Rotor Balancing on Lathes: A Cost-Effective Solution for Improving Product Quality
In modern manufacturing, where product quality is of utmost importance, rotor balancing becomes an essential part of the technological process. However, purchasing specialized balancing equipment can be costly for small and medium-sized enterprises. In this article, we explore the possibility of using lathes for rotor balancing, which can significantly reduce equipment costs and improve production efficiency.
The Lathe as a Tool for Balancing
The lathe, due to its design and functionality, can be successfully used for balancing rotors of various types and sizes. The main advantage of this approach is cost savings, as there is no need to purchase expensive specialized equipment. Additionally, using a lathe allows for balancing to be carried out directly during the rotor’s manufacturing process, which shortens production time and improves product quality. It is important to note that for effective balancing, the rotor’s mass should be comparable to the mass of the lathe spindle.
Preparation for Balancing
Before starting the balancing process, several preparatory steps must be taken:
- Choosing the appropriate lathe: The lathe should have sufficient rigidity and precision to ensure reliable rotor mounting and accurate vibration measurements.
- Installing the measurement system: To measure rotor vibration on the lathe, a portable balancer such as the Balanset-1A can be used. It includes vibration sensors, a tachometer, and software for data analysis and corrective mass calculation.
- Balancing the spindle: An important step in preparation is balancing the lathe spindle itself. This is necessary to eliminate the influence of its own imbalance on the measurement results.
In this article, I will detail our experience and methodology in dynamically balancing rubberized shafts on a lathe machine – a solution that, admittedly, I was initially skeptical of due to the inherent rigidity and substantial weight of such machinery. Surprisingly, the operation was seamlessly executed, achieving an precision level of g 6.3 as per ISO 1940 standards.
Rotor Balancing Process on a Lathe in theory
The rotor balancing process on a lathe involves the following steps:
Securing the Rotor
The rotor is securely mounted in the lathe chuck or on centers to ensure stability during the balancing process.
Installing Sensors
Vibration sensors are installed on the bearing supports or the lathe body, and a tachometer is aimed at a reflective tape attached to the rotor.
Measuring Initial Vibration
The initial vibration level of the rotor is measured at its operating speed.
Installing a Test Weight
A test weight of known mass is installed on the rotor, and the vibration is measured again.
Calculating Corrective Masses
The Balanset-1A software analyzes the measurement results and calculates the necessary corrective masses and their placement angles.
Correcting Rotor Mass
Depending on the rotor’s design and the lathe’s capabilities, mass correction can be performed by drilling, milling, welding, or other methods.
Balancing Verification
After making corrections, a control vibration measurement is conducted. The process is repeated if necessary until the required balance level is achieved.
Accounting for Eccentricity
After balancing, it is important to account for eccentricity by rotating the rotor in the fixture by 180 degrees and repeating the measurement. The Balanset-1A software includes a special function for eccentricity compensation.
Dynamic Balancing Process on practice:
- Rotation Frequency: Typically, the working rotation speed of this shafts ranges between 300 to 500 revolutions per minute (rpm). In this particular case, we carried out the balancing at 550 rpm.
- Setup: The rubberized shaft was mounted on the lathe machine, followed by the strategic placement of sensors, as depicted in the accompanying photographs.
