیری میشود) حداکثر انحراف از موقعیت تعادل را نشان میدهد. این پارامتر به ویژه برای ارتعاشات با فرکانس پایین و هنگام تحلیل نوسانات فونداسیون اهمیت دارد. مقادیر جابجایی بزرگ ممکن است نشاندهنده مشکلاتی در سختی سیستم یا پدیده رزونانس باشد.
سرعت ارتعاش (که بر حسب میلیمتر بر ثانیه یا اینچ بر ثانیه اندازهگیری میشود) جهانیترین پارامتر برای تشخیص اکثر مشکلات مکانیکی در محدوده فرکانسی 10 هرتز تا 1000 هرتز است. استانداردهای بینالمللی مانند ISO 20816 دقیقاً بر اساس اندازهگیریهای سرعت ارتعاش بنا شدهاند. این پارامتر همبستگی خوبی با انرژی ارتعاش و در نتیجه، با آسیب بالقوه به تجهیزات دارد.
پارامتر | واحدها | کاربرد | محدوده فرکانس |
---|---|---|---|
جابجایی | میلیمتر، میکرومتر | نوسانات فرکانس پایین، عدم تعادل | ۲-۲۰۰ هرتز |
سرعت | میلیمتر بر ثانیه | تشخیص عمومی، استانداردهای ISO | ۱۰-۱۰۰۰ هرتز |
شتاب | متر بر ثانیه مربع، گرم | عیوب فرکانس بالا، یاتاقانها | ۱۰۰۰-۲۰۰۰۰+ هرتز |
شتاب ارتعاش (که بر حسب متر بر ثانیه یا گرم اندازهگیری میشود، که در آن g = 9.81 متر بر ثانیه) بیشترین حساسیت را به اجزای ارتعاش فرکانس بالا دارد و برای تشخیص عیوب یاتاقان، گیربکسهای دندهای و سایر منابع ارتعاش فرکانس بالا استفاده میشود. شتاب متناسب با نیروی وارد بر سازه است، و این امر آن را برای ارزیابی بارهای سازهای مهم میکند.
دامنه بزرگ معمولاً نشان دهنده یک مشکل جدیتر است، با این حال، درک این نکته مهم است که مقادیر دامنه مطلق باید در چارچوب نوع تجهیزات، شرایط عملیاتی و ویژگیهای سیستم اندازهگیری تفسیر شوند. به عنوان مثال، دامنه ارتعاش 5 میلیمتر بر ثانیه ممکن است برای یک موتور بزرگ با سرعت پایین طبیعی باشد، اما برای یک اسپیندل ماشین CNC با سرعت بالا حیاتی است.
فرکانس ارتعاش: کلید شناسایی منبع
فرکانس به نرخ وقوع ارتعاش اشاره دارد و معمولاً بر حسب هرتز (Hz) بیان میشود که معادل تعداد سیکل در ثانیه یا سیکل در دقیقه (CPM) است که به ویژه هنگام تحلیل تجهیزات دوار مناسب است زیرا مستقیماً با دور در دقیقه (RPM) مرتبط است.
۱۰ هرتز - ۱۰ کیلوهرتز
تحلیل فرکانس یکی از قدرتمندترین ابزارهای تشخیصی است زیرا انواع مختلف عیوب در فرکانسهای مشخصه ظاهر میشوند. به عنوان مثال، عدم تعادل روتور در فرکانس چرخش (1X RPM) ظاهر میشود، عدم همترازی شفت باعث ایجاد ارتعاش در فرکانس چرخش مضاعف (2X RPM) میشود و عیوب یاتاقان بسته به هندسه یاتاقان و سرعت چرخش، ارتعاش را در فرکانسهای خاصی ایجاد میکنند.
رابطه ریاضی بین دور در دقیقه و فرکانس بر حسب هرتز با یک فرمول ساده بیان میشود: f(Hz) = RPM/60. این رابطه امکان تبدیل آسان سرعت چرخش به فرکانس هارمونیک اساسی و تجزیه و تحلیل فرکانسهای چندگانه (هارمونیکها) را فراهم میکند، که اغلب حاوی اطلاعات تشخیصی مهمی هستند.
تحلیل هارمونیک در تشخیص
ظهور هارمونیکهای قابل توجه (۲X، ۳X، ۴X فرکانس چرخش) اغلب نشاندهنده فرآیندهای غیرخطی در تجهیزات، مانند لقی، ضربه یا ضربانهای آیرودینامیکی است. تجزیه و تحلیل ترکیب هارمونیک امکان تشخیص مشکلاتی را فراهم میکند که ممکن است هنگام تجزیه و تحلیل فقط فرکانس اساسی آشکار نباشند.
فاز ارتعاش: اطلاعات مکانی در مورد حرکت
فاز، حرکت ارتعاشی یک قسمت از ماشین نسبت به قسمت دیگر یا نسبت به یک نقطه مرجع ثابت را توصیف میکند. این پارامتر به ویژه هنگام تشخیص انواع خاصی از عدم تعادل، ناهمترازی و سایر عیوبی که در روابط فاز مشخصه بین نقاط اندازهگیری مختلف آشکار میشوند، اهمیت دارد.
تحلیل فاز مستلزم اندازهگیری همزمان ارتعاش در چندین نقطه با استفاده از یک سیگنال مرجع، معمولاً از یک تاکومتر یا استروب، است. اختلاف فاز بین نقاط اندازهگیری مختلف میتواند نوع و محل مشکل را نشان دهد. به عنوان مثال، عدم تعادل معمولاً با حرکت هم فاز تکیهگاههای یاتاقان مشخص میشود، در حالی که عدم همترازی به صورت حرکت غیر هم فاز خود را نشان میدهد.
حرکت هم فاز
مشخصه عدم تعادل جرم، زمانی که همه نقاط به طور همزمان در یک جهت حرکت میکنند
حرکت ناهمفاز
معمولاً برای ناهمترازی شفت، زمانی که نقاط در جهت مخالف حرکت میکنند
حرکت تربیعی
ممکن است نشاندهنده حرکت بیضوی روتور یا ترکیبی از نقصها باشد
اهمیت ویژگیهای فرکانسی در تشخیص
لازم به ذکر است که مشکلات مکانیکی مختلف، به ویژه در فرکانسهای خاص، با ویژگیهای ارتعاشی متمایزی بروز میکنند. این الگو، اساس توسعه سیستمهای تشخیص تخصصی و الگوریتمهای تشخیص خودکار نقص است.
زیرهارمونیکها (فرکانسهای پایینتر از فرکانس چرخش اساسی، مانند 0.5X، 0.33X) ممکن است نشاندهنده ناپایداری چرخش، مشکلات یاتاقان غلتشی یا مشکلات گوه روغن در یاتاقانهای کشویی باشند. ظهور زیرهارمونیکها اغلب نشانهای از بروز مشکلات جدی است.
درک این مفاهیم اساسی ضروری است، به خصوص برای خوانندگانی که متخصص ارتعاش نیستند اما باید ماهیت مشکل را درک کنند تا در مورد نگهداری و تعمیر تصمیمات آگاهانه بگیرند. این دانش، پایه و اساس بحثهای بعدی در مورد روشهای تحلیل پیچیدهتر مانند تحلیل طیفی، تحلیل پوششی و تحلیل کپسترال را بنا مینهد.
