Rotorul este un corp care se rotește în jurul unei anumite axe și este ținut de suprafețele sale de sprijin în suporturi. Suprafețele de sprijin ale rotorului transmit sarcini către suporturi prin intermediul unor rulmenți sau lagăre de alunecare. Suprafețele de sprijin sunt suprafețele butucilor sau suprafețele care le înlocuiesc.
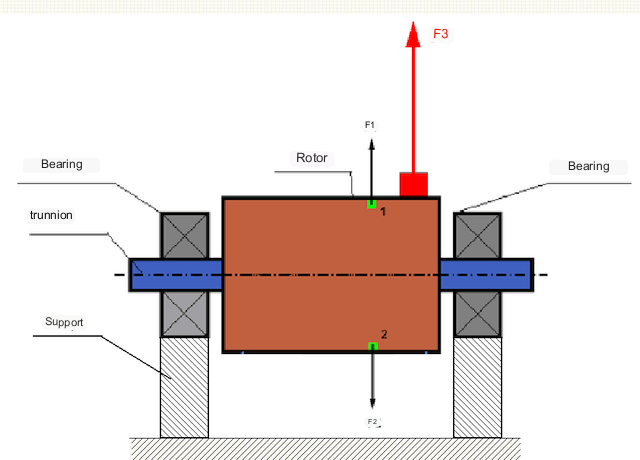
Fig.1 Rotorul și forțele centrifuge care acționează asupra lui.
Într-un rotor perfect echilibrat, masa sa este distribuită simetric în jurul axei de rotație, adică orice element al rotorului poate fi adaptat cu un alt element situat simetric în jurul axei de rotație. Într-un rotor echilibrat, forța centrifugă care acționează asupra oricărui element al rotorului este echilibrată de forța centrifugă care acționează asupra elementului simetric. De exemplu, forțele centrifuge F1 și F2, egale ca mărime și opuse ca direcție, acționează asupra elementelor 1 și 2 (marcate cu verde în figura 1). acest lucru este valabil pentru toate elementele simetrice ale rotorului și, astfel, forța centrifugă totală care acționează asupra rotorului este 0, iar rotorul este echilibrat.
Dar dacă simetria rotorului este ruptă (elementul asimetric este marcat cu roșu în fig.1), atunci asupra rotorului acționează forța centrifugă dezechilibrată F3.În timpul rotirii, această forță își schimbă direcția odată cu rotația rotorului. Sarcina dinamică rezultată din această forță este transmisă la rulmenți, ceea ce duce la o uzură accelerată.
În plus, sub influența acestei forțe cu direcție variabilă se produce o deformare ciclică a suporturilor și a fundației, pe care este fixat rotorul, adică se produc vibrații. Pentru a elimina dezechilibrul rotorului și vibrațiile care îl însoțesc, trebuie instalate mase de echilibrare pentru a restabili simetria rotorului.
Echilibrarea rotorului este o operațiune de corectare a dezechilibrului prin adăugarea de mase de echilibrare.
Sarcina de echilibrare este de a găsi dimensiunea și poziția (unghiul) uneia sau mai multor mase de echilibrare.
Tipuri de rotoare și tipuri de dezechilibru.
Ținând cont de rezistența materialului rotorului și de mărimea forțelor centrifuge care acționează asupra acestuia, rotoarele pot fi împărțite în două tipuri - rotoare rigide și rotoare flexibile.
Rotoarele rigide se deformează în mod nesemnificativ sub acțiunea forței centrifuge în modurile de lucru, iar influența acestei deformări în calcule poate fi neglijată.
Deformarea rotorilor flexibili nu mai poate fi neglijată. Deformarea rotoarelor flexibile complică rezolvarea problemei de echilibrare și necesită aplicarea altor modele matematice în comparație cu problema echilibrării rotoarelor rigide.Trebuie remarcat faptul că același rotor la viteze mici se poate comporta ca rigid, iar la viteze mari - ca flexibil. În cele ce urmează, vom lua în considerare doar echilibrarea rotorilor rigizi.