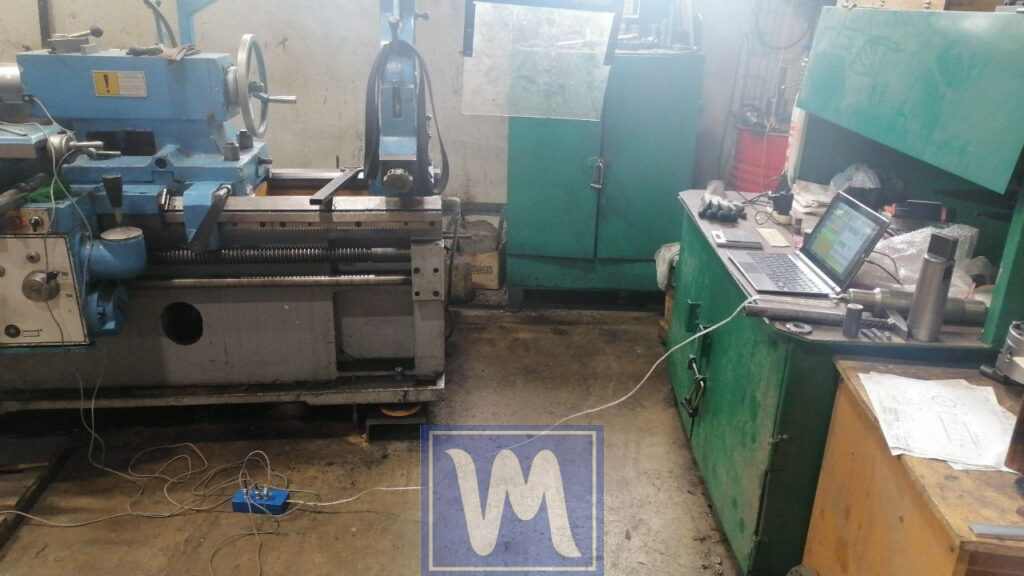
On-Site Dynamic Balancing of Rubberized Shafts Using a Lathe Machine
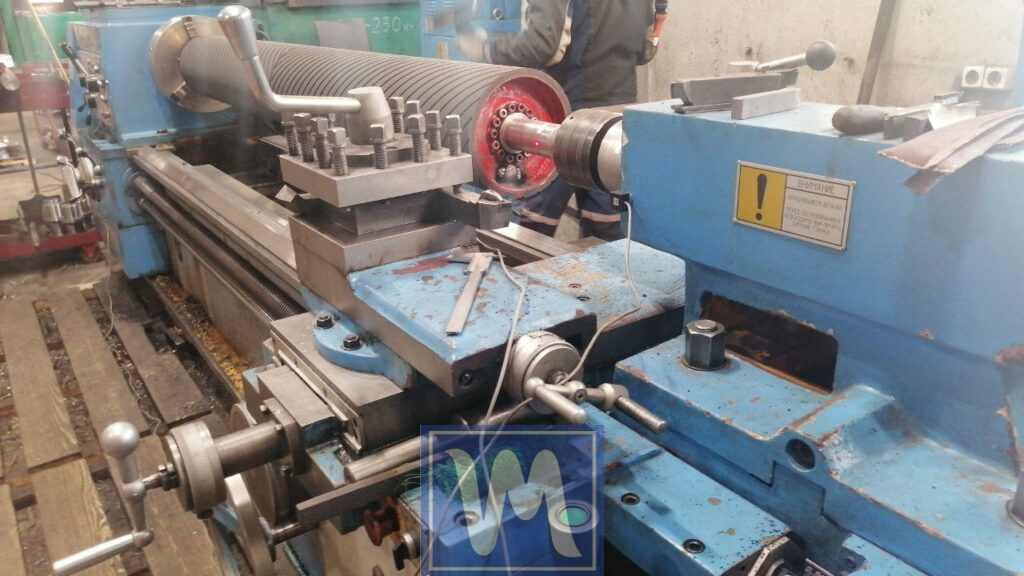
Dynamic Balancing of Rubberized Shafts
-
- Initial Vibration Readings: Before balancing, the vibration readings stood at 9 mm/sec and 17 mm/sec.
- Trial Weight: A trial weight of 340 grams was welded. This was sufficient to alter the vibration and phase readings by roughly 10%.
- Balancing Adjustments: Post the trial runs with the test weight, our Balanset-1A instrument indicated the need for the addition of 3100 grams on one side of the shaft and 4300 grams on the other. After these adjustments, vibration levels decreased to 2 mm/sec and 4 mm/sec.