مرحله ۱: اندازهگیری پارامترهای پایه
تعیین دامنه، فرکانس و فاز ارتعاش در نقاط کلیدی تجهیزات
مرحله ۲: تحلیل طیفی
تجزیه سیگنال پیچیده به مؤلفههای فرکانسی برای آشکارسازی امضاهای نقص مشخصه
مرحله ۳: تحلیل روند
ردیابی تغییرات پارامتر در طول زمان برای پیشبینی توسعه نقص
مرحله ۴: تشخیص یکپارچه
تجزیه و تحلیل جامع تمام دادههای موجود برای تعیین دقیق نوع و شدت مشکل
سیستمهای مدرن تحلیل ارتعاش قادر به پردازش حجم عظیمی از دادهها در زمان واقعی هستند و حتی نشانههای ضعیفی از ایجاد نقص را تشخیص میدهند. یادگیری ماشین و هوش مصنوعی به طور فزایندهای برای تشخیص خودکار الگو در سیگنالهای ارتعاشی به کار میروند و به طور قابل توجهی دقت و سرعت تشخیص را بهبود میبخشند.
۱.۳ مقصران رایج: شناسایی علل ریشهای لرزش بیش از حد
لرزش بیش از حد در تجهیزات صنعتی به ندرت یک مشکل مجزا است. به عنوان یک قاعده، این نشانه ای از یک یا چند وضعیت معیوب است که می توانند به طور مستقل یا در تعامل با یکدیگر ایجاد شوند. درک این علل ریشه ای برای تشخیص موثر و جلوگیری از خرابی های جدی تجهیزات بسیار مهم است.
عدم تعادل: شایعترین علت لرزش
عدم تعادل به دلیل توزیع ناهموار جرم در اجزای چرخان رخ میدهد و یک "نقطه سنگین" ایجاد میکند که باعث ایجاد نیروهای گریز از مرکز و در نتیجه لرزش میشود. این یکی از شایعترین دلایل لرزش در موتورها، روتورها، فنها، پمپها و سایر تجهیزات چرخان است.
عدم تعادل استاتیک
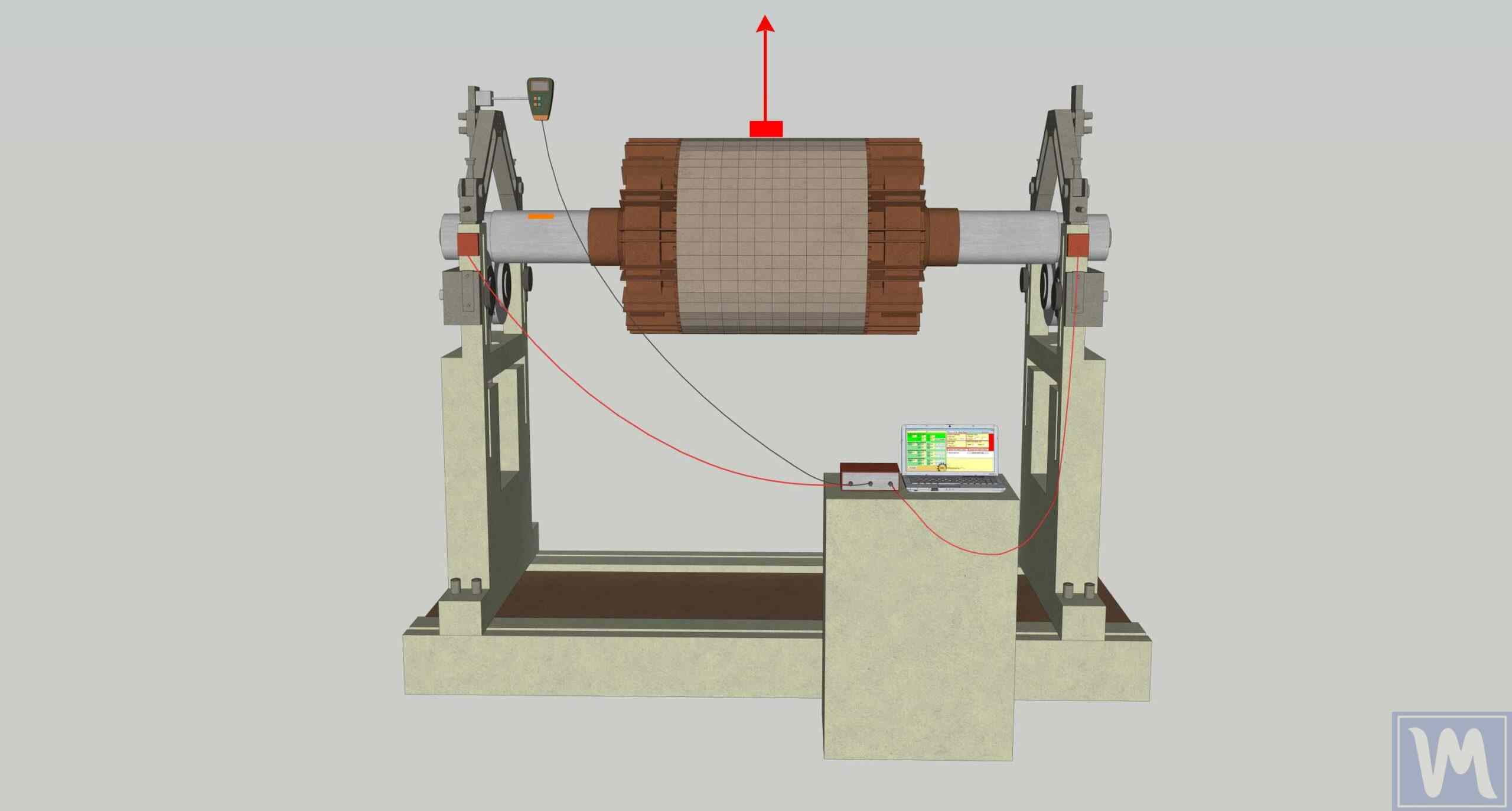
مرکز ثقل با محور چرخش منطبق نیست. در یک صفحه ظاهر میشود و باعث ارتعاش شعاعی در فرکانس چرخش میشود.
عدم تعادل دینامیکی
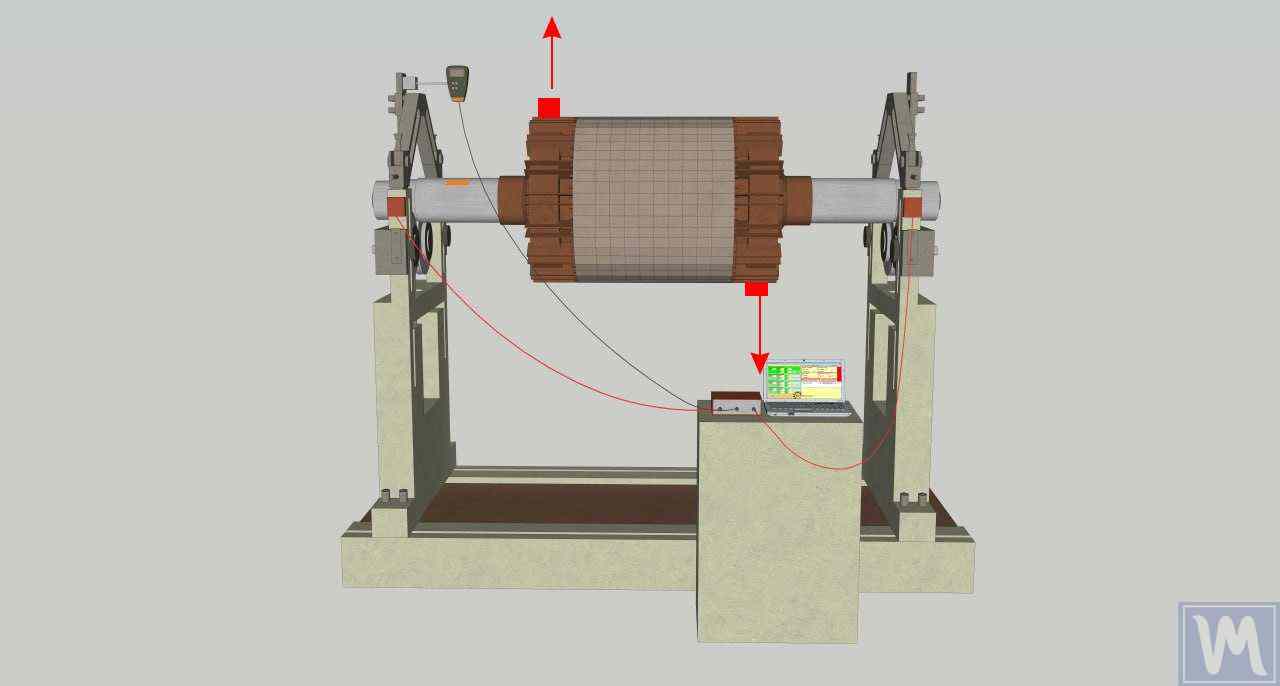
محور اینرسی با محور چرخش منطبق نیست. نیاز به اصلاح در دو صفحه دارد و گشتاورهایی ایجاد میکند که باعث گهواره شدن روتور میشود.