În funcție de distribuția maselor dezechilibrate de-a lungul lungimii rotorului, se pot distinge două tipuri de dezechilibru - static și dinamic (momentan). În consecință, se face referire la echilibrarea statică și dinamică a rotorului. Dezechilibrarea statică a rotorului apare fără rotația rotorului, adică în statică, atunci când rotorul este inversat de gravitație cu "punctul său greu" în jos. Un exemplu de rotor cu dezechilibru static este prezentat în figura 2.
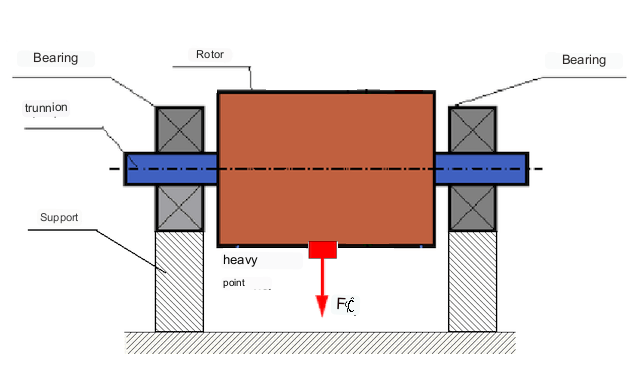
Fig.2 Dezechilibrul static al rotorului.
Sub acțiunea gravitației, "punctul greu" se întoarce în jos.
Dezechilibrul dinamic apare numai atunci când rotorul se rotește.
Un exemplu de rotor cu dezechilibru dinamic este prezentat în figura 3.
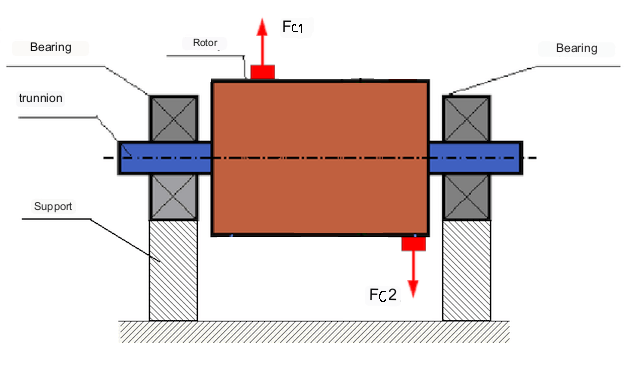
Fig.3 Dezechilibrul dinamic al rotorului.
Forțele Fc1 și Fc2 creează un moment care tinde să dezechilibreze rotorul.
În acest caz, masele egale dezechilibrate M1 și M2 se află în planuri diferite - în locuri diferite pe lungimea rotorului. În poziție statică, adică atunci când rotorul nu se rotește, doar gravitația acționează asupra rotorului, iar masele se echilibrează reciproc. În dinamică, atunci când rotorul se rotește, forțele centrifuge Fc1 și Fc2 încep să acționeze asupra maselor M1 și M2. Aceste forțe sunt egale ca mărime și opuse ca direcție. Cu toate acestea, deoarece sunt aplicate în locuri diferite de-a lungul lungimii arborelui și nu se află pe aceeași linie, aceste forțe nu se compensează reciproc. Forțele Fc1 și Fc2 creează un cuplu aplicat pe rotor. Prin urmare, acest dezechilibru se mai numește și dezechilibru de moment. În consecință, forțele centrifuge necompensate acționează asupra pozițiilor rulmenților, care pot depăși cu mult valorile calculate și pot reduce durata de viață a rulmenților.
Deoarece acest tip de dezechilibru apare numai în mod dinamic în timpul rotației rotorului, se numește dezechilibru dinamic. Acesta nu poate fi corectat în condiții statice prin echilibrare "la cuțite" sau prin metode similare. Pentru a elimina dezechilibrul dinamic, trebuie instalate două greutăți de compensare, care produc un moment egal ca mărime și de sens opus față de momentul care rezultă din masele M1 și M2. Nu este necesar ca masele de compensare să fie opuse și egale în mărime cu masele M1 și M2. Principalul lucru este ca acestea să producă un moment care să compenseze complet momentul de dezechilibru.
