Dynamic balancing devices for shafts and machine equipment Balanset-1A priced at €1751.
O rotor é um corpo que gira em torno de um eixo e é mantido por suas superfícies de apoio nos suportes. As superfícies de apoio do rotor transmitem cargas para os suportes por meio de rolamentos ou mancais deslizantes. As superfícies de apoio são as superfícies dos munhões ou as superfícies que os substituem.
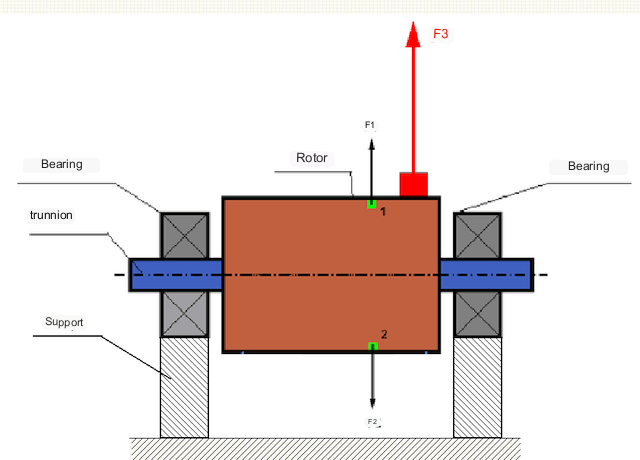
Fig.1 Rotor e forças centrífugas que atuam sobre ele.
Em um rotor perfeitamente balanceado, sua massa é distribuída simetricamente em torno do eixo de rotação, ou seja, qualquer elemento do rotor pode ser combinado com outro elemento localizado simetricamente em torno do eixo de rotação. Em um rotor balanceado, a força centrífuga que atua em qualquer elemento do rotor é equilibrada pela força centrífuga que atua no elemento simétrico. Por exemplo, as forças centrífugas F1 e F2, iguais em magnitude e opostas em direção, atuam nos elementos 1 e 2 (marcados em verde na figura 1). Isso é verdadeiro para todos os elementos simétricos do rotor e, portanto, a força centrífuga total que atua no rotor é 0 e o rotor está balanceado.
Mas se a simetria do rotor for quebrada (o elemento assimétrico está marcado em vermelho na fig. 1), a força centrífuga desequilibrada F3 atuará no rotor. A carga dinâmica resultante dessa força é transmitida aos rolamentos, resultando em desgaste acelerado.
Além disso, sob a influência dessa força variável na direção, há uma deformação cíclica dos suportes e da fundação, na qual o rotor está fixado, ou seja, há vibração. Para eliminar o desequilíbrio do rotor e a vibração que o acompanha, é necessário instalar massas de balanceamento para restaurar a simetria do rotor.
O balanceamento do rotor é uma operação para corrigir o desequilíbrio por meio da adição de massas de balanceamento.
A tarefa de balanceamento é encontrar o tamanho e a localização (ângulo) de uma ou mais massas de balanceamento.
Tipos de rotores e tipos de desequilíbrio.
Levando em conta a resistência do material do rotor e a magnitude das forças centrífugas que atuam sobre ele, os rotores podem ser divididos em dois tipos: rotores rígidos e rotores flexíveis.
Os rotores rígidos se deformam de forma insignificante sob a ação da força centrífuga nos modos de trabalho e a influência dessa deformação nos cálculos pode ser desprezada.
A deformação dos rotores flexíveis não pode mais ser negligenciada. A deformação de rotores flexíveis complica a solução do problema de balanceamento e exige a aplicação de outros modelos matemáticos em comparação com o problema de balanceamento de rotores rígidos. A seguir, consideraremos apenas o balanceamento de rotores rígidos.
