Before starting work in the Two plane balancing mode, it is necessary to install vibration sensors on the machine body at the selected measurement points and connect them to the inputs X1 and X2 of the measuring unit, respectively.
An optical phase angle sensor must be connected to input X3 of the measuring unit. In addition, to use this sensor, a reflective tape must be glued onto the accessible rotor surface of the balancing machine.
Detailed requirements for choosing the installation location of sensors and their mounting at the facility during balancing are set out in Appendix 1.
The work on the program in the “Two plane balancing” mode starts from the Main window of the programs.
Click on the “F3-Two plane” button (or press the F3 key on the computer keyboard).
Further, click on the “F7 – Balancing” button, after which a working window will appear on the computer display (see Fig. 7.13), selection of the archive for saving data when balancing in two planes.
Fig. 7.32 Two plane balancing archive window.
In this window you need to enter the data of the balanced rotor. After pressing the “F10-OK” button, a balancing window will appear.
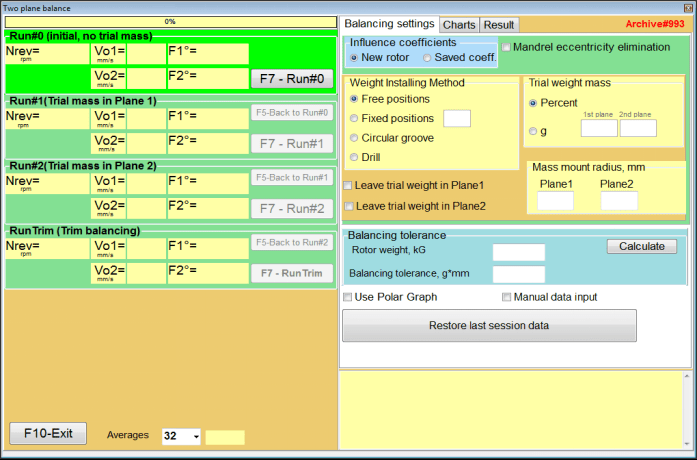
Fig. 7.33. Balancing in two planes window.
On the right side of the window is the “Balancing settings” tab for entering settings before balancing.
• Influence coefficients
Balancing a new rotor or balancing using stored influence coefficients (balancing coefficients)
• Mandrel eccentricity elimination
Balancing with additional start to eliminate the influence of the eccentricity of the mandrel
• Weight Attachment Method
Installation of corrective weights in an arbitrary place on the circumference of the rotor or in a fixed position. Calculations for drilling when removing the mass.
• “Free position” – weights can be installed in an arbitrary angular positions on the circumference of the rotor.
• “Fixed position” – weight can be installed in fixed angular positions on the rotor, for example, on blades or holes (for example 12 holes – 30 degrees), etc. The number of fixed positions must be entered in the appropriate field. After balancing, the program will automatically split the weight into two parts and indicate the number of positions on which it is necessary to establish the masses obtained.
• Trial weight mass
Trial weight
• Leave trial weight in Plane1 / Plane2
Remove or leave trial weight when balancing.
• Mass mount radius, mm
Radius of mounting trial and corrective weights
• Balancing tolerance
Entering or calculating residual imbalance tolerances in g-mm
• Use Polar Graph
Use polar graph to display balancing results
• Manual data input
Manual data entry for calculating balancing weights
• Restore last session data
Recovery of the measurement data of the last session in the event of failure to continue balancing.
Input of the initial data for the New rotor balancing in the “Two plane balancing. Settings”(see Fig. 7.32.).
In this case, in the “Influence coefficients” section, select the “New rotor” item.
Further, in the section “Trial weight mass“, you must select the unit of measurement of the mass of the trial weight – “Gram” or “Percent“.
When choosing the unit of measure “Percent”, all further calculations of the mass of the corrective weight will be performed as a percentage in relation to the mass of the trial weight.
When choosing the “Gram” unit of measurement, all further calculations of the mass of the corrective weight will be performed in grams. Then enter in the windows located to the right of the inscription “Gram” the mass of trial weights that will be installed on the rotor.
Attention!
If it is necessary to use the “Saved coeff.” Mode for further work during initial balancing, the mass of trial weights must be entered in grams.
Then select “Weight Attachment Method” – “Circum” or “Fixed position”.
If you select “Fixed position”, you must enter the number of positions.
The tolerance for residual imbalance (Balancing tolerance) can be calculated in accordance with the procedure described in ISO 1940 Vibration. Balance quality requirements for rotors in a constant (rigid) state. Part 1. Specification and verification of balance tolerances.
Fig. 7.34. Balancing tolerance calculation window
When balancing in two planes in the “New rotor” mode, balancing requires three calibration runs and at least one test run of the balancing machine.
The vibration measurement at the first start of the machine is performed in the “Two plane balance” working window (see Fig. 7.34) in the “Run#0” section.
