Introduction
Dynamic balancing is a critical procedure for maintaining the operational integrity and performance of rotary equipment, particularly in industrial blower systems. Imbalanced blower rotors can cause multiple operational issues including increased mechanical stress, elevated noise levels, accelerated wear of bearings, and excessive energy consumption. This article focuses on analyzing high vibration levels in various types of blowers—squirrel cage, centrifugal, turbine, lobe, rotary vane, and blower wheels—and outlines the dynamic balancing procedure using the Balanset-1A portable vibration analyzer from Vibromera.
Issues Associated with Elevated Vibration in Blower Systems
- Component Fatigue: Continuous exposure to unbalanced forces results in material fatigue, leading to premature failure of blower components.
- Operational Inefficiency: An unbalanced rotor disrupts aerodynamic performance and increases energy demand due to added mechanical resistance.
- Accelerated Bearing Wear: Elevated vibration loads the bearings disproportionately, reducing their operational life and increasing maintenance frequency.
- Noise Pollution: Rotor imbalance generates periodic forces that translate into noticeable noise, which may exceed permissible occupational thresholds.
- Structural Resonance: If operating speeds approach the system’s critical frequencies, resonance can lead to uncontrolled vibration amplitudes and potential system failure.
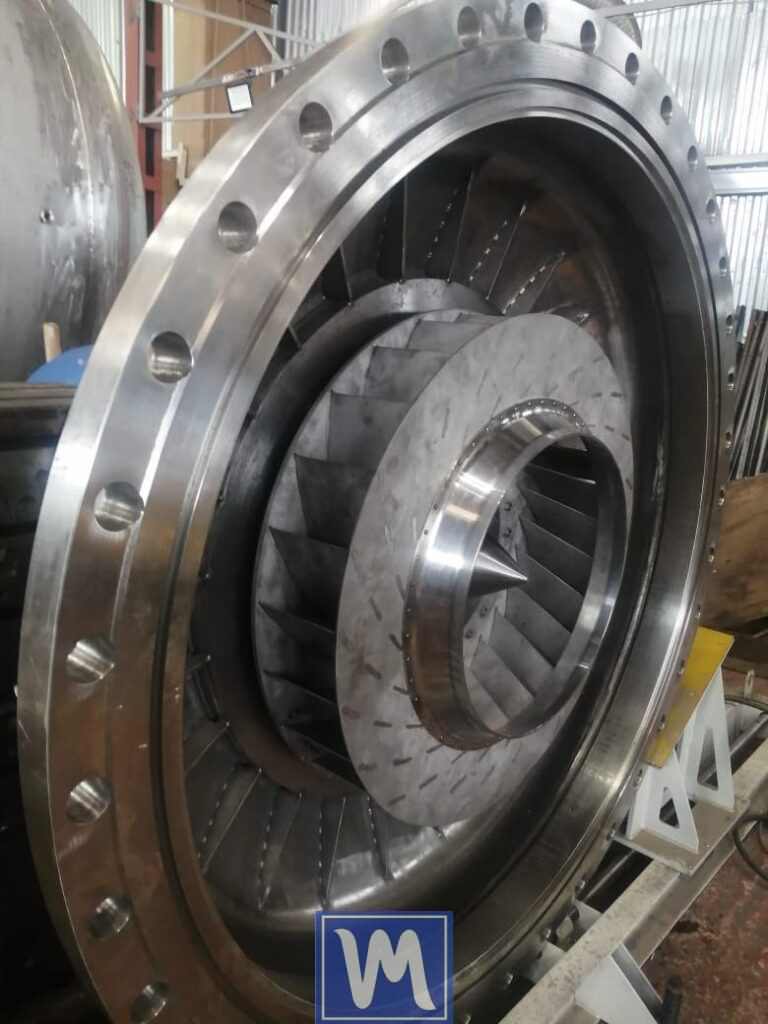
Two-plane dynamic balancing of an industrial radial fan using Balanset-1A by Vibromera
Process of Dynamic Balancing Using Balanset-1A
- Initial Diagnostic Assessment: Balanset-1A captures baseline vibration and RPM data using two accelerometers and a laser tachometer, delivering accurate phase and amplitude readings.
- In-Situ Balancing: This system supports dynamic balancing directly in operational conditions using the machine’s native bearings, ensuring minimal downtime and greater practicality.
- Trial Weight Attachment: Calibrated weights are temporarily attached to the rotor to determine system response, aiding in calculating influence coefficients for precise correction.