Dependendo da distribuição das massas desbalanceadas ao longo do comprimento do rotor, é possível distinguir dois tipos de desbalanceamento: estático e dinâmico (momentâneo). Dessa forma, o balanceamento estático e dinâmico do rotor são mencionados. O desbalanceamento estático do rotor ocorre sem rotação do rotor, ou seja, na estática, quando o rotor é revertido pela gravidade com seu "ponto pesado" para baixo. Um exemplo de um rotor com desbalanceamento estático é mostrado na Fig. 2
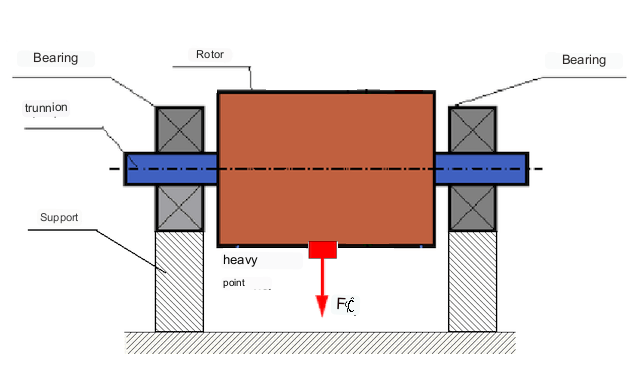
Fig.2 Desequilíbrio estático do rotor.
Sob a ação da gravidade, o "ponto pesado" gira para baixo
O desequilíbrio dinâmico ocorre somente quando o rotor está girando.
Um exemplo de um rotor com desequilíbrio dinâmico é mostrado na Fig. 3.
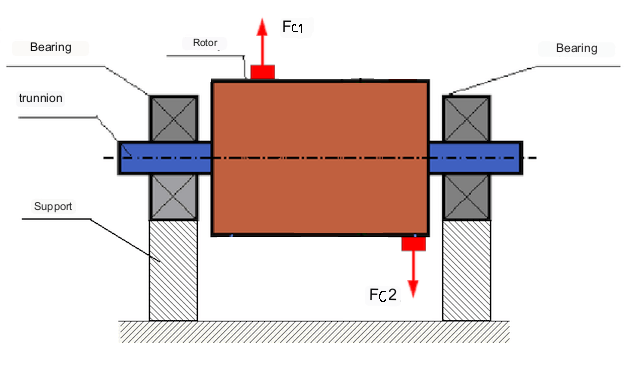
Fig.3 Desequilíbrio dinâmico do rotor.
As forças Fc1 e Fc2 criam um momento que tende a desequilibrar o rotor.
Nesse caso, as massas iguais e desequilibradas M1 e M2 estão em planos diferentes, em locais diferentes ao longo do comprimento do rotor. Na posição estática, ou seja, quando o rotor não gira, somente a gravidade atua sobre o rotor e as massas se equilibram. Na dinâmica, quando o rotor gira, as forças centrífugas Fc1 e Fc2 começam a agir sobre as massas M1 e M2. Essas forças são iguais em magnitude e opostas em direção. Entretanto, como são aplicadas em locais diferentes ao longo do comprimento do eixo e não estão na mesma linha, essas forças não se compensam. As forças Fc1 e Fc2 criam um torque aplicado ao rotor. Portanto, esse desequilíbrio também é chamado de desequilíbrio de momento. Consequentemente, forças centrífugas não compensadas atuam nas posições dos rolamentos, o que pode exceder em muito os valores calculados e reduzir a vida útil dos rolamentos.
Como esse tipo de desbalanceamento ocorre apenas dinamicamente durante a rotação do rotor, ele é chamado de desbalanceamento dinâmico. Ele não pode ser corrigido em condições estáticas por meio do balanceamento "em facas" ou métodos semelhantes. Para eliminar o desbalanceamento dinâmico, é necessário instalar dois pesos de compensação que produzam um momento igual em magnitude e oposto em direção ao momento resultante das massas M1 e M2. As massas de compensação não precisam ser definidas como opostas e iguais em magnitude às massas M1 e M2. O principal é que elas produzam um momento que compense totalmente o momento de desequilíbrio.