از نظر ریاضی، نیروی گریز از مرکز ناشی از عدم تعادل با فرمول زیر بیان میشود:
که در آن: m جرم نامتعادل، r شعاع نامتعادل، ω سرعت زاویهای
از این فرمول، مشخص است که نیروی عدم تعادل با مجذور سرعت چرخش متناسب است، که توضیح میدهد چرا مشکلات عدم تعادل به ویژه در سرعتهای بالا بحرانی میشوند. دو برابر شدن سرعت چرخش منجر به افزایش چهار برابری نیروی عدم تعادل میشود.
علل عدم تعادل متنوع هستند و شامل خطاهای تولید، سایش ناهموار، تجمع آلودگی، از بین رفتن وزنههای تعادل، تغییر شکل ناشی از اثرات دما و خوردگی میشوند. در طول عملیات، عدم تعادل میتواند به تدریج افزایش یابد و نیاز به تنظیم مجدد تجهیزات به صورت دورهای باشد.
ماهیت پیشرونده عدم تعادل
عدم تعادل معمولاً خود را تقویت میکند: عدم تعادل اولیه باعث افزایش بار روی یاتاقانها میشود که منجر به سایش سریع و افزایش لقی آنها میشود، که به نوبه خود عدم تعادل را تشدید کرده و یک چرخه معیوب از تخریب ایجاد میکند.
ناهمترازی: تهدید پنهان برای قابلیت اطمینان
ناهمترازی زمانی رخ میدهد که محورهای ماشینهای متصل (مثلاً موتور و پمپ) به طور نادرست همتراز باشند. دو نوع اصلی ناهمترازی وجود دارد: موازی (جابجایی محور) و زاویهای (تقاطع محورها با زاویه). در عمل، ناهمترازی ترکیبی، شامل هر دو نوع، رایجترین نوع است.
ناهمراستایی بارهای چرخهای روی کوپلینگها، یاتاقانها و شفتها ایجاد میکند که به صورت ارتعاش، عمدتاً در فرکانس چرخش دوگانه (2X RPM) ظاهر میشود. با این حال، بسته به نوع و درجه ناهمراستایی و همچنین ویژگیهای کوپلینگ، ممکن است هارمونیکهای دیگری نیز وجود داشته باشند.
نوع ناهمراستایی | فرکانسهای اصلی | جهت ارتعاش | علائم مشخصه |
---|---|---|---|
موازی | دو برابر دور در دقیقه | شعاعی | ارتعاش زیاد در جهت شعاعی |
زاویه دار | ۱X، ۲X دور در دقیقه | محوری | ارتعاش محوری قابل توجه |
ترکیبی | ۱X، ۲X، ۳X دور در دقیقه | شعاعی + محوری | طیف پیچیده با هارمونیکهای چندگانه |
محدودیتهای قابل قبول عدم همترازی به سرعت چرخش و نوع تجهیزات بستگی دارد. برای تجهیزات دقیق با سرعت بالا، انحرافات قابل قبول ممکن است تنها چند صدم میلیمتر باشد، در حالی که برای ماشینهای با سرعت پایین، تلرانسها ممکن است سخاوتمندانهتر باشند. با این حال، در هر صورت، همترازی دقیق برای عملکرد قابل اعتماد و عمر طولانی تجهیزات بسیار مهم است.
شل بودن مکانیکی: منبع بیثباتی
شل بودن مکانیکی به معنای فاصله بیش از حد بین اجزا است و میتواند به اشکال مختلف ظاهر شود: شل بودن پیچهای پایه یا نصب، یاتاقانهای فرسوده با فاصله داخلی بیش از حد، اتصال ضعیف قطعات روی شفت، ساییدگی اتصالات کلید، تغییر شکل قطعات محفظه.
شل بودن میتواند سایر منابع ارتعاش را تقویت کند و به عنوان تقویتکنندهای برای نیروهای عدم تعادل یا ناهمترازی عمل کند. علاوه بر این، شل بودن میتواند اثرات غیرخطی مانند ضربهها و کوبشها ایجاد کند که ارتعاش پهن باند و مؤلفههای فرکانس بالا را ایجاد میکنند.
علائم تشخیصی شل بودن
شل بودن اغلب از طریق ناپایداری قرائتهای ارتعاش، ظهور زیرهارمونیکها و طیف پیچیده با چندین پیک آشکار میشود. یک نشانه مشخص نیز وابستگی سطح ارتعاش به بار تجهیزات است.
عیوب یاتاقان: شاخصهای مشکل فرکانس بالا
سایش، حفرهدار شدن یا آسیب دیدن شیارها یا اجزای غلتشی یاتاقانها از دلایل اصلی ارتعاش فرکانس بالا است. یاتاقانها فرکانسهای مشخصه مربوط به هندسه و سینماتیک خود را تولید میکنند:
BPFI = (n/2) × (1 + d/D × cos α) × RPM/60
BSF = (D/2d) × (1 - (d/D × cos α)²) × RPM/60
FTF = (1/2) × (1 - d/D × cos α) × RPM/60
که در آن: n تعداد المانهای غلتشی، d قطر المان غلتشی، D قطر گام، α زاویه تماس
این فرمولها امکان محاسبه فرکانسهای مشخصه عیب یاتاقان را فراهم میکنند: BPFO (فرکانس عبور ساچمه در حلقه بیرونی)، BPFI (فرکانس عبور ساچمه در حلقه داخلی)، BSF (فرکانس چرخش ساچمه) و FTF (فرکانس اساسی قطار).
رزونانس: تقویتکنندهی تمام مشکلات
رزونانس زمانی رخ میدهد که فرکانس تحریک (مثلاً سرعت چرخش یا مضربهای آن) با فرکانس طبیعی ماشین یا سازه آن همزمان شود. این امر منجر به تقویت شدید ارتعاش میشود که میتواند عواقب فاجعهباری داشته باشد.