În general, este posibil ca masele M1 și M2 să nu fie egale între ele, astfel încât va exista o combinație de dezechilibru static și dinamic. S-a demonstrat teoretic că, pentru un rotor rigid, două greutăți distanțate pe lungimea rotorului sunt necesare și suficiente pentru a elimina dezechilibrul acestuia. Aceste greutăți vor compensa atât cuplul care rezultă din dezechilibrul dinamic, cât și forța centrifugă care rezultă din asimetria masei în raport cu axa rotorului (dezechilibru static). În mod obișnuit, dezechilibrul dinamic este caracteristic rotorilor lungi, cum ar fi arborii, iar dezechilibrul static este caracteristic rotorilor înguste. Cu toate acestea, dacă rotorul îngust este înclinat în raport cu axa sau deformat ("figura opt"), atunci dezechilibrul dinamic va fi dificil de eliminat. (a se vedea Fig. 4), deoarece în acest caz este dificil de instalat greutăți de corecție care să creeze momentul de compensare necesar.
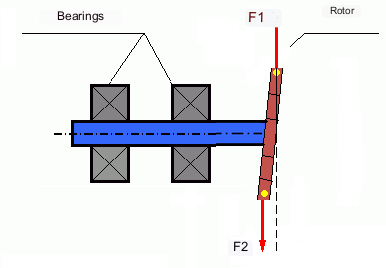
Fig.4 Dezechilibrul dinamic al rotorului îngust.
Forțele F1 și F2 nu se află pe aceeași linie și nu se compensează reciproc.
Din cauza faptului că brațul de creare a cuplului este mic din cauza rotorului îngust, pot fi necesare greutăți de corecție mari. Cu toate acestea, acest lucru duce, de asemenea, la un "dezechilibru indus" din cauza deformării rotorului îngust de către forțele centrifuge generate de greutățile de corecție. (A se vedea, de exemplu, "Instrucțiuni metodologice pentru echilibrarea rotoarelor rigide (conform ISO 22061-76)". Secțiunea 10. SISTEMUL DE SUSȚINERE A ROTORULUI. )
Acest lucru este vizibil pentru rotoarele înguste ale ventilatoarelor, în care, pe lângă dezechilibrul de forță, este activ și dezechilibrul aerodinamic. Și trebuie să se înțeleagă că dezechilibrul aerodinamic, sau mai degrabă forța aerodinamică este direct proporțională cu viteza unghiulară a rotorului, iar pentru compensarea acesteia se folosește forța centrifugă a masei de corecție, care este proporțională cu pătratul vitezei unghiulare. Prin urmare, efectul de echilibrare poate avea loc numai la o anumită frecvență de echilibrare. La alte frecvențe de rotație există o eroare suplimentară.
Același lucru se poate spune și despre forțele electromagnetice dintr-un motor electric, care sunt, de asemenea, proporționale cu viteza unghiulară. Așadar, nu este posibil să se elimine toate cauzele de vibrații dintr-o mașină prin echilibrare.
Vibrarea mecanismelor.
Vibrația este reacția structurii mecanismului la efectele unei forțe excitatoare ciclice. Această forță poate fi de natură diferită.
Forța centrifugă care rezultă din rotorul dezechilibrat este o forță necompensată care acționează asupra "punctului greu". Această forță și vibrațiile cauzate de ea pot fi eliminate prin echilibrarea rotorului.
Forțele de interacțiune de natură "geometrică" care rezultă din erori de fabricație și de asamblare a pieselor care se îmbină. Aceste forțe pot apărea, de exemplu, ca urmare a nerotunjimii gâturilor de arbore, a erorilor în profilurile dinților din angrenaje, a ondulației căilor de rulare ale rulmenților, a nealinierii arborilor corespondenți etc. În cazul necircularității butucilor, axa arborelui va fi deplasată în funcție de unghiul de rotație al arborelui. Deși această vibrație apare și la turația rotorului, este aproape imposibil să o eliminăm prin echilibrare.
Forțele aerodinamice care rezultă din rotația rotoarelor ventilatoarelor și a altor mecanisme cu palete. Forțe hidrodinamice care rezultă din rotația rotoarelor pompelor hidraulice, turbinelor etc.
Forțele electromagnetice care rezultă din funcționarea mașinilor electrice, de exemplu, înfășurări asimetrice ale rotorului, înfășurări scurtcircuitate etc.