Em geral, as massas M1 e M2 podem não ser iguais entre si, portanto, haverá uma combinação de desequilíbrio estático e dinâmico. Está teoricamente comprovado que, para um rotor rígido, dois pesos espaçados ao longo do comprimento do rotor são necessários e suficientes para eliminar seu desequilíbrio. Esses pesos compensarão o torque resultante do desbalanceamento dinâmico e a força centrífuga resultante da assimetria da massa em relação ao eixo do rotor (desbalanceamento estático). Normalmente, o desbalanceamento dinâmico é característico de rotores longos, como eixos, e o desbalanceamento estático é característico de rotores estreitos. Entretanto, se o rotor estreito estiver inclinado em relação ao eixo ou deformado ("figura oito"), será difícil eliminar o desbalanceamento dinâmico. (veja a Fig. 4), pois, nesse caso, é difícil instalar pesos de correção que criem o momento de compensação necessário.
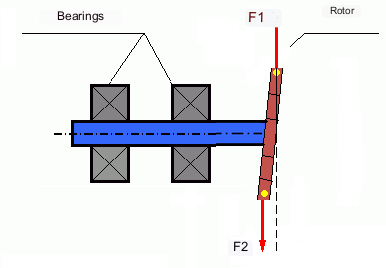
Fig.4 Desequilíbrio dinâmico do rotor estreito.
As forças F1 e F2 não se encontram na mesma linha e não se compensam mutuamente.
Devido ao fato de que o braço para criar torque é pequeno devido ao rotor estreito, podem ser necessários grandes pesos de correção. Entretanto, isso também resulta em um "desequilíbrio induzido" devido à deformação do rotor estreito por forças centrífugas dos pesos de correção. (Consulte, por exemplo, "Instruções metodológicas para balanceamento de rotores rígidos (de acordo com a ISO 22061-76)". Seção 10. SISTEMA DE SUPORTE DO ROTOR. )
Isso é perceptível em rotores estreitos de ventiladores, nos quais, além do desequilíbrio de força, o desequilíbrio aerodinâmico também está ativo. Deve-se entender que o desequilíbrio aerodinâmico, ou melhor, a força aerodinâmica é diretamente proporcional à velocidade angular do rotor e, para sua compensação, é usada a força centrífuga da massa de correção, que é proporcional ao quadrado da velocidade angular. Portanto, o efeito de equilíbrio só pode ocorrer em uma frequência de equilíbrio específica. Em outras frequências de rotação, há um erro adicional.
O mesmo pode ser dito das forças eletromagnéticas em um motor elétrico, que também são proporcionais à velocidade angular. Portanto, não é possível eliminar todas as causas de vibração em uma máquina por meio do balanceamento.
Vibração de mecanismos.
A vibração é a reação do projeto do mecanismo aos efeitos de uma força excitatória cíclica. Essa força pode ser de diferentes naturezas.
A força centrífuga resultante do rotor desbalanceado é uma força não compensada que atua sobre o "ponto pesado". É essa força e a vibração causada por ela que podem ser eliminadas com o balanceamento do rotor.
Forças de interação de natureza "geométrica" decorrentes de erros de fabricação e montagem das peças conjugadas. Essas forças podem, por exemplo, surgir como resultado da falta de circularidade dos pescoços dos eixos, erros nos perfis dos dentes das engrenagens, ondulação das pistas dos rolamentos, desalinhamento dos eixos correspondentes etc. No caso de não circularidade dos munhões, o eixo do eixo será deslocado dependendo do ângulo de rotação do eixo. Embora essa vibração também ocorra na velocidade do rotor, é quase impossível eliminá-la por meio do balanceamento.
Forças aerodinâmicas resultantes da rotação dos impulsores de ventiladores e outros mecanismos de palhetas. Forças hidrodinâmicas resultantes da rotação dos impulsores de bombas hidráulicas, turbinas, etc.