پدیده رزونانس
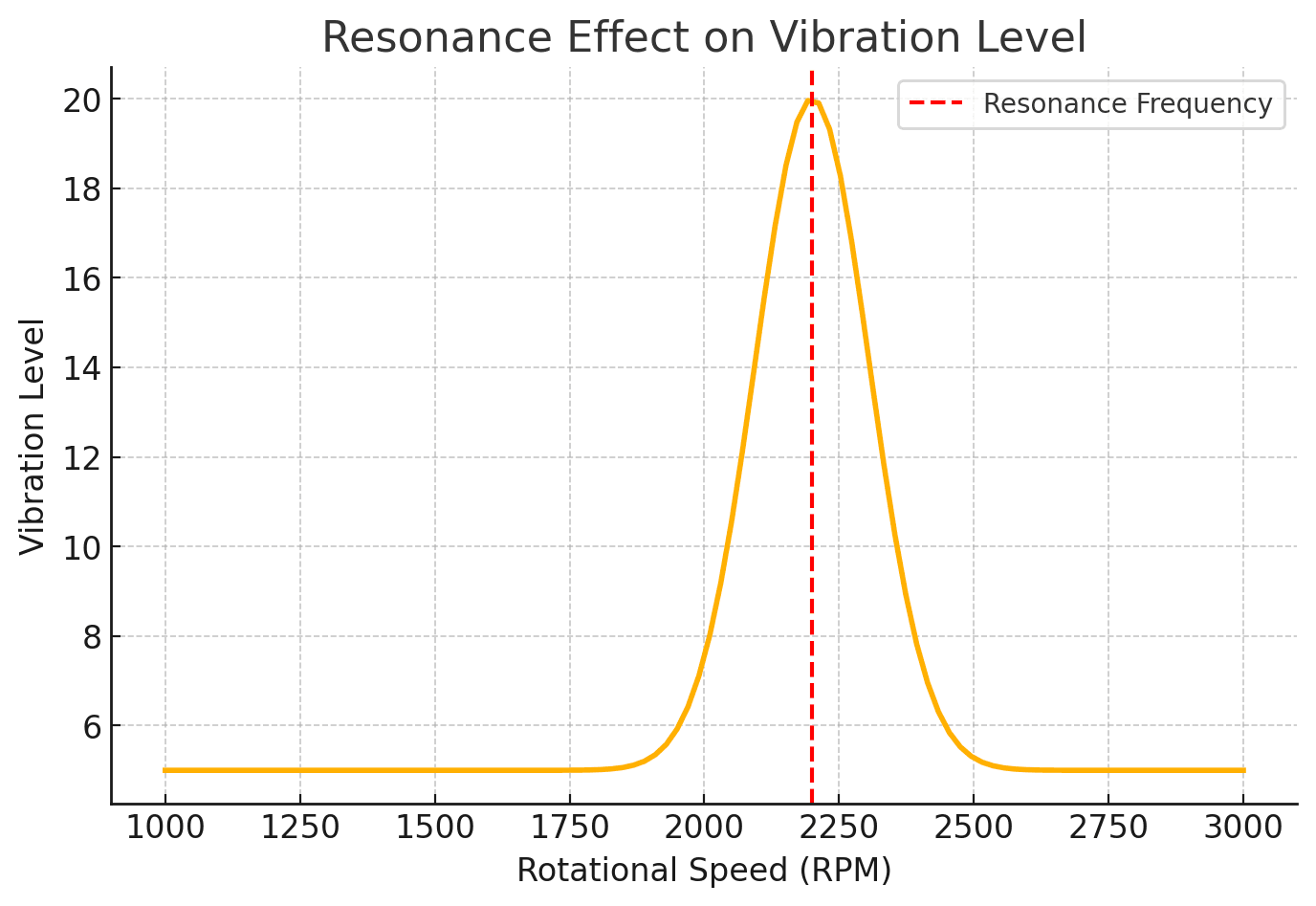
تشدید، ارتعاش را هنگامی که فرکانس تحریک با فرکانس طبیعی مطابقت دارد، تقویت میکند
پدیدههای رزونانس به ویژه در هنگام راهاندازی و خاموش شدن تجهیزات، زمانی که فرکانس چرخش از مقادیر بحرانی عبور میکند، خطرناک هستند. سیستمهای کنترل مدرن اغلب شامل الگوریتمهایی برای عبور سریع از مناطق رزونانس هستند تا زمان قرار گرفتن در معرض ارتعاش تقویتشده را به حداقل برسانند.
علل دیگر لرزش
علاوه بر دلایل اصلی، عوامل بسیار دیگری نیز وجود دارند که میتوانند باعث لرزش بیش از حد شوند:
شفتهای خمیده ایجاد ارتعاش در فرکانس چرخش و هارمونیکهای آن، که ویژگی ارتعاشی آن به درجه و نوع خمیدگی بستگی دارد. خمیدگیهای حرارتی میتوانند به دلیل گرم یا سرد شدن ناهموار شفتها رخ دهند.
مشکلات گیربکس شامل سایش دندانه، دندانههای شکسته یا لبپریده، عدم دقت در ساخت، و لقیهای نادرست میشود. گیربکسهای دندهای ارتعاشی در فرکانس مش (تعداد دندانهها × دور در دقیقه) و هارمونیکهای آن ایجاد میکنند.
مشکلات الکتریکی در موتورها ممکن است شامل شکافهای هوایی ناهموار، شکستگی میلههای روتور، مشکلات کموتاسیون در موتورهای DC، عدم تعادل فاز در موتورهای سه فاز باشد. این مشکلات اغلب در فرکانسهای مربوط به فرکانس شبکه برق ظاهر میشوند.
رویکرد جامع به تشخیص
درک این نکته مهم است که در شرایط عملیاتی واقعی، اغلب چندین منبع ارتعاش به طور همزمان وجود دارند. تشخیص مؤثر نیاز به تجزیه و تحلیل جامع از همه علل احتمالی و تعامل آنها دارد.
سیستمهای تشخیصی مدرن از پایگاههای داده امضای نقص و سیستمهای خبره برای تشخیص خودکار ترکیبات مختلف مشکل استفاده میکنند. این امر نه تنها امکان تشخیص وجود نقص، بلکه ارزیابی شدت، سرعت توسعه و اولویت حذف آن را نیز فراهم میکند.
۱.۴ اثر دومینو: پیامدهای ارتعاش کنترل نشده بر کارایی، عمر مفید و ایمنی
نادیده گرفتن ارتعاش بیش از حد، فرآیند تخریب آبشاری را آغاز میکند که میتوان آن را با اثر دومینو مقایسه کرد - افتادن یک کاشی ناگزیر منجر به افتادن بقیه کاشیها میشود. در زمینه تجهیزات صنعتی، این بدان معناست که یک مشکل اولیه کوچک، در صورت عدم رسیدگی، میتواند منجر به عواقب فاجعهباری برای کل سیستم تولید شود.
فرسایش شتابیافته قطعات: اولین حلقه در زنجیره تخریب
سایش تسریعشدهی قطعات یکی از مستقیمترین و واضحترین پیامدهای ارتعاش بیش از حد است. این فرآیند تقریباً بر تمام عناصر ماشین تأثیر میگذارد، اما آسیبپذیرترین آنها یاتاقانها، آببندها، شفتها، کوپلینگها و حتی فونداسیون ماشین هستند.
یاتاقانها به طور ویژه به ارتعاش حساس هستند زیرا بارهای دینامیکی اضافی ایجاد میکنند که شکست خستگی فلز را تسریع میکنند. تحقیقات نشان میدهد که افزایش سطح ارتعاش تنها به میزان 20% میتواند عمر مفید یاتاقان را به میزان 40-50% کاهش دهد. این امر به این دلیل رخ میدهد که دوام خستگی یاتاقانها طبق معادله لوندبرگ-پالمگرن با مکعب بار اعمال شده نسبت معکوس دارد.