Magnitudinea vibrației (de exemplu, amplitudinea Av) depinde nu numai de forța de excitație Fv care acționează asupra mecanismului cu frecvența circulară ω, ci și de rigiditatea k a mecanismului, de masa m a acestuia, precum și de coeficientul de amortizare C.
Pentru măsurarea vibrațiilor și a mecanismelor de echilibrare pot fi utilizate diferite tipuri de senzori, printre care:
senzori absoluți de vibrații concepuți pentru a măsura accelerația vibrațiilor (accelerometre) și senzori de viteză a vibrațiilor;
senzori de vibrații relative - curenți turbionari sau capacitivi, concepuți pentru a măsura deplasarea vibrațiilor. În unele cazuri (atunci când designul mecanismului o permite), se pot utiliza și senzori de forță pentru a evalua sarcina de vibrație a acestuia. În special, aceștia sunt utilizați pe scară largă pentru a măsura sarcina de vibrație a suporturilor mașinilor de echilibrare cu rulmenți tari.
Așadar, vibrația este reacția unei mașini la acțiunea unor forțe externe. Magnitudinea vibrațiilor depinde nu numai de magnitudinea forței care acționează asupra mecanismului, ci și de rigiditatea construcției mecanismului. Una și aceeași forță poate duce la vibrații diferite. La o mașină cu rulmenți tari, chiar dacă vibrațiile sunt mici, rulmenții pot fi supuși unor sarcini dinamice semnificative. De aceea, la echilibrarea mașinilor cu rulmenți tari se utilizează mai degrabă senzori de forță decât senzori de vibrații (accelerometre de vibrații).
Senzorii de vibrații sunt utilizați pe mecanisme cu suporturi relativ flexibile, atunci când acțiunea forțelor centrifuge dezechilibrate duce la o deformare vizibilă a suporturilor și la vibrații. Senzorii de forță se utilizează pentru suporturi rigide, atunci când chiar și forțele semnificative datorate dezechilibrului nu conduc la vibrații semnificative.
Rezonanța este un factor care împiedică echilibrarea
Am menționat mai devreme că rotoarele sunt împărțite în rigide și flexibile. Rigiditatea sau flexibilitatea rotorului nu trebuie confundată cu rigiditatea sau mobilitatea suporturilor (fundației) pe care este instalat rotorul. Un rotor este considerat rigid atunci când deformarea (încovoierea) sa sub acțiunea forțelor centrifuge poate fi neglijată. Deformarea unui rotor flexibil este relativ mare și nu poate fi neglijată.
În acest articol, luăm în considerare doar echilibrarea rotorilor rigizi. Un rotor rigid (nedeformabil) poate fi, la rândul său, montat pe suporturi rigide sau mobile (flexibile). Este clar că această rigiditate/suspensibilitate a suporturilor este, de asemenea, relativă, în funcție de viteza rotorului și de amploarea forțelor centrifuge rezultate. O limită condiționată este reprezentată de frecvența vibrațiilor naturale ale suporturilor rotorului.
În cazul sistemelor mecanice, forma și frecvența vibrațiilor naturale sunt determinate de masa și elasticitatea elementelor sistemului mecanic. Altfel spus, frecvența vibrațiilor naturale este o caracteristică internă a sistemului mecanic și nu depinde de forțele externe. Fiind deviate de la starea de echilibru, suporturile datorită elasticității tind să revină în poziția de echilibru. Dar, din cauza inerției rotorului masiv, acest proces este de natura unor oscilații amortizate. Aceste vibrații sunt vibrațiile naturale ale sistemului rotor-susținere. Frecvența lor depinde de raportul dintre masa rotorului și elasticitatea suporturilor.
Atunci când rotorul începe să se rotească și frecvența de rotație se apropie de frecvența vibrațiilor naturale, amplitudinea vibrațiilor crește brusc, ceea ce poate duce la distrugerea structurii.
Se produce fenomenul de rezonanță mecanică. În zona de rezonanță, o modificare a vitezei de rotație cu 100 rpm poate duce la o creștere a vibrațiilor de zeci de ori. În același timp (în zona de rezonanță), faza de vibrație se modifică cu 180°.