Forças eletromagnéticas resultantes da operação de máquinas elétricas, por exemplo, enrolamentos de rotor assimétricos, enrolamentos em curto-circuito, etc.
A magnitude da vibração (por exemplo, sua amplitude Av) depende não apenas da força excitatória Fv que atua no mecanismo com frequência circular ω, mas também da rigidez k do mecanismo, de sua massa m , bem como do coeficiente de amortecimento C.
Vários tipos de sensores podem ser usados para medir mecanismos de vibração e equilíbrio, incluindo:
sensores de vibração absolutos projetados para medir a aceleração da vibração (acelerômetros) e sensores de velocidade de vibração;
sensores de vibração relativa - de corrente de Foucault ou capacitivos, projetados para medir o deslocamento da vibração. Em alguns casos (quando o projeto do mecanismo permite), os sensores de força também podem ser usados para avaliar sua carga de vibração. Em particular, eles são amplamente usados para medir a carga de vibração de suportes de máquinas de balanceamento com rolamentos rígidos.
Portanto, a vibração é a reação de uma máquina à ação de forças externas. A magnitude da vibração depende não apenas da magnitude da força que atua no mecanismo, mas também da rigidez do projeto do mecanismo. Uma mesma força pode levar a diferentes vibrações. Em uma máquina de rolamento rígido, mesmo que a vibração seja pequena, os rolamentos podem estar sujeitos a cargas dinâmicas significativas. É por isso que os sensores de força, em vez de sensores de vibração (acelerômetros de vibração), são usados no balanceamento de máquinas de rolamento rígido.
Os sensores de vibração são usados em mecanismos com suportes relativamente flexíveis, quando a ação de forças centrífugas desequilibradas leva a uma deformação perceptível dos suportes e à vibração. Os sensores de força são usados em suportes rígidos, quando mesmo forças significativas devido ao desequilíbrio não levam a uma vibração significativa.
A ressonância é um fator que impede o equilíbrio
Mencionamos anteriormente que os rotores são divididos em rígidos e flexíveis. A rigidez ou flexibilidade do rotor não deve ser confundida com a rigidez ou mobilidade dos suportes (fundação) nos quais o rotor está instalado. Um rotor é considerado rígido quando sua deformação (flexão) sob a ação de forças centrífugas pode ser desprezada. A deformação do rotor flexível é relativamente grande e não pode ser desprezada.
Neste artigo, consideramos apenas o balanceamento de rotores rígidos. Um rotor rígido (não deformável) pode, por sua vez, ser montado em suportes rígidos ou móveis (flexíveis). É claro que essa rigidez/suspensão dos suportes também é relativa, dependendo da velocidade do rotor e da magnitude das forças centrífugas resultantes. Um limite condicional é a frequência das vibrações naturais dos suportes do rotor.
Para sistemas mecânicos, a forma e a frequência das vibrações naturais são determinadas pela massa e pela elasticidade dos elementos do sistema mecânico. Ou seja, a frequência das vibrações naturais é uma característica interna do sistema mecânico e não depende de forças externas. Ao serem desviados do estado de equilíbrio, os suportes, devido à elasticidade, tendem a retornar à posição de equilíbrio. Porém, devido à inércia do rotor maciço, esse processo tem a natureza de oscilações amortecidas. Essas vibrações são as vibrações naturais do sistema de suporte do rotor. Sua frequência depende da relação entre a massa do rotor e a elasticidade dos suportes.
Quando o rotor começa a girar e a frequência de sua rotação se aproxima da frequência das vibrações naturais, a amplitude da vibração aumenta drasticamente, o que pode levar à destruição da estrutura.
Ocorre o fenômeno da ressonância mecânica. Na área de ressonância, uma mudança na velocidade de rotação de 100 rpm pode levar a um aumento na vibração de dezenas de vezes. Ao mesmo tempo (na área de ressonância), a fase de vibração muda em 180°.