آببندها همچنین از ارتعاش آسیب میبینند زیرا ارتعاش، پایداری تماس بین سطوح آببندی را مختل میکند. این امر منجر به نشت روانکننده، ورود آلودگی و بدتر شدن بیشتر شرایط عملیاتی یاتاقان میشود. آمار نشان میدهد که در صورت وجود ارتعاش قابل توجه، عمر مفید آببند میتواند 3 تا 5 برابر کاهش یابد.
شفتها در معرض تنشهای چرخهای ناشی از ارتعاش قرار دارند که میتواند منجر به ترکهای خستگی، به ویژه در نواحی تمرکز تنش مانند نواحی نشیمنگاه یاتاقان، شیارهای کلید یا تغییر قطرها، شود. ایجاد ترکهای خستگی در شفتها به ویژه خطرناک است زیرا میتواند منجر به شکست ناگهانی و فاجعهبار شود.
ماهیت مترقی سایش
سایش قطعات در اثر ارتعاش، روندی تصاعدی دارد: با افزایش لقی در یاتاقانها، دامنه ارتعاش افزایش مییابد که این امر سایش را بیشتر تسریع میکند. این فرآیند میتواند به صورت تصاعدی، به ویژه پس از عبور از یک سطح آستانه مشخص، توسعه یابد.
از دست دادن راندمان عملیاتی: تلفات انرژی پنهان
لرزش به ناچار منجر به از دست رفتن راندمان عملیاتی میشود زیرا انرژی به جای انجام کار مفید، به صورت نوسانات مکانیکی تلف میشود. این امر منجر به افزایش مصرف انرژی میشود که بسته به شدت مشکل و نوع تجهیزات میتواند از 5% تا 25% باشد.
مصرف انرژی اضافی از چندین منبع ناشی میشود:
- تلفات اصطکاکی: افزایش ارتعاش، اصطکاک را در یاتاقانها و سایر سطوح تماس افزایش میدهد.
- تلفات آیرودینامیکی: نوسانات پرههای فن و روتور، راندمان آنها را کاهش میدهد.
- تلفات درایو: ناهمراستایی و سایر عیوب باعث افزایش تلفات در کوپلینگها و گیربکسها میشود.
- تلفات تغییر شکل: انرژی صرف تغییر شکلهای الاستیک سازهها میشود
در فرآیندهای تولیدی که نیاز به دقت بالا دارند، ارتعاش میتواند کیفیت محصول نهایی را به خطر بیندازد. این امر به ویژه در صنایعی مانند تولید نیمههادیها، ماشینکاری دقیق و صنایع داروسازی بسیار مهم است، جایی که حتی کمترین ارتعاشات نیز میتواند منجر به نقص محصول شود.
پیامدهای اقتصادی: هزینههای پنهان و آشکار
هزینههای نگهداری به دلیل تعمیرات مکرر و از همه مهمتر، به دلیل خرابیهای برنامهریزی نشده افزایش مییابد. دادههای آماری از شرکتهای صنعتی، ساختار هزینه زیر را در رابطه با مشکلات ارتعاش نشان میدهد:
نوع هزینه | سهم از کل خسارات | هزینه متوسط | امکان پیشگیری |
---|---|---|---|
خرابیهای برنامهریزی نشده | 60-70% | $50،000-500،000 در ساعت | 90-95% |
تعمیر اضطراری | 15-20% | ۳ تا ۵ برابر هزینه برنامهریزیشده | 80-90% |
افت کیفیت محصول | 10-15% | وابسته به صنعت | 95-99% |
افزایش مصرف انرژی | 5-10% | ۵-۲۵۱TP3T بودجه انرژی | 85-95% |
به ویژه توقفهای برنامهریزی نشده دردناک هستند، که هزینه آنها میتواند برای خطوط تولید بزرگ به صدها هزار دلار در ساعت برسد. به عنوان مثال، در صنعت پتروشیمی، توقف یک واحد کراکینگ میتواند روزانه $500,000-1,000,000 دلار هزینه داشته باشد، بدون احتساب ضررهای ناشی از نقض تعهدات قراردادی.
خطرات ایمنی: تهدید برای پرسنل و محیط زیست
خطرات جدی ایمنی شغلی وجود دارد زیرا ارتعاش کنترل نشده میتواند منجر به خرابیهای ساختاری یا فاجعهبار تجهیزات با پتانسیل آسیب به پرسنل شود. تاریخ صنعتی موارد بسیاری را به خود دیده است که نادیده گرفتن مشکلات ارتعاش منجر به عواقب غمانگیزی شده است.
نمونههایی از شکستهای فاجعهبار
خرابی توربوژنراتور در نیروگاه برق آبی سایانو-شوشنسکایا در سال ۲۰۰۹ تا حدودی به مشکلات ارتعاشی مربوط بود. این حادثه منجر به ۷۵ کشته و میلیاردها روبل خسارت شد. چنین مواردی بر اهمیت حیاتی نظارت بر ارتعاش برای ایمنی تأکید میکند.
خطرات اصلی ایمنی شامل موارد زیر است:
- آسیبهای مکانیکی: از قطعات پرتاب شده تجهیزات تخریب شده
- آتشسوزی و انفجار: از نشت مایعات یا گازهای قابل احتراق به دلیل خرابی آببندی
- مسمومیت شیمیایی: وقتی سیستمهای حاوی مواد سمی دچار افت فشار میشوند
- فروریختگی سازهها: وقتی فونداسیونها یا سازههای نگهدارنده دچار شکست میشوند
سر و صدای بیش از حد ایجاد شده توسط ارتعاشات نیز نگرانیهای جدی ایجاد میکند. این امر بر راحتی اپراتور تأثیر میگذارد، تمرکز را کاهش میدهد و میتواند منجر به بیماریهای شنوایی شغلی شود. قرار گرفتن طولانی مدت در معرض سر و صدای بالای ۸۵ دسیبل میتواند باعث از دست دادن شنوایی برگشتناپذیر شود و خطرات قانونی برای کارفرمایان ایجاد کند.
پیامدهای زیستمحیطی: تأثیر پنهان بر محیط زیست
ناکارآمدی انرژی ناشی از ارتعاش، از طریق افزایش انتشار CO₂ و سایر گازهای گلخانهای، به تأثیر منفی بر محیط زیست منجر میشود. با توجه به مصرف انرژی سالانه شرکتهای بزرگ صنعتی که به صدها گیگاوات ساعت میرسد، حتی ناکارآمدی 5% نیز میتواند به معنای انتشار هزاران تن CO₂ اضافی باشد.
علاوه بر این، مشکلات ارتعاش میتواند منجر به موارد زیر شود:
- نشت سیالات فرآیندی به محیط زیست
- افزایش تولید زباله ناشی از فرسایش سریع
- آلودگی صوتی مناطق اطراف
- اختلال در پایداری فرآیند فناوری با پیامدهای زیستمحیطی
هزینه عدم اقدام
تحلیل موارد واقعی نشان میدهد که هزینه نادیده گرفتن مشکلات ارتعاش میتواند 10 تا 100 برابر بیشتر از هزینه حذف آنها باشد. علاوه بر این، میتوان از طریق نظارت منظم و مداخله به موقع از اکثر مشکلات جلوگیری کرد.