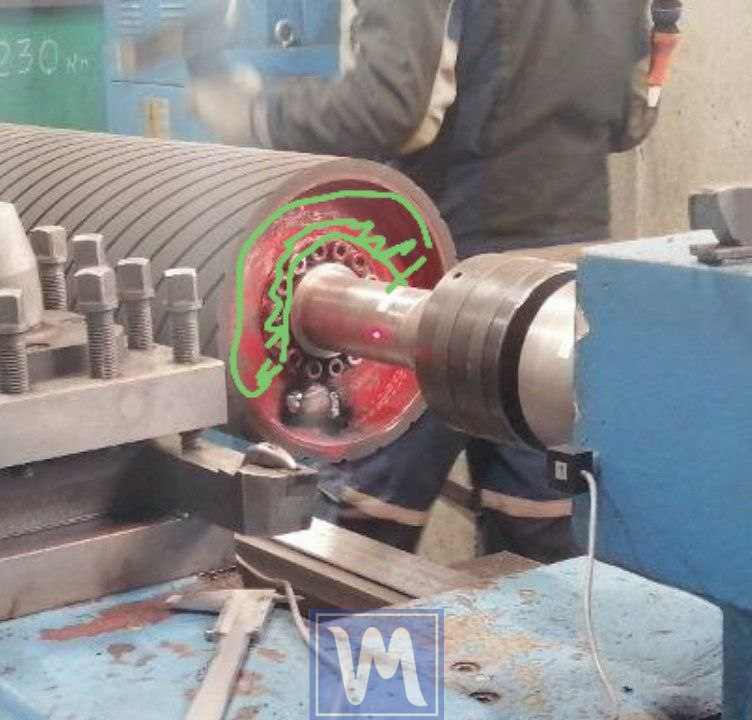
On-Site Dynamic Balancing of Rubberized Shafts Using a Lathe Machine
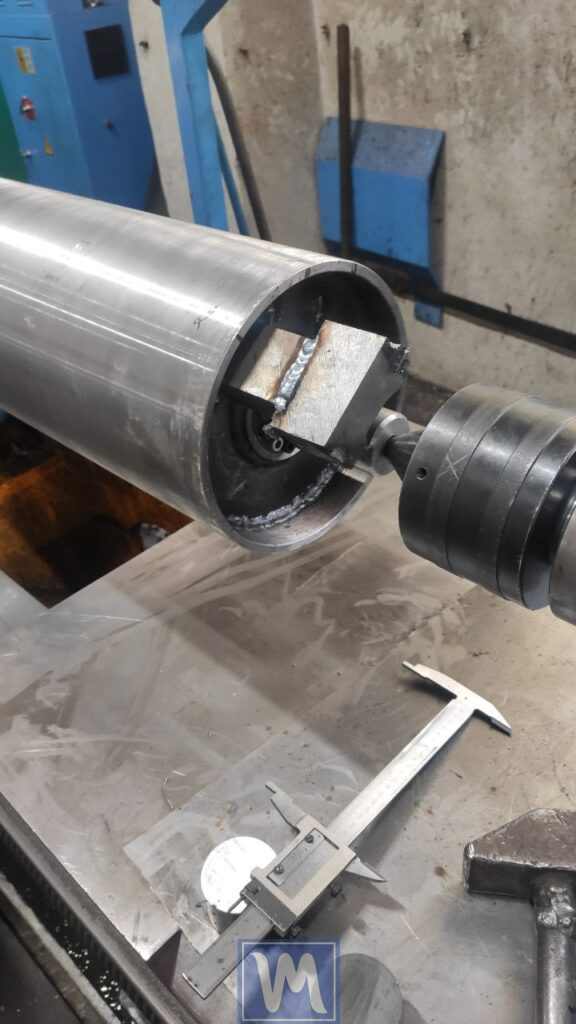
On-Site Dynamic Balancing of Rubberized Shafts Using a Lathe Machine
- Fine-tuning: To further optimize results, we proceeded to add weights of 400 grams and 700 grams. Subsequently, another round of fine-tuning was executed by adding 200 grams and 400 grams. Due to spatial constraints, the weights were welded atop one another. Ultimately, these temporary weights were replaced with precision-cut, aesthetically pleasing counterweights crafted specifically for this shaft. The final vibration readings were an impressive 0.1 mm/sec in both planes.