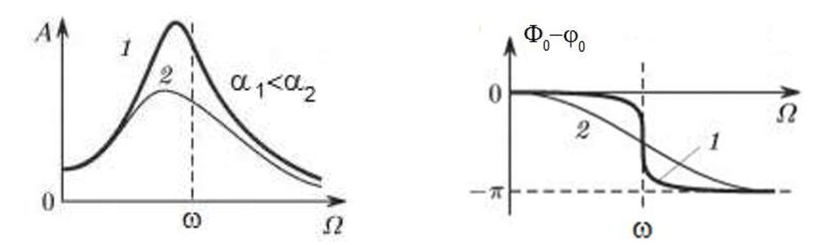
Fig.5 Alterações na amplitude e na fase das oscilações de um sistema mecânico quando a frequência de uma força externa muda.
Se o projeto do mecanismo não for bem-sucedido e a frequência de operação do rotor estiver próxima da frequência das vibrações naturais, a operação do mecanismo se tornará impossível devido à vibração inadmissivelmente alta. Isso não é possível da maneira usual, pois mesmo uma pequena alteração na velocidade causará uma mudança drástica nos parâmetros de vibração. Para o balanceamento na área de ressonância, são usados métodos especiais não considerados neste artigo.
É possível determinar a frequência das vibrações naturais do mecanismo em repouso (ao desligar a rotação do rotor) ou pelo método de choque com a análise espectral subsequente da resposta do sistema ao choque.
Para mecanismos cuja frequência de trabalho de rotação está acima da frequência de ressonância, ou seja, trabalhando no regime de ressonância, os suportes são considerados móveis e, para a medição, são usados sensores de vibração, principalmente vibroacelerômetros, que medem a aceleração dos elementos estruturais. Para mecanismos que operam no modo pré-ressonante, os suportes são considerados rígidos. Nesse caso, são usados sensores de força.
Modelos lineares e não lineares de um sistema mecânico. A não linearidade é um fator que impede o equilíbrio
No balanceamento de rotores rígidos, os modelos matemáticos chamados de modelos lineares são usados para os cálculos de balanceamento. Um modelo linear significa que, nesse modelo, uma quantidade é proporcional (linear) à outra. Por exemplo, se a massa não compensada no rotor for duplicada, o valor da vibração também será duplicado. Para rotores rígidos, um modelo linear pode ser usado, pois eles não se deformam.
Para rotores flexíveis, o modelo linear não pode mais ser usado. Em um rotor flexível, se a massa do ponto pesado aumentar durante a rotação, ocorrerá uma deformação adicional e, além da massa, o raio do local do ponto pesado também aumentará. Portanto, em um rotor flexível, a vibração aumentará mais de duas vezes, e os métodos usuais de cálculo não funcionarão.
Além disso, a mudança de elasticidade dos suportes em suas grandes deformações, por exemplo, quando em pequenas deformações dos suportes alguns elementos estruturais funcionam e, em grandes deformações, outros elementos estruturais estão envolvidos. É por isso que não é possível equilibrar mecanismos que não estejam fixados em uma fundação, mas, por exemplo, simplesmente colocados no chão. Com vibrações significativas, a força do desequilíbrio pode puxar o mecanismo para fora do piso, alterando significativamente as características de rigidez do sistema. Os pés do motor devem ser fixados com segurança, os suportes dos parafusos devem ser apertados, a espessura da arruela deve proporcionar rigidez de montagem suficiente, etc. Se os rolamentos estiverem quebrados, é possível que haja desalinhamento significativo do eixo e choques, o que também resultará em linearidade ruim e incapacidade de realizar um balanceamento de qualidade.
Dispositivos de balanceamento e máquinas de balanceamento
Conforme observado acima, o balanceamento é o processo de alinhamento do eixo central principal de inércia com o eixo de rotação do rotor.
Esse processo pode ser realizado por dois métodos.