تأثیر جامع بر فرآیندهای تجاری
شرح مفصل همه این پیامدهای منفی، نیاز به مدیریت پیشگیرانه ارتعاش را تقویت میکند و درک روشنی از «نیازی» که راهحلهای تشخیصی مدرن برای برآوردن آن طراحی شدهاند، ایجاد میکند. درک این نکته مهم است که پیامدهای مشکلات ارتعاش بسیار فراتر از جنبههای فنی است و بر تمام سطوح کسبوکار تأثیر میگذارد:
- سطح عملیاتی: کاهش بهرهوری، افزایش هزینههای نگهداری
- سطح تاکتیکی: اختلال در برنامههای تولید، مشکلات تأمین
- سطح استراتژیک: از دست دادن مزایای رقابتی، آسیب به اعتبار
واقعیتهای اقتصادی مدرن ایجاب میکند که شرکتها به حداکثر بهرهوری و به حداقل رساندن خطرات دست یابند. در این زمینه، مدیریت پیشگیرانه ارتعاش نه تنها یک ضرورت فنی، بلکه یک مزیت استراتژیک است که میتواند موفقیت یا شکست را در رقابت تعیین کند.
۱.۵ مسیرهای تشخیصی: مروری بر ابزارها و روشهای تحلیل ارتعاش
فرآیند تشخیص ارتعاش، یک روش جامع را نشان میدهد که فناوریهای پیشرفته اندازهگیری، الگوریتمهای پیچیده تحلیل و دانش تخصصی را برای تبدیل دادههای ارتعاشی «خام» به اطلاعات تشخیصی ارزشمند ترکیب میکند. این فرآیند معمولاً شامل سه مرحله اصلی است: اندازهگیری، تحلیل و تفسیر، که هر یک از آنها برای دستیابی به نتایج دقیق و مفید بسیار مهم هستند.
اندازهگیری
تحلیل
تفسیر
مرحله اندازهگیری: حسگرها به عنوان پنجرهای به دنیای ارتعاش
حسگرها اولین حلقه بسیار مهم در زنجیره تشخیص ارتعاش هستند. عمدتاً از شتابسنجها استفاده میشود - دستگاههایی که روی تجهیزات نصب میشوند تا ارتعاشات مکانیکی را ثبت کرده و آنها را به سیگنالهای الکتریکی تبدیل کنند. کیفیت و ویژگیهای حسگرها مستقیماً بر دقت و قابلیت اطمینان کل فرآیند تشخیص تأثیر میگذارد.
شتابسنجهای مدرن به چندین نوع اصلی تقسیم میشوند:
پیزوالکتریک
رایجترین نوع. دارای محدوده فرکانسی وسیع (تا ۵۰ کیلوهرتز)، حساسیت و پایداری بالا. ایدهآل برای اکثر کاربردهای صنعتی.
IEPE (ICP)
سنسورهای پیزوالکتریک با قطعات الکترونیکی داخلی. سطح نویز کم و اتصال سادهای را فراهم میکنند. به برق از دستگاه اندازهگیری نیاز دارند.
سیستمهای میکرو الکترومکانیکی (MEMS)
حسگرهای میکروالکترومکانیکی. جمع و جور، ارزان، مقاوم در برابر ضربه. مناسب برای نظارت مداوم و سیستمهای بیسیم.
ویژگیهای حسگر بسیار مهم عبارتند از:
- حساسیت: معمولاً با واحد mV/g یا pC/g اندازهگیری میشود. حساسیت بالا امکان تشخیص سیگنالهای ضعیف را فراهم میکند اما ممکن است منجر به اضافه بار با ارتعاش قوی شود.
- محدوده فرکانس: طیف فرکانسهایی را که سنسور میتواند به طور دقیق اندازهگیری کند، تعیین میکند. برای تشخیص یاتاقان، ممکن است به محدودهای تا 20 تا 50 کیلوهرتز نیاز باشد.
- محدوده دینامیکی: نسبت بین حداکثر و حداقل سطح قابل اندازهگیری. محدوده دینامیکی وسیع امکان اندازهگیری ارتعاشات ضعیف و قوی را فراهم میکند.
- پایداری دما: برای کاربردهای صنعتی با محدوده دمای عملیاتی گسترده، مهم است.
جایگذاری حسگر: هنر و علم
قرارگیری صحیح سنسور برای به دست آوردن دادههای نماینده بسیار مهم است. سنسورها باید تا حد امکان نزدیک به یاتاقانها، در جهت حداکثر سختی سازه و با اتصال مکانیکی قابل اعتماد نصب شوند تا انتقال دقیق ارتعاش تضمین شود.
ارتعاشسنجها: ارزیابی سریع وضعیت عمومی
ارتعاشسنجها ابزارهای قابل حملی هستند که اندازهگیری سطح ارتعاش عمومی را فراهم میکنند و برای بررسی سریع وضعیت تجهیزات یا ردیابی روند کلی وضعیت ماشین در درازمدت مفید هستند. این ابزارها معمولاً یک یا چند پارامتر ارتعاش انتگرالی مانند سرعت RMS یا شتاب اوج را نمایش میدهند.
ویبرومترهای مدرن اغلب شامل توابع زیر هستند:
- اندازهگیری در چندین باند فرکانسی برای محلیسازی تقریبی مسئله
- ذخیرهسازی دادهها برای تحلیل روند
- مقایسه با استانداردهای از پیش تعیینشده (ISO 20816، ISO 10816)
- تجسم طیفی ساده
- انتقال داده بیسیم
پارامتر | کاربرد | مقادیر معمول هشدار | باند فرکانس |
---|---|---|---|
سرعت RMS | ارزیابی وضعیت عمومی | ۲.۸-۱۱.۲ میلیمتر بر ثانیه | ۱۰-۱۰۰۰ هرتز |
اوج شتاب | عیوب ناشی از ضربه | ۲۵-۱۰۰ گرم | ۱۰۰۰-۱۵۰۰۰ هرتز |
اوج جابجایی | مشکلات فرکانس پایین | ۲۵-۱۰۰ میکرومتر | ۲-۲۰۰ هرتز |
آنالایزرهای ارتعاش: تشخیص عمیق
برای تشخیص عمیقتر و شناسایی علت اصلی ارتعاش، از آنالیزورهای ارتعاش یا آنالیزورهای فرکانس استفاده میشود. این ابزارهای پیچیده، کامپیوترهای تخصصی هستند که برای پردازش سیگنال ارتعاش در زمان واقعی بهینه شدهاند.
اساس عملکرد آنالیزورهای مدرن، تبدیل سریع فوریه (FFT) است، یک الگوریتم ریاضی که یک سیگنال زمانی پیچیده را به اجزای فرکانسی منفرد آن تجزیه میکند. این فرآیند یک طیف ارتعاش ایجاد میکند - نموداری که دامنه ارتعاش را به عنوان تابعی از فرکانس نشان میدهد.
تبدیل فوریه، سیگنال زمانی x(t) را به طیف فرکانسی X(f) تبدیل میکند.
دستگاههای آنالیز ارتعاش مدرن عملکردهای پیشرفته بسیاری را ارائه میدهند:
- تحلیل چند کاناله: اندازهگیری همزمان ارتعاش در چندین نقطه برای تحلیل فاز
- تبدیل فوریه سریع با وضوح بالا: تا ۲۵۶۰۰ خط برای تحلیل طیفی دقیق
- تحلیل زمان: ثبت و تحلیل فرآیندهای گذرا
- تحلیل پوششی: استخراج سیگنالهای مدولاسیون برای تشخیص بیرینگ
- تحلیل سپسترال: تشخیص ساختارهای تناوبی در طیف
- تحلیل مداری: تجسم حرکت شفت در فضا
معیارهای انتخاب آنالایزر
هنگام انتخاب یک آنالایزر ارتعاش، نه تنها توجه به ویژگیهای فنی، بلکه سهولت استفاده، کیفیت نرمافزار، قابلیتهای تفسیر خودکار نتایج و ادغام با سیستمهای مدیریت سازمانی نیز مهم است.