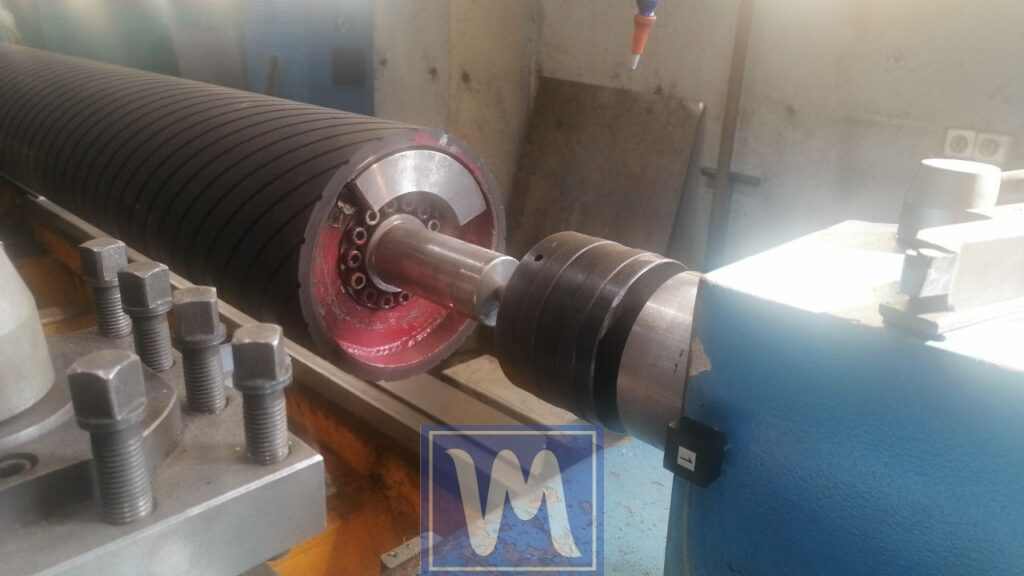
On-Site Dynamic Balancing of Rubberized Shafts Using a Lathe Machine

On-Site Dynamic Balancing of Rubberized Shafts Using a Lathe Machine
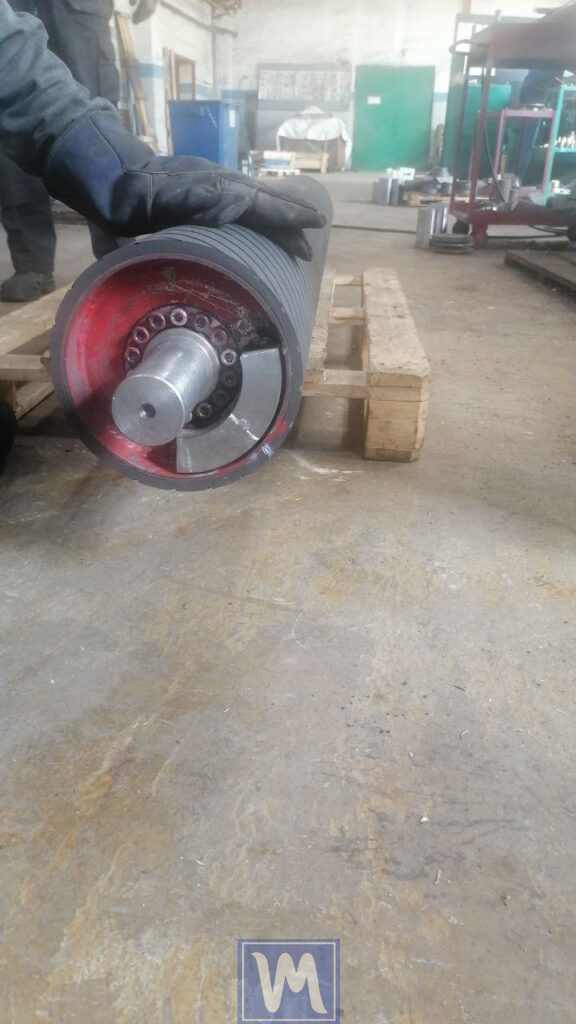
On-Site Dynamic Balancing of Rubberized Shafts Using a Lathe Machine
Advantages of Rotor Balancing on Lathes
Cost-Effectiveness
Using a lathe for balancing avoids the expense of purchasing specialized balancing equipment.
Convenience
Balancing can be performed directly during the rotor’s manufacturing process, reducing production time.
High Quality
Modern portable balancers, such as the Balanset-1A, provide high balancing accuracy, enabling low vibration levels and improved product quality.
Conclusion
Rotor balancing on lathes is an effective and economical solution for businesses seeking to improve product quality and reduce production costs. The use of portable balancers like the Balanset-1A makes this process simple and accessible, even for small workshops.
Important Reminders
- For effective balancing, the rotor’s mass should be comparable to the mass of the lathe spindle.
- Before balancing the rotor, the lathe spindle itself must be balanced to eliminate the influence of its own imbalance on the measurement results.
- To achieve the best results, it is recommended to use high-quality measuring instruments and strictly follow the balancing procedure.
Balancing rotors on lathes is a step towards the future of your production, paying off through improved product quality, reduced costs, and increased competitiveness of your business.
0 Comments