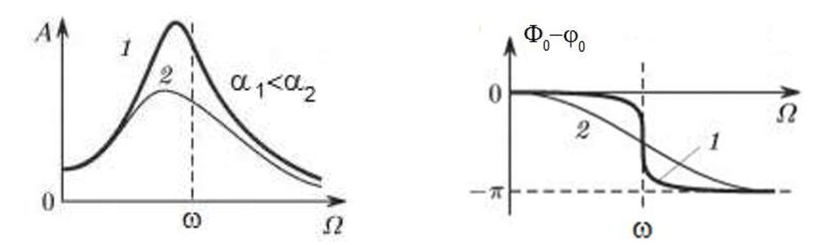
Fig.5 Modificări ale amplitudinii și fazei oscilațiilor unui sistem mecanic la modificarea frecvenței unei forțe exterioare.
În cazul în care proiectarea mecanismului nu este reușită și frecvența de funcționare a rotorului este apropiată de frecvența vibrațiilor naturale, atunci funcționarea mecanismului devine imposibilă din cauza vibrațiilor inadmisibil de mari. Acest lucru nu este posibil în mod obișnuit, deoarece chiar și o mică modificare a vitezei va provoca o schimbare drastică a parametrilor de vibrație. Pentru echilibrarea în zona de rezonanță, se folosesc metode speciale care nu sunt luate în considerare în acest articol.
Este posibil să se determine frecvența vibrațiilor naturale ale mecanismului în regim de coastă (la oprirea rotației rotorului) sau prin metoda șocului, cu analiza spectrală ulterioară a răspunsului sistemului la șoc.
Pentru mecanismele a căror frecvență de rotație este mai mare decât frecvența de rezonanță, adică funcționează în regim de rezonanță, se consideră că suporturile sunt în mișcare, iar pentru măsurare se folosesc senzori de vibrații, în principal vibroacelerometre, care măsoară accelerația elementelor structurale. Pentru mecanismele care funcționează în regim de prerezonanță, suporturile sunt considerate rigide. În acest caz, se utilizează senzori de forță.
Modele liniare și neliniare ale unui sistem mecanic. Non-linearitatea este un factor care împiedică echilibrarea
La echilibrarea rotoarelor rigide, pentru calculele de echilibrare se utilizează modele matematice numite modele liniare. Un model liniar înseamnă că, într-un astfel de model, o mărime este proporțională (liniară) cu cealaltă. De exemplu, dacă masa necompensată de pe rotor este dublată, atunci valoarea vibrației va fi, de asemenea, dublată. Pentru rotoarele rigide, se poate utiliza un model liniar, deoarece acestea nu se deformează.
În cazul rotorilor flexibili, modelul liniar nu mai poate fi utilizat. În cazul unui rotor flexibil, dacă masa punctului greu crește în timpul rotației, se va produce o deformare suplimentară și, în plus față de masă, va crește și raza de amplasare a punctului greu. Prin urmare, pentru un rotor flexibil, vibrațiile vor crește de peste două ori, iar metodele obișnuite de calcul nu vor funcționa.
De asemenea, schimbarea elasticității suporturilor la deformările mari ale acestora, de exemplu, atunci când la deformările mici ale suporturilor lucrează unele elemente structurale, iar la cele mari sunt implicate alte elemente structurale. De aceea, nu se pot echilibra mecanisme care nu sunt fixate pe o fundație, ci, de exemplu, pur și simplu așezate pe podea. În cazul unor vibrații semnificative, forța de dezechilibru poate trage mecanismul de pe podea, modificând astfel semnificativ caracteristicile de rigiditate ale sistemului. Picioarele motorului trebuie să fie bine fixate, monturile cu șuruburi trebuie să fie bine strânse, grosimea șaibelor trebuie să asigure o rigiditate suficientă a montajului etc. În cazul în care rulmenții sunt rupți, sunt posibile o dezaliniere semnificativă a arborelui și șocuri, ceea ce va duce, de asemenea, la o liniaritate slabă și la imposibilitatea de a efectua un echilibru de calitate.
Dispozitive de echilibrare și mașini de echilibrare
După cum s-a menționat mai sus, echilibrarea este procesul de aliniere a axei centrale principale de inerție cu axa de rotație a rotorului.
Acest proces poate fi realizat prin două metode.