Fig. 7.35. Measurement results at balancing in two planes after the initial run.
Attention!
Before starting the measurement, it is necessary to turn on the rotation of the rotor of the balancing machine (first run) and make sure that it has entered the operating mode with a stable speed.
To measure vibration parameters in the Run#0 section, click on the “F7 – Run#0” button (or press the F7 key on a computer keyboard)
The results of measuring the rotor speed (RPM), the value RMS (VО1, VО2) and phases (F1, F2) of 1x vibration appearing appear in the corresponding windows of the Run#0 section.
Before starting to measure vibration parameters in the “Run#1.Trial mass in Plane1” section, you should stop the rotation of the rotor of the balancing machine and install a trial weight on it, the mass selected in the “Trial weight mass” section.
Attention!
1. The question of choosing the mass of trial weights and their installation places on the rotor of a balancing machine is discussed in detail in Appendix 1.
2. If it is necessary to use the Saved coeff. Mode in future work, the place for installing the trial weight must necessarily coincide with the place for installing the mark used to read the phase angle.
After this, it is necessary to turn on the rotation of the rotor of the balancing machine again and make sure that it has entered the operating mode.
To measure vibration parameters in the “Run # 1.Trial mass in Plane1” section (see Fig. 7.25), click on the “F7 – Run#1” button (or press the F7 key on the computer keyboard).
Upon successful completion of the measurement process, you are returned to the tab of measurement results (see Fig. 7.25).
In this case, in the corresponding windows of the “Run#1. Trial mass in Plane1” section, the results of measuring the rotor speed (RPM), as well as the value of the components of the RMS (Vо1, Vо2) and phases (F1, F2) of 1x vibration.
Before starting to measure vibration parameters in the section “Run # 2.Trial mass in Plane2“, you must perform the following steps:
– stop the rotation of the rotor of the balancing machine;
– remove the trial weight installed in plane 1;
– install on a trial weight in plane 2, the mass selected in the section “Trial weight mass“.
After this, turn on the rotation of the rotor of the balancing machine and make sure that it has entered the operating speed.
To begin the measurement of vibration in the “Run # 2.Trial mass in Plane2” section (see Fig. 7.26), click on the “F7 – Run # 2” button (or press the F7 key on the computer keyboard). Then the “Result” tab opens.
In the case of using the Weight Attachment Method” – “Free positions, the display shows the values of the masses (M1, M2) and installation angles (f1, f2) of the corrective weights.
Fig. 7.36. Results of calculation of corrective weights – free position
Fig. 7.37. Results of calculation of corrective weights – free position.
Polar diagram
In the case of using the Weight Attachment Method” – “Fixed positions
Fig. 7.37. Results of calculation of corrective weights – fixed position.
Fig. 7.39. Results of calculation of corrective weights – fixed position.
Polar diagram.
In the case of using the Weight Attachment Method” – “Circular groove”
Fig. 7.40. Results of calculation of corrective weights – Circular groove.
Attention!:
1. After completing the measurement process on the RUN#2 of the balancing machine, stop the rotation of the rotor and remove the trial weight previously installed. Then you can to install (or remove) corrective weights.
2. The angular position of the corrective weights in the polar coordinate system is counted from the place of installation of the trial weight in the direction of rotation of the rotor.
3. In the case of “Fixed position” – the 1st position (Z1), coincides with the place of installation of the trial weight. The counting direction of the position number is in the direction of rotation of the rotor.
4. By default the corrective weight will be added to the rotor. This is indicated by the label set in the “Add” field. If removing the weight (for example, by drilling), you must set a mark in the “Delete” field, after which the angular position of the correction weight will automatically change by 180º.
After installing the correction weight on the balancing rotor it is necessary to carry out a RunC (trim) and evaluate the effectiveness of the performed balancing.
Attention!
Before starting the measurement at the test run, it is necessary to turn on the rotation of the rotor of the machine and make sure that it has entered the operating speed.
To measure vibration parameters in the RunTrim (Check balance quality) section (see Fig. 7.37), click on the “F7 – RunTrim” button (or press the F7 key on the computer keyboard).
The results of measuring the rotor rotation frequency (RPM), as well as the value of the RMS component (Vо1) and phase (F1) of 1x vibration will be shown.
The “Result” tab appears on right side of the working window with the table of measurement results (see Fig. 7.37), which displays the results of calculating the parameters of additional corrective weights.
These weights can be added to corrective weights that are already installed on the rotor to compensate for residual imbalance.
In addition, the residual rotor unbalance achieved after balancing is displayed in the lower part of this window.
In the case when the values of the residual vibration and / or residual unbalance of the balanced rotor satisfy the tolerance requirements established in the technical documentation, the balancing process can be completed.
Otherwise, the balancing process may continue. This allows the method of successive approximations to correct possible errors that may occur during the installation (removal) of the corrective weight on a balanced rotor.