O primeiro método envolve a usinagem dos munhões do rotor de forma que o eixo que passa pelos centros dos munhões cruze a seção com o eixo central principal de inércia do rotor. Essa técnica raramente é usada na prática e não será discutida em detalhes neste artigo.
O segundo método (mais comum) envolve mover, instalar ou remover pesos de correção no rotor, que são colocados de modo que o eixo de inércia do rotor fique o mais próximo possível de seu eixo de rotação.
A movimentação, adição ou remoção de pesos de correção durante o balanceamento pode ser realizada por meio de várias operações tecnológicas, incluindo: perfuração, fresagem, revestimento, soldagem, parafusamento ou desparafusamento, queima a laser ou por feixe de elétrons, eletrólise, revestimento eletromagnético etc.
O processo de balanceamento pode ser realizado de duas maneiras:
- balanceamento de rotores montados (em seus próprios rolamentos) usando máquinas de balanceamento;
- balanceamento de rotores em máquinas de balanceamento. Para o balanceamento de rotores em seus próprios rolamentos, geralmente são usados dispositivos (kits) de balanceamento especializados, que permitem medir a vibração do rotor balanceado em sua frequência de rotação na forma vetorial, ou seja, medir a amplitude e a fase da vibração. Atualmente, os dispositivos acima são fabricados com base na tecnologia de microprocessador e (além da medição e análise da vibração) fornecem o cálculo automático dos parâmetros dos pesos de correção, que devem ser instalados no rotor para compensar seu desbalanceamento.
Esses dispositivos incluem:
- uma unidade de medição e computação baseada em um computador ou controlador industrial;
- Dois (ou mais) sensores de vibração;
- Um sensor de ângulo de fase;
- acessórios para montagem dos sensores no local;
- software especializado, projetado para realizar um ciclo completo de medição dos parâmetros de vibração do rotor em um, dois ou mais planos de correção.
Atualmente, dois tipos de máquinas de balanceamento são os mais comuns:
- Máquinas de rolamentos macios (com suportes macios);
- Máquinas com rolamentos rígidos (com suportes rígidos).
As máquinas de rolamentos macios têm suportes relativamente flexíveis, por exemplo, baseados em molas planas. A frequência das vibrações naturais desses suportes é geralmente de 2 a 3 vezes menor do que a frequência de rotação do rotor de balanceamento, que é montado neles. Os sensores de vibração (acelerômetros, sensores de velocidade de vibração, etc.) são normalmente usados para medir a vibração dos suportes pré-ressonantes da máquina.
As máquinas de balanceamento de pré-ressonância usam suportes relativamente rígidos, cujas frequências naturais de vibração devem ser de 2 a 3 vezes maiores do que a frequência de rotação do rotor que está sendo balanceado. Os transdutores de força geralmente são usados para medir a carga de vibração dos suportes da máquina de pré-ressonância.
A vantagem das máquinas de balancear pré-ressonância é que o balanceamento nelas pode ser realizado em velocidades de rotor relativamente baixas (até 400 - 500 rpm), o que simplifica muito o projeto da máquina e de sua fundação, além de aumentar a produtividade e a segurança do balanceamento.
Balanceamento de rotores rígidos
Importante!
- O balanceamento elimina apenas a vibração causada pela distribuição assimétrica da massa do rotor em relação ao seu eixo de rotação. Outros tipos de vibração não são eliminados pelo balanceamento!
- Mecanismos técnicos, cujo projeto garante a ausência de ressonâncias na frequência operacional de rotação, fixados de forma confiável na fundação, instalados em rolamentos que podem ser reparados, estão sujeitos a balanceamento.
- As máquinas com defeito devem ser reparadas antes do balanceamento. Caso contrário, não será possível fazer um balanceamento de qualidade.
O balanceamento não substitui o reparo!
A principal tarefa do balanceamento é encontrar a massa e a localização dos pesos de compensação que estão sujeitos a forças centrífugas de balanceamento.
