Simple Balancing Stands for Rotors: Design and Application
Rotor balancing is an important stage in the production and operation of rotating equipment. High-quality balancing reduces vibrations, increases the lifespan of bearings and mechanisms, and enhances the overall efficiency of the equipment. This article examines simple balancing stands that provide high-quality balancing of various types of rotors with minimal costs. These stands are suitable for balancing small and medium rotors used in various mechanisms.
The basis of the design of such stands is a flat plate or frame mounted on cylindrical compression springs. The springs are selected so that the natural frequency of oscillation of the plate with the balanced mechanism mounted on it is 2-3 times lower than the rotational frequency of the rotor of this mechanism during balancing.
1. Stand for Balancing Abrasive Wheels
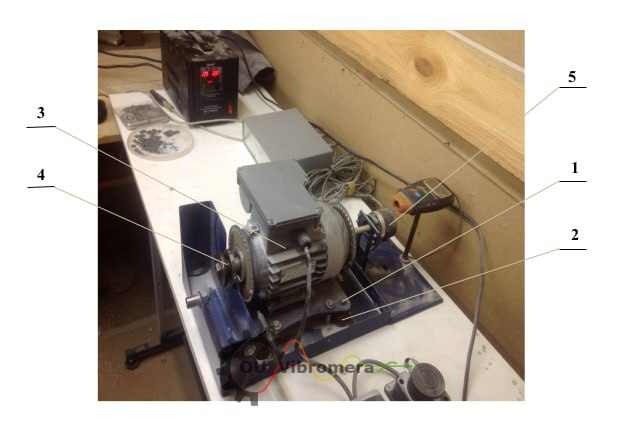
Purpose: Balancing abrasive wheels.
Main components:
- Plate (1): Mounted on four cylindrical springs (2).
- Electric Motor (3): The rotor of the motor simultaneously serves as a spindle on which an arbor (4) is mounted for attaching the abrasive wheel.
- Impulse Sensor (5): Measures the rotation angle of the motor rotor and is used in the “Balanceset” measuring system to determine the angular position for removing the corrective mass from the abrasive wheel.
Operating Principle: The stand allows determining and eliminating the imbalance of the abrasive wheel by measuring vibration and identifying the angular position of the imbalance point.
Features: The presence of an impulse rotation angle sensor for precise determination of the mass correction point.
2. Stand for Balancing Vacuum Pumps
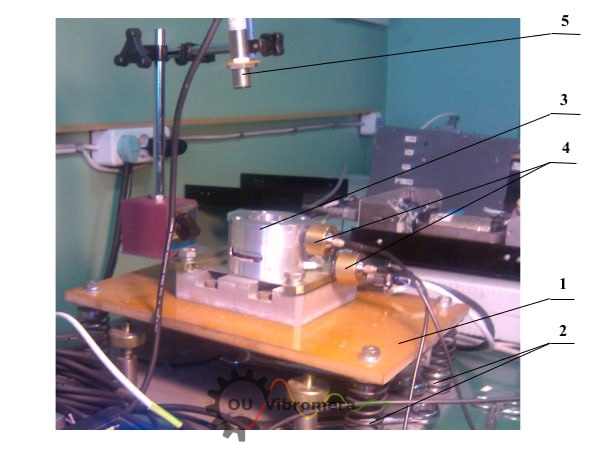
Purpose: Balancing vacuum pumps.
Main Components:
- Plate (1): Mounted on cylindrical springs (2).
- Vacuum Pump (3): Installed on the plate and has its own electric drive with adjustable rotational speed from 0 to 60,000 rpm.
- Vibration Sensors (4): Mounted on the pump housing and measure vibration in two different sections along the height.
- Laser Phase Angle Sensor (5): Used to synchronize the vibration measurement process with the rotation angle of the pump rotor.
Operating Principle: The pump’s vibration is measured by sensors (4), and the laser sensor (5) synchronizes the measurements with the rotor’s rotation angle, allowing determination of the location and magnitude of the imbalance.
Features: Capability of balancing at high rotational speeds (up to 60,000 rpm) and the use of a laser sensor for precise synchronization.
Results: At subcritical speeds, the residual imbalance of the pump rotor meets the requirements of balance quality grade G0.16 according to ISO 1940-1-2007 “Mechanical vibration—Requirements for the balancing quality of rotors in a constant (rigid) state—Part 1: Specification and verification of balance tolerances.” The residual vibration of the pump housing at speeds up to 8,000 rpm does not exceed 0.01 mm/s.
3. Stands for Balancing Fans
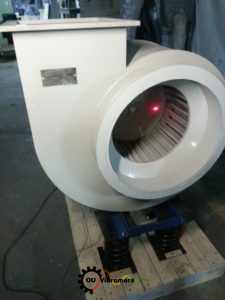
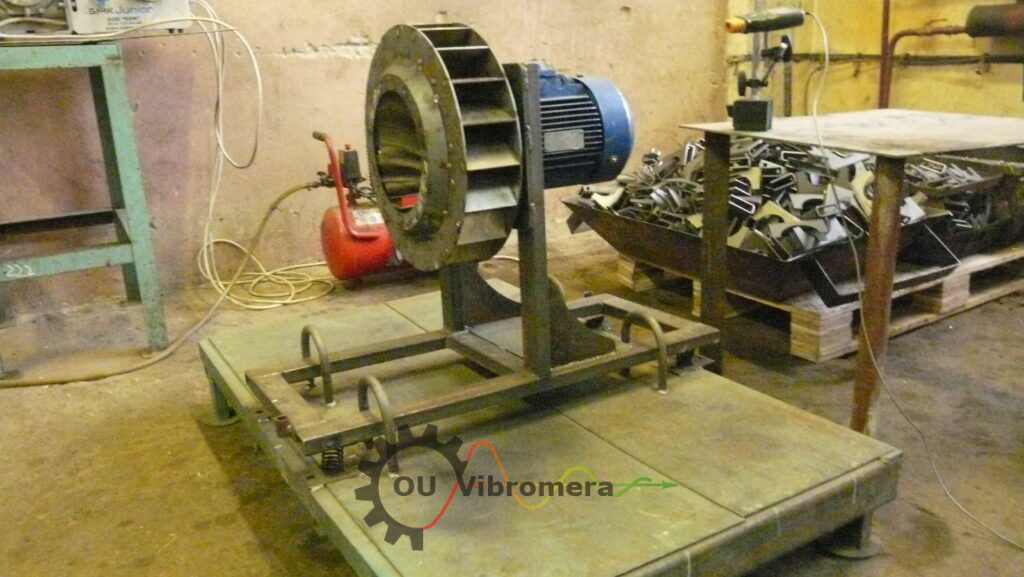
Purpose: Balancing fans.
Main Components: The design is similar to the previous stands, featuring a plate on springs with a fan mounted on it.
Operating Principle: Measuring the fan’s vibration and adjusting the mass to eliminate imbalance.
Results: On the stand shown in Fig. 3, a residual vibration level of 0.8 mm/s was achieved, which is more than three times better than the permissible value for fans of category BV5 according to ISO 14694-2003 “Industrial Fans—Specifications for Balance Quality and Vibration Levels.” On another stand used in the mass production of duct fans, the residual vibration consistently does not exceed 0.1 mm/s.
Conclusion
Simple balancing stands based on a plate mounted on springs are an effective and economical solution for high-quality balancing of various types of rotors. They allow achieving low levels of residual vibration, complying with international standards. Such stands are widely used in the production and repair of equipment, ensuring its reliable and long-lasting operation.