تحلیل شکل موج زمانی: جستجوی فرآیندهای گذرا
تحلیل شکل موج زمانی یکی دیگر از روشهای ارزشمند است، بهویژه برای تشخیص ضربهها، گذراها و پدیدههای غیرایستا که ممکن است در طیف فرکانسی قابل مشاهده نباشند، مفید است. این روش امکان مشاهده سیگنال ارتعاش را به شکل «طبیعی» آن - به عنوان تابعی از زمان - فراهم میکند.
پارامترهای کلیدی تحلیل زمان عبارتند از:
- ضریب تاج: نسبت مقدار پیک به RMS. مقادیر بالا نشان دهنده وجود اثرات است.
- کشیدگی: معیار آماری توزیع "تیز بودن". افزایش کشیدگی اغلب نشانه اولیه ایجاد نقص در یاتاقان است.
- کجشکلی: معیار عدم تقارن توزیع دامنه.
ادغام روشهای مختلف تحلیل
مؤثرترین تشخیص با ترکیب روشهای مختلف تجزیه و تحلیل حاصل میشود. تجزیه و تحلیل زمانی میتواند وجود مشکل را آشکار کند، تجزیه و تحلیل طیفی میتواند نوع آن را شناسایی کند و تجزیه و تحلیل فاز میتواند منبع را به طور دقیق مکانیابی کند.
روندهای مدرن در تجهیزات تشخیصی
توسعه فناوری منجر به قابلیتهای جدیدی در تشخیص ارتعاش میشود:
- سیستمهای مانیتورینگ بیسیم: شبکههای حسگر با توان مستقل و انتقال داده بیسیم
- هوش مصنوعی: تشخیص خودکار الگوی نقص و پیشبینی شکست
- پلتفرمهای ابری: پردازش متمرکز دادهها از اشیاء متعدد با استفاده از منابع محاسباتی بزرگ
- اپلیکیشنهای موبایل: تبدیل گوشیهای هوشمند به دستگاههای اندازهگیری ارتعاش قابل حمل
- ادغام IIoT: شامل نظارت بر ارتعاش در سیستمهای اینترنت اشیاء صنعتی
پیادهسازی این ابزارها و روشها، به ویژه تحلیل FFT، زمینه را برای بحث در مورد مزایای داشتن قابلیتهای تحلیلی پیشرفته، به طور ایدهآل قابل حمل، برای تشخیص مؤثر در محل فراهم میکند. تحلیلگرهای قابل حمل مدرن، قدرت سیستمهای ثابت را با راحتی استفاده میدانی ترکیب میکنند و امکان تشخیص جامع را مستقیماً در تجهیزات فراهم میکنند.
اندازهگیری پایه
استفاده از ارتعاشسنجهای ساده برای ارزیابی سطح کلی ارتعاش و تعیین نیاز به تحلیل بیشتر
تحلیل طیفی
استفاده از آنالیزورهای FFT برای شناسایی مولفههای فرکانسی و تعیین نوع نقص
تشخیص عمیق
استفاده از روشهای تخصصی (آنالیز پوششی، کپستروم، مدارها) برای تشخیص دقیق عیوب پیچیده
نظارت یکپارچه
نظارت مداوم با تشخیص خودکار و پیشبینی مبتنی بر هوش مصنوعی
آیندهی تشخیص ارتعاشات در ایجاد سیستمهای هوشمندی نهفته است که نه تنها قادر به تشخیص و طبقهبندی عیوب باشند، بلکه بتوانند توسعهی آنها را پیشبینی کنند، برنامهریزی تعمیر و نگهداری را بهینه کنند و با سیستمهای مدیریت عمومی سازمان ادغام شوند تا بهرهوری عملیاتی را به حداکثر برسانند.
۱.۶ قدرت مدیریت پیشگیرانه ارتعاش: مزایای تشخیص و اصلاح زودهنگام
اتخاذ یک رویکرد پیشگیرانه در مدیریت ارتعاشات به جای رویکرد سنتی و واکنشی "تعمیر پس از خرابی" نشان دهنده یک تغییر اساسی در فلسفه نگهداری و تعمیرات است. این رویکرد نه تنها از خرابیهای فاجعهبار جلوگیری میکند، بلکه کل چرخه عمر تجهیزات را بهینه میکند و نگهداری و تعمیرات را از یک مرکز هزینه به منبعی برای مزایای رقابتی تبدیل میکند.
افزایش عمر مفید تجهیزات: ریاضیات دوام
مدیریت پیشگیرانه ارتعاش مزایای قابل توجه بسیاری را ارائه میدهد که از جمله آنها افزایش عمر مفید اجزای تجهیزات است. تحقیقات نشان میدهد که مدیریت صحیح ارتعاش میتواند عمر مفید یاتاقانها را 200-300%، آببندها را 150-200% و عمر مفید کلی دستگاه را 50-100% افزایش دهد.
این پیشرفتها بر اساس اصول اساسی شکست خستگی مواد بنا شدهاند. طبق معادله وهلر، دوام خستگی با دامنه تنش نسبت معکوس دارد و برای اکثر فلزات بین ۳ تا ۱۰ است. این بدان معناست که حتی کاهش اندک در سطح ارتعاش میتواند منجر به افزایش قابل توجه عمر مفید شود.
که در آن: N تعداد سیکلهای تا شکست، Δσ دامنه تنش، A و m ثابتهای ماده هستند.
بهبود اثربخشی کلی تجهیزات (OEE)
اثربخشی کلی تجهیزات (OEE) یک شاخص کلیدی بهرهوری تولید است که در دسترس بودن، عملکرد و کیفیت را در نظر میگیرد. مدیریت پیشگیرانه ارتعاش بر هر سه مؤلفه OEE تأثیر مثبت میگذارد:
- موجودی: کاهش زمان توقفات برنامهریزی نشده از طریق پیشگیری از خرابیهای اضطراری
- عملکرد: حفظ پارامترهای عملیاتی و سرعتهای بهینه
- کیفیت: کاهش عیوب از طریق پایداری فرآیندهای تکنولوژیکی
آمارها نشان میدهد که شرکتهایی که برنامههای جامع مدیریت ارتعاش را اجرا میکنند، به بهبود OEE 5-15% دست مییابند که برای یک شرکت تولیدی بزرگ میتواند به معنای سود اضافی میلیونها دلار در سال باشد.
محاسبه اثر اقتصادی از بهبود OEE
برای یک خط تولید به ارزش ۱TP4T10 میلیون با بهرهوری سالانه ۱TP4T50 میلیون، بهبود OEE به میزان ۱۰۱TP3T سود اضافی معادل ۱TP4T5 میلیون در سال به همراه دارد که سرمایهگذاری در سیستم نظارت بر ارتعاش را ظرف چند ماه بازمیگرداند.
پیشگیری از خرابیهای جدی و پرهزینه
یکی از مهمترین مزایای رویکرد پیشگیرانه، پیشگیری از خرابیهای جدی و پرهزینه است. خرابیهای آبشاری، زمانی که خرابی یک جزء منجر به آسیب به سایر بخشهای سیستم میشود، میتواند به ویژه از نظر مالی و عملیاتی مخرب باشد.
یک مثال کلاسیک، خرابی یاتاقان در توربوماشینهای پرسرعت است: تخریب یاتاقان میتواند منجر به تماس روتور-استاتور شود و باعث آسیب به پرهها، محفظه، شفتها شود و حتی ممکن است بر فونداسیون تأثیر بگذارد. هزینه چنین خرابی آبشاری میتواند 50 تا 100 برابر هزینه تعویض به موقع یاتاقان باشد.