Prima metodă implică prelucrarea butucilor rotorului astfel încât axa care trece prin centrele butucilor să aibă o secțiune transversală cu axa centrală principală de inerție a rotorului. O astfel de tehnică este rar utilizată în practică și nu va fi discutată în detaliu în acest articol.
Cea de-a doua metodă (cea mai comună) implică deplasarea, instalarea sau îndepărtarea greutăților de corecție de pe rotor, care sunt plasate astfel încât axa de inerție a rotorului să fie cât mai aproape posibil de axa de rotație a acestuia.
Deplasarea, adăugarea sau îndepărtarea greutăților de corecție în timpul echilibrării poate fi realizată prin diverse operațiuni tehnologice, inclusiv: găurire, frezare, surfilare, sudare, înșurubare sau deșurubare, ardere cu laser sau fascicul de electroni, electroliză, surfilare electromagnetică etc.
Procesul de echilibrare poate fi realizat în două moduri:
- echilibrarea rotoarelor asamblate (în rulmenții proprii) cu ajutorul mașinilor de echilibrare;
- echilibrarea rotorilor pe mașini de echilibrare. Pentru echilibrarea rotoarelor în rulmenții proprii se utilizează de obicei dispozitive de echilibrare specializate (truse), care permit măsurarea vibrațiilor rotorului echilibrat la frecvența sa de rotație în formă vectorială, adică măsurarea atât a amplitudinii, cât și a fazei vibrațiilor. În prezent, dispozitivele de mai sus sunt fabricate pe baza tehnologiei microprocesorului și (în afară de măsurarea și analiza vibrațiilor) asigură calculul automat al parametrilor greutăților de corecție, care ar trebui instalate pe rotor pentru a compensa dezechilibrul acestuia.
Aceste dispozitive includ:
- o unitate de măsurare și de calcul bazată pe un calculator sau un controler industrial;
- Doi (sau mai mulți) senzori de vibrații;
- Un senzor de unghi de fază;
- accesorii pentru montarea senzorilor pe amplasament;
- software specializat, conceput pentru a efectua un ciclu complet de măsurare a parametrilor de vibrație ai rotorului într-unul, două sau mai multe planuri de corecție.
În prezent, două tipuri de mașini de echilibrare sunt cele mai răspândite:
- Mașini cu rulmenți moi (cu suporturi moi);
- Mașini cu rulmenți tari (cu suporturi rigide).
Mașinile cu rulmenți moi au suporturi relativ flexibile, de exemplu, bazate pe arcuri plate. Frecvența vibrațiilor naturale ale acestor suporturi este de obicei de 2-3 ori mai mică decât frecvența de rotație a rotorului de echilibrare, care este montat pe ele. La măsurarea vibrațiilor suporturilor prerezonante ale mașinii se utilizează de obicei senzori de vibrații (accelerometre, senzori de viteză de vibrație etc.).
Mașinile de echilibrare cu prerezonanță utilizează suporturi relativ rigide, ale căror frecvențe proprii de vibrație trebuie să fie de 2-3 ori mai mari decât frecvența de rotație a rotorului care se echilibrează. Pentru a măsura sarcina de vibrație a suporturilor mașinilor de prerezonanță se utilizează de obicei traductoare de forță.
Avantajul mașinilor de echilibrare cu prerezonanță este că echilibrarea pe acestea poate fi efectuată la viteze relativ mici ale rotorului (până la 400 - 500 rpm), ceea ce simplifică foarte mult proiectarea mașinii și a fundației acesteia și crește productivitatea și siguranța echilibrării.
Echilibrarea rotoarelor rigide
Important!
- Echilibrarea elimină doar vibrațiile cauzate de distribuția asimetrică a masei rotorului în raport cu axa de rotație a acestuia. Alte tipuri de vibrații nu sunt eliminate prin echilibrare!
- Mecanismele tehnice, a căror proiectare asigură absența rezonanțelor la frecvența de funcționare a rotației, fixate în mod fiabil pe fundație, instalate în rulmenți care pot fi întreținuți, fac obiectul echilibrării.
- Mașinile defecte trebuie reparate înainte de echilibrare. În caz contrar, nu este posibilă o echilibrare de calitate.
Echilibrarea nu poate înlocui reparația!
Sarcina principală a echilibrării este de a găsi masa și amplasarea greutăților de compensare care sunt supuse forțelor centrifuge de echilibrare.