When continuing the balancing process on the balancing rotor, it is necessary to install (remove) additional corrective mass, the parameters of which are indicated in the “Result” window.
In the “Result” window there are two control buttons can be used – “F4-Inf.Coeff“, “F5 – Change correction planes“.
The “F4-Inf.Coeff” button (or the F4 function key on the computer keyboard) is used to view and save rotor balancing coefficients in the computer memory, calculated from the results of two calibration starts.
When it is pressed, the “Influence coefficients (two planes)” working window appears on the computer display (see Fig. 7.40), in which balancing coefficients calculated based on the results of the first three calibration starts are displayed.
Fig. 7.41. Working window with balancing coefficients in 2 planes.
In the future, when balancing of such type of the machine it is supposed, require to use the “Saved coeff.” mode and balancing coefficients stored in the computer memory.
To save coefficients, click the “F9 – Save” button and go to the “Influence coefficients archive (2planes)” windows (see Fig. 7.42)
Fig. 7.42. The second page of the working window with balancing coefficients in 2 planes.
The “F5 – Change correction planes” button is used when require change the position of the correction planes, when it is necessary to recalculate the masses and installation angles
corrective weights.
This mode is primarily useful when balancing rotors of complex shape (for example, crankshafts).
When this button is pressed, the working window “Recalculation of correction weights mass and angle to other correction planes” is displayed on the computer display (see Fig. 7.42).
In this working window, you should select one of the 4 possible options by clicking corresponding picture.
The original correction planes (Н1 and Н2) in Fig. 7.29 are marked in green, and new (K1 and K2), for which it recounts, in red.
Then, in the “Calculation data” section, enter the requested data, including:
– the distance between the corresponding correction planes (a, b, c);
– new values of the radii of the installation of corrective weights on the rotor (R1 ’, R2’).
After entering the data, you must press the button “F9-calculate“
The calculation results (masses M1, M2 and installation angles of corrective weights f1, f2) are displayed in the corresponding section of this working window (see Fig. 7.42).
Fig. 7.43 Change correction planes. Recalculation of correction mass and angle to other correction planes.
Saved coeff. balancing can be performed on a machine for which balancing coefficients have already been determined and saved in the computer memory.
Attention!
When re-balancing, the vibration sensors and the phase angle sensor must be installed in the same way as during the initial balancing.
Input of initial data for re-balancing begins in the “Two plane balance. Balancing settings”(see Fig. 7.23).
In this case, in the “Influence coefficients” section, select the “Saved coeff.” Item. In this case, the window “Influence coefficients archive (2planes)” will appear (see Fig. 7.30), in which the archive of the previously determined balancing coefficients is stored.
Moving through the table of this archive using the “►” or “◄” control buttons, you can select the desired record with balancing coefficients of the machine of interest to us. Then, to use this data in current measurements, press the “F2 – OK” button and return to the previous working window.
Fig. 7.44. The second page of the working window with balancing coefficients in 2 planes.
After that, the contents of all other windows of the “Balancing in 2 pl. Source data” is filled in automatically.
“Saved coeff.” balancing requires only one tuning start and at least one test start of the balancing machine.
Vibration measurement at the tuning start (Run # 0) of the machine is performed in the “Balancing in 2 planes” working window with a table of balancing results (see Fig. 7.14) in the Run # 0 section.
Attention!
Before starting the measurement, it is necessary to turn on the rotation of the rotor of the balancing machine and make sure that it has entered the operating mode with a stable speed.
To measure vibration parameters in the Run # 0 section, click the “F7 – Run#0” button (or press the F7 key on the computer keyboard).
The results of measuring the rotor speed (RPM), as well as the value of the components of the RMS (VО1, VО2) and phases (F1, F2) of the 1x vibration appear in the corresponding fields of the Run # 0 section.
At the same time, the “Result” tab opens (see Fig. 7.15), which displays the results of calculating the parameters of corrective weights that must be installed on the rotor to compensate for its imbalance.
Moreover, in the case of using the polar coordinate system, the display shows the values of the masses and installation angles of corrective weights.
In the case of decomposition of corrective weights on the blades, the numbers of the blades of the balancing rotor and the mass of weight that need to be installed on them are displayed.
Further, the balancing process is carried out in accordance with the recommendations set out in section 7.6.1.2. for primary balancing.
Attention!:
In case of correction of imbalance by removal of a weight (for example by drilling) it is necessary to establish tag in the field “Removal” then the angular position of the correction weight will change automatically on 180º.
To carry out index balancing, a special option is provided in the Balanset-1A program. When checked Mandrel eccentricity elimination an additional RunEcc section appears in the balancing window.
Fig. 7.45. The working window for Index balancing.
After running Run # 2 (Trial mass Plane 2), a window will appear
Fig. 7.46. Attention windows
After installing the rotor with an 180 turn, Run Ecc must be completed. The program will automatically calculate the true rotor imbalance without affecting the mandrel eccentricity.