- Data Analysis and Calculations: The Balanset-1A software computes the optimal correction weights and angular positions using advanced algorithms and ISO 1940-based tolerance checks.
- Final Verification: A verification run confirms that vibration amplitudes have decreased within acceptable limits, ensuring compliance and rotor health.
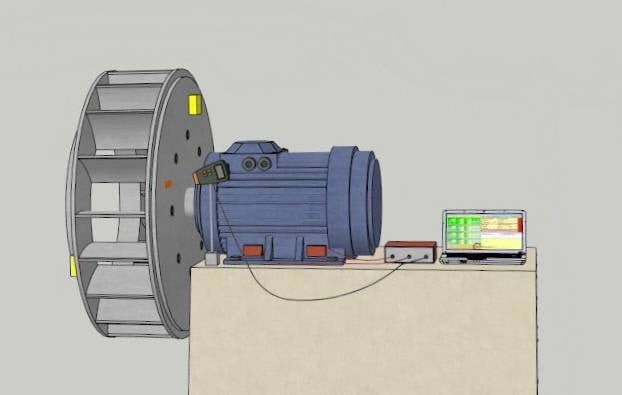
Balanset-1A portable dynamic balancer and vibration analyzer by Vibromera
Technical Specifications of Balanset-1A
Balanset-1A operates within a vibration velocity range of 0.02–80 mm/s and supports rotational speeds from 100 to 100,000 RPM. It measures vibration phase angles with ±1° accuracy and performs FFT spectrum analysis in the 5–550 Hz range. The device allows balancing in one or two planes, automatically calculating influence coefficients and permissible imbalance levels in accordance with ISO 1940.
Application Versatility for Various Blower Types
Balanset-1A is effective for balancing industrial blowers of all types, including axial fans, radial impellers, multistage centrifugal fans, HVAC units, combustion air blowers, and exhaust systems. The system is adaptable to both high-speed and low-speed configurations, making it ideal for energy and manufacturing sectors.
Comparison with Traditional Balancing Methods
Unlike fixed-station balancing machines, which require rotor removal and transportation to a balancing bench, Balanset-1A enables on-site correction. This not only preserves alignment and bearing setup but also significantly accelerates the maintenance process. Additionally, traditional methods often lack the ability to store historical vibration data, which Balanset-1A provides via digital archiving and data export capabilities.
Advantages of In-Situ Balancing with Balanset-1A
- Time and Cost Efficiency: Avoids dismounting the rotor, significantly reducing machine downtime and associated operational costs.
- Elimination of Reassembly Errors: As no disassembly is required, the risk of misalignment or assembly-related defects is eliminated.
- Precision: Balanset-1A’s dual-channel real-time data acquisition and FFT analysis ensure accurate phase detection and corrective measures, even in noisy industrial environments.
Conclusion
Effective dynamic balancing is essential for extending the service life and ensuring the performance of blower systems. Tools like the Balanset-1A offer a reliable, user-friendly, and highly accurate solution for both preventive maintenance and troubleshooting. By eliminating imbalance-related issues directly on-site, this device supports safer operations and better energy efficiency across industrial applications. Investing in professional balancing equipment is a proactive step toward maintaining mechanical reliability and reducing unexpected downtime.
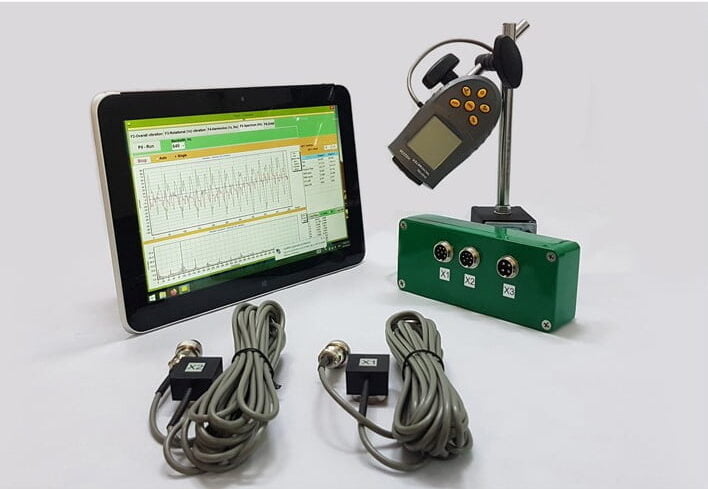
Portable vibration analyzer Balanset-1A by Vibromera
0 Comments