După cum s-a menționat mai sus, pentru rotoarele rigide, este în general necesar și suficient să se instaleze două greutăți de compensare. Acest lucru va elimina atât dezechilibrul static, cât și cel dinamic al rotorului. Schema generală de măsurare a vibrațiilor în timpul echilibrării este următoarea.
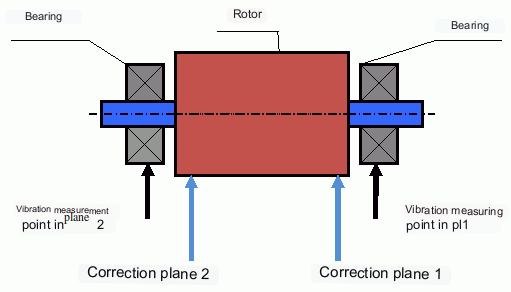
Fig. 6 Selectarea punctelor de măsurare și amplasarea greutăților (planuri de corecție) la echilibrarea în două planuri
Senzorii de vibrații sunt instalați pe suporturile de rulmenți în punctele 1 și 2. Pe rotor se atașează un marker de revoluție, de obicei cu bandă reflectorizantă. Marcajul de turație este utilizat de tahometrul cu laser pentru a determina viteza rotorului și faza semnalului de vibrație.
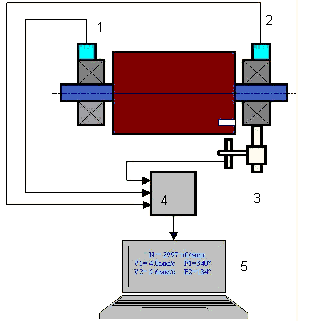
Fig. 7. Instalarea senzorilor la echilibrarea în două planuri. 1,2 - senzori de vibrații, 3 - marker, 4 - unitate de măsură, 5 - notebook
În majoritatea cazurilor, echilibrarea dinamică se realizează prin metoda celor trei porniri. Metoda se bazează pe faptul că pe rotor se plasează greutăți de încercare cu greutate cunoscută, în serie, în planul 1 și 2, iar greutățile și amplasarea greutăților de echilibrare se calculează pe baza rezultatelor modificărilor parametrilor de vibrație.
Locul de instalare a greutăților se numește planul de corecție. De obicei, planurile de corecție sunt selectate în zona suporturilor de rulmenți pe care este instalat rotorul.
La prima pornire se măsoară vibrația inițială. Apoi, se plasează o greutate de testare cu greutate cunoscută pe rotor, mai aproape de unul dintre rulmenți. Se efectuează o a doua pornire și se măsoară parametrii de vibrație, care ar trebui să se modifice ca urmare a instalării greutății de testare. Apoi se îndepărtează greutatea de încercare din primul plan și se instalează în al doilea plan. Se efectuează o a treia pornire de testare și se măsoară parametrii de vibrație. Se îndepărtează greutatea de testare, iar software-ul calculează automat masele și unghiurile de instalare a greutăților de echilibrare.
Scopul instalării greutăților de testare este de a determina modul în care sistemul reacționează la schimbările de dezechilibru. Greutățile și locațiile greutăților de testare sunt cunoscute, astfel încât software-ul poate calcula așa-numiții coeficienți de influență, arătând modul în care introducerea unui dezechilibru cunoscut afectează parametrii de vibrație. Coeficienții de influență sunt caracteristici ale sistemului mecanic propriu-zis și depind de rigiditatea suporturilor și de masa (inerția) sistemului rotor-suport.
Pentru același tip de mecanisme de același design, coeficienții de influență vor fi apropiați. Este posibilă salvarea acestora în memoria calculatorului și utilizarea lor pentru echilibrarea mecanismelor de același tip fără teste, ceea ce crește semnificativ productivitatea echilibrării. Rețineți că masa greutăților de încercare trebuie aleasă astfel încât parametrii de vibrație să se modifice în mod vizibil atunci când sunt instalate greutățile de încercare. În caz contrar, eroarea de calcul a coeficienților de influență crește și calitatea echilibrării se deteriorează.