Como mencionado acima, para rotores rígidos, geralmente é necessário e suficiente instalar dois pesos de compensação. Isso eliminará o desequilíbrio estático e dinâmico do rotor. O esquema geral para medir a vibração durante o balanceamento é o seguinte.
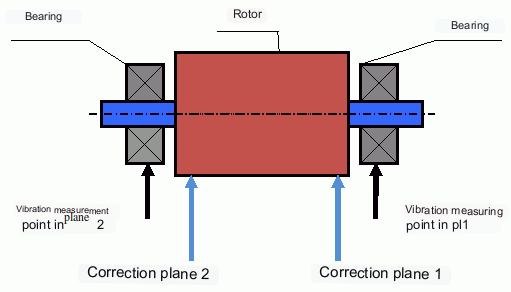
Fig. 6 Seleção dos pontos de medição e locais dos pesos (planos de correção) ao fazer o balanceamento em dois planos
Os sensores de vibração são instalados nos suportes dos rolamentos nos pontos 1 e 2. Um marcador de rotação é fixado no rotor, geralmente com fita reflexiva. A marca de RPM é usada pelo tacômetro a laser para determinar a velocidade do rotor e a fase do sinal de vibração.
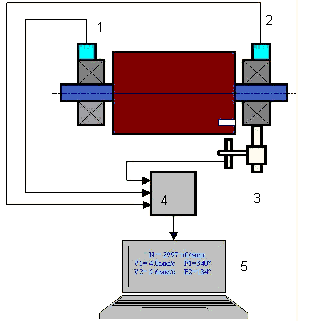
Fig. 7. Instalação dos sensores durante o balanceamento em dois planos. 1,2 - sensores de vibração, 3 - marcador, 4 - unidade de medição, 5 - notebook
Na maioria dos casos, o balanceamento dinâmico é realizado pelo método das três partidas. O método baseia-se no fato de que pesos de teste de peso conhecido são colocados no rotor em série nos planos 1 e 2, e os pesos e a localização dos pesos de balanceamento são calculados com base nos resultados das alterações nos parâmetros de vibração.
O local de instalação dos pesos é chamado de plano de correção. Normalmente, os planos de correção são selecionados na área dos suportes de rolamento nos quais o rotor está instalado.
Na primeira partida, a vibração inicial é medida. Em seguida, um peso de teste de peso conhecido é colocado no rotor mais próximo de um dos rolamentos. Uma segunda partida é realizada e os parâmetros de vibração são medidos, que devem mudar devido à instalação do peso de teste. Em seguida, o peso de teste no primeiro plano é removido e instalado no segundo plano. Um terceiro teste é realizado e os parâmetros de vibração são medidos. O peso de teste é removido e o software calcula automaticamente as massas e os ângulos de instalação dos pesos da balança.
O objetivo da instalação dos pesos de teste é determinar como o sistema reage às mudanças no desequilíbrio. Os pesos e os locais dos pesos de teste são conhecidos, de modo que o software pode calcular os chamados coeficientes de influência, mostrando como a introdução de um desequilíbrio conhecido afeta os parâmetros de vibração. Os coeficientes de influência são características do próprio sistema mecânico e dependem da rigidez dos suportes e da massa (inércia) do sistema de suporte do rotor.
Para o mesmo tipo de mecanismos do mesmo projeto, os coeficientes de influência serão próximos. É possível salvá-los na memória do computador e usá-los para o balanceamento dos mecanismos do mesmo tipo sem execuções de teste, o que aumenta significativamente a produtividade do balanceamento. Observe que a massa dos pesos de teste deve ser escolhida de forma que os parâmetros de vibração mudem visivelmente quando os pesos de teste forem instalados. Caso contrário, o erro de cálculo dos coeficientes de influência aumenta e a qualidade do balanceamento se deteriora.