نوع مداخله | هزینه | خرابی | احتمال موفقیت |
---|---|---|---|
نگهداری پیشگیرانه | $1,000 | ۲-۴ ساعت | 95-98% |
تعمیر برنامهریزیشده | $5,000 | ۸-۱۶ ساعت | 90-95% |
تعمیر اضطراری | $25,000 | ۲۴-۷۲ ساعت | 70-85% |
شکست آبشاری | $100,000+ | ۱-۴ هفته | 50-70% |
کاهش نویز و لرزش عملیاتی
کاهش قابل توجه نویز عملیاتی از مزایای دیگر مدیریت موثر ارتعاش است. نویز در محیط صنعتی نه تنها باعث ناراحتی پرسنل میشود، بلکه میتواند نشاندهنده مشکلات فنی نیز باشد، بر دقت کار اپراتور تأثیر بگذارد و خطرات قانونی مربوط به الزامات ایمنی شغلی را ایجاد کند.
کاهش 10 دسیبل در سطح صدا توسط گوش انسان به عنوان کاهش دو برابری بلندی صدا درک میشود. برای مراکز تولیدی که سطح صدا میتواند از 90 دسیبل فراتر رود، حتی کاهش اندک میتواند تأثیر قابل توجهی بر راحتی کار و بهرهوری پرسنل داشته باشد.
تحلیل ارتعاشات به عنوان پایه و اساس نگهداری و تعمیرات پیشبینانه
آنالیز ارتعاشات سنگ بنای نگهداری و تعمیرات پیشبینانه (PdM) است - راهبردی که با هدف پیشبینی خرابیها از طریق پایش مداوم یا دورهای وضعیت تجهیزات انجام میشود. PdM نشان دهنده تکامل از نگهداری و تعمیرات واکنشی و پیشگیرانه به رویکرد هوشمند و مبتنی بر داده است.
اصول کلیدی نگهداری و تعمیرات پیشگیرانه عبارتند از:
- پایش وضعیت: اندازهگیری مداوم یا منظم پارامترهای کلیدی
- تحلیل روند: پیگیری تغییرات در طول زمان برای شناسایی مشکلات در حال توسعه
- پیشبینی: استفاده از مدلهای آماری و یادگیری ماشین برای پیشبینی شکستها
- بهینهسازی: برنامهریزی مداخلات در زمان بهینه با در نظر گرفتن الزامات عملیاتی
مدل اقتصادی نگهداری و تعمیرات پیشبینانه
تحقیقات نشان میدهد که نگهداری و تعمیرات پیشبینانه میتواند هزینههای نگهداری را 25-30% کاهش دهد، زمان آماده به کار را 70-75% افزایش دهد و عمر مفید تجهیزات را 20-40% افزایش دهد.
تشخیص زودهنگام و برنامهریزی مداخله
اجرای برنامه آنالیز ارتعاشات امکان تشخیص مشکلات در مراحل اولیه آنها را فراهم میکند، زمانی که هنوز بر عملکرد تأثیری ندارند اما میتوان آنها را با استفاده از روشهای تشخیصی حساس شناسایی کرد. این امر خطر خاموشیهای غیرمنتظره را کاهش داده و برنامهریزی تعمیر و نگهداری را بهینه میکند.
منحنی PF (خرابی بالقوه-عملکردی) توسعه نقص را در طول زمان نشان میدهد:
نقطه P - شکست بالقوه
نقص با استفاده از روشهای تشخیصی قابل تشخیص میشود اما هنوز بر عملکرد تأثیری ندارد.
توسعه نقص
وخامت تدریجی وضعیت با امکان مداخله برنامهریزیشده
آستانه عملکردی
نقص شروع به تأثیر بر عملکرد تجهیزات میکند
نقطه F - خرابی عملکردی
تجهیزات نمیتوانند وظایف خود را انجام دهند، تعمیر اضطراری لازم است
فاصله زمانی بین شروع و پایان درمان (PF) برای انواع مختلف نقص میتواند از چند روز تا چند ماه متغیر باشد و زمان کافی برای برنامهریزی مداخله بهینه را فراهم کند.
مزایای اقتصادی مستقیم
این امر مستقیماً منجر به کاهش زمان از کارافتادگی و صرفهجویی قابل توجه در هزینهها میشود. تجزیه و تحلیل سود اقتصادی نشان میدهد که هر دلار سرمایهگذاری در سیستم نظارت بر ارتعاش، بسته به نوع تولید و حساسیت تجهیزات، از 3 تا 15 دلار صرفهجویی به همراه دارد.
الزامات فنی برای اجرای موفقیتآمیز
برای بهرهمندی کامل از این مزایا، انجام تشخیصهای به موقع، دقیق و اغلب در محل بسیار مهم است. توانایی انجام منظم و مؤثر این بررسیها، کلید موفقیت هر استراتژی نگهداری پیشگیرانه است.
الزامات مدرن برای تجهیزات تشخیصی عبارتند از:
- قابلیت حمل: امکان انجام اندازهگیریها به طور مستقیم در محل تجهیزات
- Accuracy: قابلیت تشخیص حتی نشانههای ضعیفِ بروز نقص
- سرعت تحلیل: پردازش سریع دادهها برای تصمیمگیری فوری
- سهولت استفاده: رابط کاربری بصری برای پرسنل با مدارک تحصیلی مختلف
- ادغام: سازگاری با سیستمهای مدیریتی موجود
عوامل حیاتی موفقیت
موفقیت برنامه مدیریت پیشگیرانه ارتعاش نه تنها به کیفیت تجهیزات، بلکه به عوامل سازمانی نیز بستگی دارد: آموزش پرسنل، ایجاد رویههای مناسب، ادغام با برنامهریزی تولید و پشتیبانی مدیریت.
ابزارهای پیشرفته قابل حمل امکان دستیابی سریع به اطلاعات مفید، تسهیل تصمیمگیری آگاهانه و مداخله زودهنگام را فراهم میکنند. این ابزارها قابلیتهای تحلیلی پیشرفته را با کاربرد عملی در میدان عمل ترکیب میکنند و تشخیص پیشرفته را برای طیف وسیعی از متخصصان فنی قابل دسترسی میسازند.
آینده مدیریت پیشگیرانه ارتعاشات در گرو ایجاد سیستمهای هوشمند و خودآموز است که نه تنها وضعیت فعلی تجهیزات را رصد میکنند، بلکه عملکرد آن را در زمان واقعی بهینه میکنند و با تغییر شرایط عملیاتی و الزامات تولید سازگار میشوند. این امر راه را برای سیستمهای تولیدی واقعاً خودکار که قادر به حفظ عملکرد بهینه خود به طور مستقل هستند، باز میکند.
نتیجهگیری: مسیری به سوی تولید قابل اعتماد و کارآمد
درک و مدیریت ارتعاش در تجهیزات صنعتی نه تنها یک ضرورت فنی، بلکه یک پایه استراتژیک برای دستیابی به برتری عملیاتی در دنیای رقابتی امروز است. تشخیص صحیح ارتعاش نه تنها بر قابلیت اطمینان فنی تجهیزات، بلکه بر بهرهوری اقتصادی، ایمنی پرسنل و مسئولیت زیستمحیطی شرکت نیز تأثیر میگذارد.
سرمایهگذاری در سیستمهای مدرن پایش و تحلیل ارتعاشات، از طریق جلوگیری از حوادث پرهزینه، بهینهسازی برنامهریزی تعمیر و نگهداری و افزایش اثربخشی کلی تجهیزات، چندین برابر بازگشت سرمایه دارد. آینده تولید صنعتی متعلق به شرکتهایی است که میتوانند دادههای مربوط به وضعیت تجهیزات خود را به مزایای رقابتی تبدیل کنند.
0 Comment