With the Balanset-1A you can measure the relative vibration of the rotor using non-contact linear encoders.
1.1 Selection of the sensor type and setting.
Depending on the task, either vibration sensors or displacement sensors can be used for measurements.
To select the type of sensor it is necessary on the panel “Sensor type” (at the bottom of the main window) to put a mark in the field “Vibro” or “Linear”.
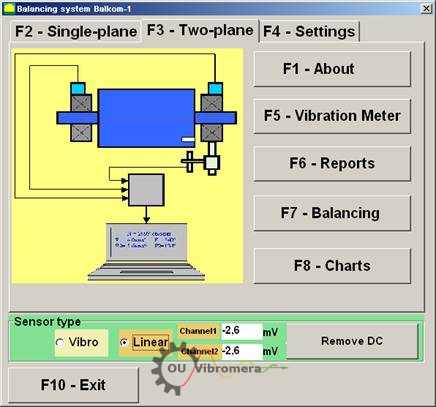
Fig. 1. The main working window of the Balanset program.T
Before starting the measurement it is necessary to make sure that the conversion coefficients of the sensors are set correctly. For this purpose press the button “F4-Settings” in the main working window of the program (see Fig. 1) and go to the settings window designed for entering conversion coefficients (see Fig. 2).
In the working window shown in Fig. 2, in the corresponding fields the conversion coefficients of linear and vibration sensors should be entered. These coefficients are specified in the instrument passport. Usually you do not need to change them.
For the linear displacement sensors used in the set of the Balanset-1A instrument, the conversion coefficients are respectively equal to:
Kprl1= 0.94 mV/μm (conversion coefficient of the sensor of the 1st channel);
Kprl2 = 0.94 mV/μm (conversion coefficient of the sensor of the 2nd channel.
For proper operation, the linear encoder must be installed at a certain distance from the surface of the object of measurement. The nominal clearance between the surface and the end of the sensor is 3.5 mm. In this case there is a constant voltage of 2.48 volts at the sensor output. This voltage will be shown in the fields “Channel1” and “Channel2” for the first and second channels respectively.
To compensate it you must press the button “Remove DC”. A small residual offset will not interfere with the measurement.
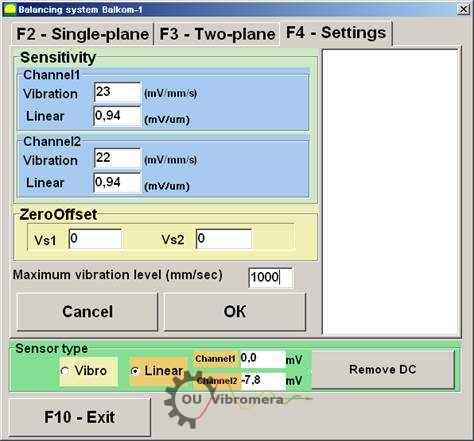
Fig. 2. Working window for entering conversion coefficients and selecting the type of used sensors
Attention!
The specified values of nominal clearance and the conversion factors of the linear encoders are given for rotors made of steel.
For rotors made of other metals (copper, bronze, aluminum) nominal clearance and sensors conversion coefficients should be determined experimentally by the user by conducting calibration.
To save the changed parameters press “OK” button. The new parameters will be saved in a file and used for further measurements.
1.2 Measuring the radial run-out of the rotor.
The radial run-out of the rotor can be measured with non-contact probes in two planes according to the scheme shown in fig. 3.
In order to measure and plot the time function and rotor run-out spectrum, if necessary, a number of preparatory operations must be carried out, including:
– select diametrical sections of the rotor, in which the measurements will be carried out;
– to install non-contact linear displacement sensors 5 and 6 and phase angle sensor 7 on the machine bed using special devices (e.g. magnetic tripods);
– connect proximity sensors of linear motion to connectors X1 and X2, and phase angle sensor to connector X3 of the measuring unit;
– set a nominal measuring gap ∆ between the rotor surface and the sensing element for each linear encoder (for the rotor made of steel ∆ = 3.5 mm);
– place on the rotor the reflective mark required for triggering for the phase angle sensor 7 and check the sensor triggering;
– connect the measuring unit to the computer.
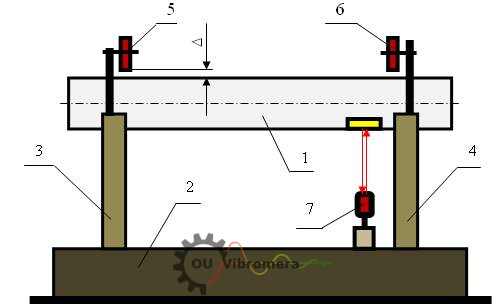
Fig. 3. Measuring the radial run-out of the rotor
If you press the button “F8 – Charts” in the main working window (see Fig. 1), the computer display shows the working window “Graphs” (see Fig. 5), designed to build different kinds of graphs of radial run-out of the rotor.