Como você pode ver na Fig. 1, a força centrífuga atua na direção radial, ou seja, perpendicularmente ao eixo do rotor. Portanto, os sensores de vibração devem ser instalados de modo que seu eixo de sensibilidade também aponte na direção radial. Normalmente, a rigidez da fundação na direção horizontal é menor, portanto, a vibração na direção horizontal é maior. Portanto, para aumentar a sensibilidade, os sensores devem ser instalados de modo que seu eixo de sensibilidade também seja direcionado horizontalmente. Embora não haja nenhuma diferença fundamental. Além da vibração na direção radial, a vibração na direção axial, ao longo do eixo de rotação do rotor, deve ser monitorada. Essa vibração geralmente não é causada pelo desbalanceamento, mas por outras causas, principalmente relacionadas ao desalinhamento e ao desalinhamento dos eixos conectados por meio do acoplamento.
Essa vibração não pode ser eliminada por meio do balanceamento e, nesse caso, o alinhamento é necessário. Na prática, essas máquinas geralmente apresentam desequilíbrio do rotor e desalinhamento do eixo, o que torna a tarefa de eliminar a vibração muito mais difícil. Nesses casos, é necessário primeiro centralizar a máquina e depois balanceá-la. (Embora com forte desequilíbrio de torque, a vibração também ocorre na direção axial devido à "torção" da estrutura da fundação).
Exemplos de bancadas para balanceamento de rotores pequenos que discutimos em nossos outros artigos:
Suporte de equilíbrio com apoio macio.
Balanceamento dos rotores de motores elétricos.
Suportes de balanceamento simples para rotores: projeto e aplicação
Critérios para avaliar a qualidade dos mecanismos de balanceamento.
A qualidade do balanceamento de rotores (mecanismos) pode ser avaliada de duas maneiras. O primeiro método envolve a comparação da quantidade de desbalanceamento residual determinada durante o processo de balanceamento com a tolerância para desbalanceamento residual. Essas tolerâncias para as diferentes classes de rotores estão especificadas na ISO 1940-1-2007. Parte 1. Definição de desbalanceamento permitido.
No entanto, a conformidade com as tolerâncias especificadas não pode garantir totalmente a confiabilidade operacional do mecanismo, associada à obtenção do nível mínimo de vibração. Isso é explicado pelo fato de que a magnitude da vibração do mecanismo é determinada não apenas pela magnitude da força associada ao desequilíbrio residual do rotor, mas também depende de vários outros parâmetros, incluindo: a rigidez k dos elementos estruturais do mecanismo, sua massa m, o fator de amortecimento e a frequência de rotação. Portanto, para estimar as qualidades dinâmicas do mecanismo (incluindo a qualidade de seu equilíbrio) em vários casos, recomenda-se estimar o nível de vibração residual do mecanismo, que é regulado por vários padrões.
A norma mais comum, que regula os níveis admissíveis de vibração dos mecanismos, é a ISO 10816-3-2002. Com sua ajuda, é possível definir tolerâncias para qualquer tipo de máquina, levando em conta a potência de seu acionamento elétrico.
Além desse padrão universal, há uma série de padrões especializados desenvolvidos para tipos específicos de máquinas. Por exemplo, 31350-2007 , ISO 7919-1-2002, etc.
ISO 1940-1-2007. "Vibração. Requisitos para a qualidade de balanceamento de rotores rígidos. Parte 1. Determinação do desequilíbrio permissível".
ISO 10816-3:2009 Preview Mechanical vibration - Evaluation of machine vibration by measurements on non-rotating parts - Part 3: Industrial machines with nominal power above 15 kW and nominal speeds between 120 r/min and 15 000 r/min when measured in situ."
ISO 14694:2003 "Ventiladores industriais - Especificações para qualidade de equilíbrio e níveis de vibração",
ISO 7919-1-2002 "Vibração de máquinas sem movimento alternativo. Medições em eixos rotativos e critérios de avaliação. Orientação geral".