După cum se poate observa în figura 1, forța centrifugă acționează în direcția radială, adică perpendicular pe axa rotorului. Prin urmare, senzorii de vibrații trebuie să fie instalați astfel încât axa lor de sensibilitate să fie orientată, de asemenea, în direcția radială. De obicei, rigiditatea fundației în direcția orizontală este mai mică, astfel încât vibrația în direcția orizontală este mai mare. Prin urmare, pentru a crește sensibilitatea, senzorii trebuie să fie instalați astfel încât axa lor de sensibilitate să fie orientată, de asemenea, în direcție orizontală. Deși nu există o diferență fundamentală. În plus față de vibrațiile în direcția radială, trebuie monitorizate și vibrațiile în direcția axială, de-a lungul axei de rotație a rotorului. Această vibrație nu este de obicei cauzată de dezechilibru, ci de alte cauze, legate în principal de nealinierea și nealinierea arborilor conectați prin intermediul cuplajului.
Această vibrație nu poate fi eliminată prin echilibrare, caz în care este necesară alinierea. În practică, astfel de mașini au de obicei atât dezechilibru al rotorului, cât și nealiniere a arborelui, ceea ce face ca sarcina de eliminare a vibrațiilor să fie mult mai dificilă. În astfel de cazuri, este necesară mai întâi centrarea mașinii și apoi echilibrarea acesteia. (Deși în cazul unui dezechilibru puternic al cuplului, vibrațiile apar și în direcția axială din cauza "răsucirii" structurii de fundație).
Exemple de bancuri pentru echilibrarea rotoarelor mici pe care le-am discutat în alte articole ale noastre:
Stand de echilibrare cu suport moale.
Echilibrarea rotoarelor motoarelor electrice.
Standuri de echilibrare simple, dar eficiente
Criterii de evaluare a calității mecanismelor de echilibrare.
Calitatea de echilibrare a rotoarelor (mecanismelor) poate fi evaluată în două moduri. Prima metodă presupune compararea valorii dezechilibrului rezidual determinat în timpul procesului de echilibrare cu toleranța pentru dezechilibru rezidual. Aceste toleranțe pentru diferitele clase de rotoare sunt specificate în ISO 1940-1-2007. Partea 1. Definiția dezechilibrului admisibil.
Cu toate acestea, respectarea toleranțelor specificate nu poate garanta pe deplin fiabilitatea operațională a mecanismului, asociată cu atingerea nivelului minim de vibrații al acestuia. Acest lucru se explică prin faptul că amploarea vibrațiilor mecanismului este determinată nu numai de mărimea forței asociate cu dezechilibrul rezidual al rotorului său, ci depinde și de alți câțiva parametri, printre care: rigiditatea k a elementelor structurale ale mecanismului, masa m a acestuia, factorul de amortizare, precum și frecvența de rotație. Prin urmare, pentru a estima calitățile dinamice ale mecanismului (inclusiv calitatea echilibrului său), într-o serie de cazuri se recomandă să se estimeze nivelul de vibrații reziduale ale mecanismului, care este reglementat de o serie de standarde.
Cel mai frecvent standard care reglementează nivelurile admisibile de vibrații ale mecanismelor este ISO 10816-3-2002. Cu ajutorul acestuia, este posibil să se stabilească toleranțe pentru orice tip de mașini, ținând cont de puterea acționării electrice a acestora.
În plus față de acest standard universal, există o serie de standarde specializate elaborate pentru anumite tipuri de mașini. De exemplu, 31350-2007 , ISO 7919-1-2002, etc.
ISO 1940-1-2007. "Vibrații. Cerințe privind calitatea de echilibrare a rotorilor rigizi. Partea 1. Determinarea dezechilibrului admisibil".
ISO 10816-3:2009 Previzualizare Vibrații mecanice - Evaluarea vibrațiilor mașinilor prin măsurători pe părți nerotante - Partea 3: Mașini industriale cu putere nominală mai mare de 15 kW și viteze nominale între 120 r/min și 15 000 r/min, măsurate in situ."
ISO 14694:2003 "Ventilatoare industriale - Specificații pentru calitatea echilibrului și nivelurile de vibrații",
ISO 7919-1-2002 "Vibrațiile mașinilor fără mișcare alternativă. Măsurători pe arbori rotativi și criterii de evaluare. Ghid general."