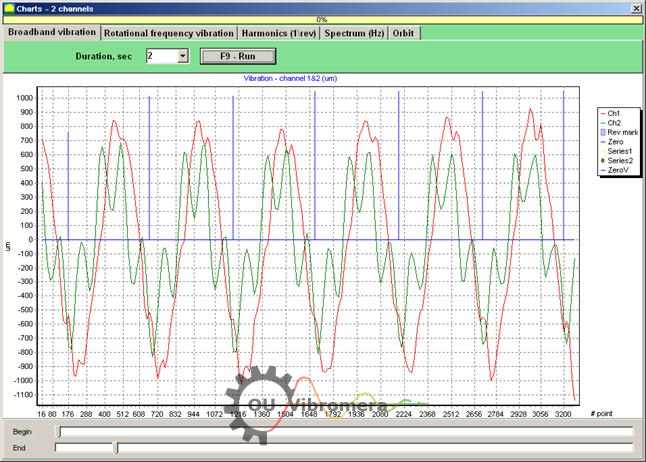
Fig. 5. The working window of the “Charts” mode
When you press the “Broadband vibration” button in this window, the time function of the rotor radial runout is displayed.
If the “Rotation frequency vibration” button is pressed, the time function of the reciprocal component of the rotor radial runout is displayed.
If you press the button “Harmonics (1/rev)”, the display will show a decomposition graph of the rotor runout into a harmonic series. The first harmonic corresponds to the value of vibration at the reverse rotor frequency (1x), the second one – at the double frequency (2x), etc.
By pressing the button “Spectrum (Hz)” the display shows the spectrum of the radial run-out of the rotor.
By pressing the button “Orbit” the graph of rotor orbit (precession) is displayed.
1.3 Construction of the rotor orbit graph.
Construction of the rotor orbit graph can be performed according to the scheme shown in Fig. 6.
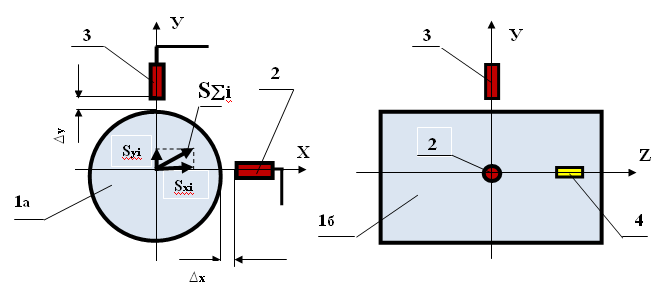
Fig. 6. Scheme of rotor orbit measurement 1a – rotor (end view); 1b – rotor (side view); 2, 3 – non-contact sensors; 4 – reflection mark of phase angle sensor.
In order to make a measurement and build a corresponding graph, it is necessary to carry out a number of preparatory operations, including:
– install the non-contact linear encoders 2 and 3 in one of the diametrical sections of the rotor at an angle of 90° to each other, provided that the measuring axis of encoder 2 must coincide with the X axis, and the measuring axis of encoder 3 must coincide with the Y axis;
– set the nominal measuring gap ∆x (∆u) between the rotor surface and the sensing element of each linear encoder (for steel ∆ = 3.5 mm);
– set the phase angle sensor (not shown in the scheme) in the X – Z plane, coinciding with the installation plane of non-contact sensor 2;
– set a reflective mark 4 on the rotor 1 in the X – Z plane, which is necessary for the phase angle sensor operation;
– connect non-contact linear encoders 2 and 3 to connectors X1 and X2, and phase angle encoder to connector X3 of the measuring unit;
– connect the measuring unit to the computer.
To start measuring the rotor orbit in the main working window (see Fig. 1)
Press the button “F8 – Charts” and go to the working window “Graphs” (see Fig. 5), which is designed to build different kinds of graphs of radial runout of the rotor.
In this working window you must press the button “Orbit”, after which the working window appears on the computer display, in which the necessary cycle of measurements is made (see Fig. 7).
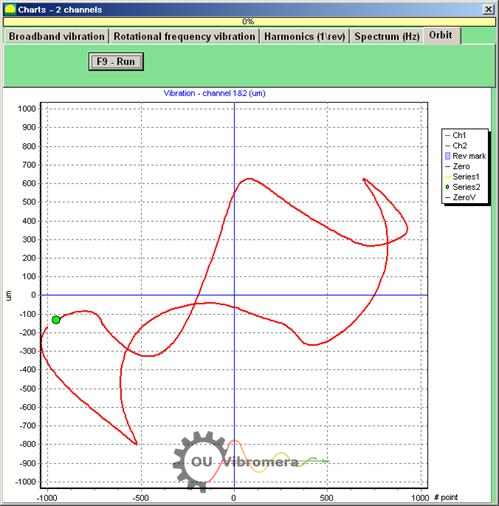
Fig.7. Graph of the rotor orbit. Balanset software.
To continue the work in the specified working window (see Fig. 7) you must turn on the rotor rotation and by pressing the “F9 – RUN” button perform measurement of the instantaneous values of radial run-out of the rotor Sxi and Sui for a period equal to one rotor revolution.
The array of instantaneous values Sxi and Sui obtained during measurement is used to calculate the orbit coordinates of the controlled rotor, which is performed by the formula:
S∑i = √ (Sxi² + Syi²) (1)
where S∑i is the instantaneous value of the rotor orbit coordinate, calculated for the i-th point of the graph;
Sxi – instantaneous value of the radial run-out of the rotor, measured by coordinate X with the sensor 1 in the i-th point;
Sxi – instantaneous value of the rotor radial run-out, measured by coordinate Y with sensor 2 in the i-th point.